Reflow lehimləmə, bir və ya bir neçə elektrik komponentini müvəqqəti olaraq kontakt yastıqlarına bağlamaq üçün bir lehim pastasının (toz lehim və axınının yapışqan qarışığı) istifadə edildiyi bir prosesdir, bundan sonra bütün montaj lehimi əridən idarə olunan istiliyə məruz qalır. , birgə daimi birləşdirən.İstilik montajı yenidən axıdılan sobadan və ya infraqırmızı lampanın altından keçirməklə və ya ayrı-ayrı birləşmələri isti hava qələmi ilə lehimləməklə həyata keçirilə bilər.
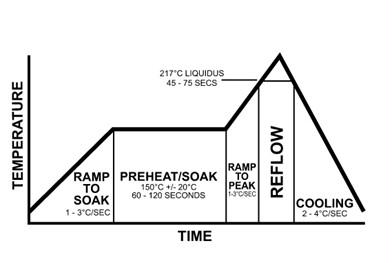
Yenidən lehimləmə, səthə montaj komponentlərini dövrə lövhəsinə bağlamağın ən geniş yayılmış üsuludur, baxmayaraq ki, bu, deşikləri lehim pastası ilə dolduraraq və komponent keçiricilərini pasta vasitəsilə daxil etməklə deşikli komponentlər üçün də istifadə edilə bilər.Dalğalı lehimləmə daha sadə və daha ucuz ola biləcəyi üçün, reflow ümumiyyətlə təmiz deşikli lövhələrdə istifadə edilmir.Tərkibində SMT və THT komponentlərinin qarışığı olan lövhələrdə istifadə edildikdə, deşik vasitəsilə yenidən axın dalğa lehimləmə addımını montaj prosesindən çıxarmağa imkan verir və potensial olaraq montaj xərclərini azaldır.
Yenidən axıdılması prosesinin məqsədi lehimi əritmək və bitişik səthləri qızdırmaq, həddindən artıq istiləşmədən və elektrik komponentlərinə zərər verməməkdir.Adi reflow lehimləmə prosesində, adətən, "zonalar" adlanan dörd mərhələ var, hər biri fərqli bir istilik profilinə malikdir: əvvəlcədən qızdırmaq, termal islatmaq (çox vaxt sadəcə islatmaq üçün qısaldılır), yenidən axıtmaq və soyutma.
Əvvəlcədən isitmə zonası
Maksimum yamac, çap dövrə lövhəsindəki temperaturun nə qədər sürətlə dəyişdiyini ölçən temperatur/zaman nisbətidir.Əvvəlcədən isitmə zonası çox vaxt zonaların ən uzunudur və tez-tez eniş sürətini təyin edir.Yüksəlmə sürəti adətən saniyədə 1,0 °C ilə 3,0 °C arasında olur, tez-tez saniyədə 2,0 °C ilə 3,0 °C (4 °F ilə 5 °F) arasında düşür.Məzənnə maksimum yamacdan artıq olarsa, termal şok və ya çatlama nəticəsində komponentlərin zədələnməsi baş verə bilər.
Lehim pastası da sıçrayış effektinə malik ola bilər.Əvvəlcədən qızdırılan hissə pastadakı həlledicinin buxarlanmağa başladığı yerdir və yüksəlmə sürəti (və ya temperatur səviyyəsi) çox aşağı olarsa, axın uçucularının buxarlanması tamamlanmamışdır.
Termal islatma zonası
İkinci bölmə, termal islatma, adətən, lehim pastası uçucu maddələrinin çıxarılması və axınların aktivləşdirilməsi üçün 60-120 saniyəlik bir məruz qalmadır (flusa bax), burada axın komponentləri komponent keçiricilərində və yastıqlarda oksidləşməyə başlayır.Həddindən artıq yüksək temperatur lehimin sıçramasına və ya toplanmasına, həmçinin pastanın oksidləşməsinə, bərkidici yastıqlara və komponentlərin uclarına səbəb ola bilər.
Eynilə, temperatur çox aşağı olarsa, axınlar tam aktivləşməyə bilər.Islatma zonasının sonunda, yenidən axın zonasından dərhal əvvəl bütün montajın istilik tarazlığı arzu edilir.Müxtəlif ölçülü komponentlər arasında və ya PCB yığımı çox böyükdürsə, hər hansı delta T-ni azaltmaq üçün islatma profili təklif olunur.Sahə massivi tipli paketlərdə boşluqları azaltmaq üçün islatma profili də tövsiyə olunur.
Yenidən axın zonası
Üçüncü bölmə, reflow zonası, həmçinin “yenidən axıdılan vaxt” və ya “likvidusdan yuxarı vaxt” (TAL) adlanır və prosesin maksimum temperatura çatdığı hissəsidir.Mühüm bir məqam, bütün prosesin maksimum icazə verilən temperaturu olan pik temperaturdur.Ümumi pik temperatur mayeləşmədən 20-40 °C yuxarıdır. Bu həd yüksək temperaturlara ən aşağı dözümlülüyə malik montajda olan komponent tərəfindən müəyyən edilir (Termik zədələnməyə ən həssas komponent).Standart təlimat, proses üçün maksimum temperatura çatmaq üçün ən həssas komponentin davam edə biləcəyi maksimum temperaturdan 5 °C çıxarmaqdır.Bu həddi aşmamaq üçün prosesin temperaturunu izləmək vacibdir.
Bundan əlavə, yüksək temperaturlar (260 °C-dən yuxarı) SMT komponentlərinin daxili kalıplarının zədələnməsinə və həmçinin intermetal böyümənin inkişafına səbəb ola bilər.Əksinə, kifayət qədər isti olmayan bir temperatur pastanın adekvat şəkildə yenidən axmasına mane ola bilər.
Likvidusdan yuxarı olan vaxt (TAL) və ya yenidən axıdılmadan yuxarı olan vaxt lehimin nə qədər maye olduğunu ölçür.Flux, metalların qovşağında səthi gərginliyi azaldır, bu da ayrı-ayrı lehim tozu sferalarının birləşməsinə imkan verən metallurgiya əlaqəsini həyata keçirir.Profil vaxtı istehsalçının spesifikasiyasını aşarsa, nəticə lehim birləşməsinin əmələ gəlməsindən əvvəl pastanın effektiv şəkildə "qurutulması" nın vaxtından əvvəl aktivləşdirilməsi və ya istehlakı ola bilər.Qeyri-kafi vaxt/temperatur əlaqəsi axının təmizləyici təsirinin azalmasına səbəb olur, nəticədə zəif nəmlənmə, həlledicinin və axının qeyri-adekvat çıxarılması və ehtimal ki, qüsurlu lehim birləşmələri olur.
Mütəxəssislər adətən mümkün olan ən qısa TAL-ı tövsiyə edirlər, lakin əksər pastalar minimum TAL-ı 30 saniyə göstərir, baxmayaraq ki, bu xüsusi vaxt üçün aydın səbəb yoxdur.Ehtimallardan biri odur ki, PCB-də profilləmə zamanı ölçülməyən yerlər var və buna görə də minimum icazə verilən vaxtı 30 saniyəyə təyin etmək ölçülməmiş sahənin yenidən axmama şansını azaldır.Yüksək minimum təkrar axıdma vaxtı həm də sobanın temperatur dəyişikliklərinə qarşı təhlükəsizlik marjasını təmin edir.Islatma vaxtı ideal olaraq likvidusdan yuxarı 60 saniyədən aşağı qalır.Likvidasiyadan yuxarı əlavə vaxt həddindən artıq intermetal böyüməyə səbəb ola bilər ki, bu da oynaqların kövrəkliyinə səbəb ola bilər.Lövhə və komponentlər, həmçinin mayeləşmə zamanı uzun müddət zədələnə bilər və əksər komponentlərin müəyyən edilmiş maksimum temperatura məruz qalma müddəti üçün dəqiq müəyyən edilmiş vaxt məhdudiyyəti var.
Likvidasiya üzərində çox az vaxt həllediciləri və axını tuta bilər və soyuq və ya darıxdırıcı birləşmələr, eləcə də lehim boşluqları üçün potensial yarada bilər.
Soyutma zonası
Son zona, işlənmiş lövhəni tədricən soyumaq və lehim birləşmələrini bərkitmək üçün soyutma zonasıdır.Düzgün soyutma komponentlərə həddindən artıq intermetal əmələ gəlməsini və ya termal şoku maneə törədir.Soyutma zonasında tipik temperaturlar 30–100 °C (86–212 °F) arasında dəyişir.Sürətli soyutma dərəcəsi mexaniki cəhətdən ən sağlam olan incə taxıl quruluşu yaratmaq üçün seçilir.
[1] Maksimum yüksəlmə sürətindən fərqli olaraq, eniş sürəti çox vaxt nəzərə alınmır.Müəyyən temperaturlardan yuxarı eniş sürəti daha az kritik ola bilər, lakin hər hansı komponent üçün maksimum icazə verilən yamac komponentin istiləşməsindən və ya soyumasından asılı olmayaraq tətbiq edilməlidir.Adətən 4°C/s soyutma sürəti təklif edilir.Prosesin nəticələrini təhlil edərkən nəzərə alınmalı olan bir parametrdir.
"Yenidən axan" termini, lehim ərintisinin bərk kütləsinin əriməyə əmin olduğu temperatura istinad etmək üçün istifadə olunur (sadəcə yumşaltmaqdan fərqli olaraq).Bu temperaturdan aşağı soyudulursa, lehim axmayacaq.Bir daha yuxarıda qızdırılan lehim yenidən axacaq - beləliklə "yenidən axın".
Yenidən lehimləmə istifadə edən müasir dövrə montaj üsulları lehimin bir dəfədən çox axmasına mütləq icazə vermir.Onlar lehim pastasının tərkibində olan dənəvər lehimin, lehimin təkrar axınının temperaturunu üstələdiyinə zəmanət verirlər.
Termal profilləşdirmə
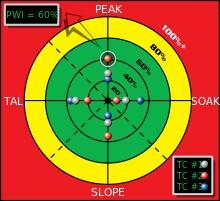
Termal profil üçün Proses Pəncərəsi İndeksinin qrafik təsviri.
Elektronika istehsalı sənayesində istilik prosesinin möhkəmliyini ölçmək üçün Proses Pəncərə İndeksi (PWI) kimi tanınan statistik ölçüdən istifadə olunur.PWI, prosesin Spesifikasiya Limiti kimi tanınan istifadəçi tərəfindən müəyyən edilmiş proses limitinə nə qədər "uyğun" olduğunu ölçməyə kömək edir. Hər bir istilik profili proses pəncərəsində (spesifikasiya və ya dözümlülük həddi) necə "uyduğuna" görə sıralanır.
Proses pəncərəsinin mərkəzi sıfır, proses pəncərəsinin ekstremal kənarı isə 99% kimi müəyyən edilir. 100%-dən böyük və ya ona bərabər olan PWI profilin spesifikasiya çərçivəsində məhsulu emal etmədiyini göstərir.99% PWI, profilin məhsulu spesifikasiya çərçivəsində emal etdiyini, lakin proses pəncərəsinin kənarında işlədiyini göstərir.60% PWI bir profilin proses spesifikasiyasının 60% istifadə etdiyini göstərir.PWI dəyərlərindən istifadə etməklə istehsalçılar müəyyən bir termal profilin nə qədər proses pəncərəsindən istifadə etdiyini müəyyən edə bilərlər.Aşağı PWI dəyəri daha möhkəm profili göstərir.
Maksimum səmərəlilik üçün istilik profilinin pik, yamac, reflow və islatma prosesləri üçün ayrı PWI dəyərləri hesablanır.İstilik şokunun çıxışa təsir etmə ehtimalının qarşısını almaq üçün istilik profilindəki ən dik yamac müəyyən edilməli və düzəldilməlidir.İstehsalçılar yamacın dikliyini dəqiq müəyyən etmək və azaltmaq üçün xüsusi hazırlanmış proqram təminatından istifadə edirlər.Bundan əlavə, proqram avtomatik olaraq pik, yamac, yenidən axın və islatma prosesləri üçün PWI dəyərlərini yenidən kalibrləyir.PWI dəyərlərini təyin etməklə, mühəndislər təkrar lehimləmə işinin həddindən artıq istiləşməməsini və ya çox tez soyumamasını təmin edə bilərlər.
Göndərmə vaxtı: 01 mart 2022-ci il