Запояването чрез повторно оформяне е процес, при който спояваща паста (лепкава смес от прахообразен припой и флюс) се използва за временно закрепване на един или няколко електрически компонента към техните контактни площадки, след което целият модул се подлага на контролирана топлина, която разтапя спойката , трайно свързващ ставата.Нагряването може да се осъществи чрез преминаване на модула през пещ за повторно оформяне или под инфрачервена лампа или чрез запояване на отделни съединения с молив с горещ въздух.
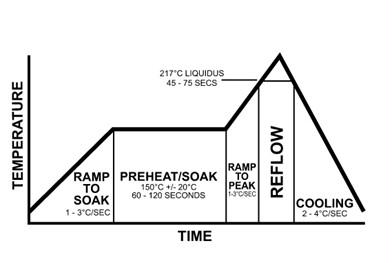
Запояването чрез повторно оформяне е най-разпространеният метод за закрепване на компоненти за повърхностен монтаж към печатна платка, въпреки че може да се използва и за компоненти с проходни отвори чрез запълване на отворите с паста за запояване и поставяне на проводниците на компонентите през пастата.Тъй като вълновото запояване може да бъде по-просто и по-евтино, повторното запояване обикновено не се използва върху платки с чисти отвори.Когато се използва върху платки, съдържащи комбинация от SMT и THT компоненти, преформатирането през отвор позволява стъпката на вълново запояване да бъде елиминирана от процеса на сглобяване, което потенциално намалява разходите за сглобяване.
Целта на процеса на преформатиране е да разтопи спойката и да загрее прилежащите повърхности, без прегряване и повреда на електрическите компоненти.В конвенционалния процес на запояване с препълване обикновено има четири етапа, наречени "зони", всяка от които има различен термичен профил: предварително загряване, термично накисване (често съкратено до просто накисване), повторно накисване и охлаждане.
Зона за предварително загряване
Максималният наклон е съотношението температура/време, което измерва колко бързо се променя температурата на печатната платка.Зоната за предварително загряване често е най-дългата от зоните и често определя скоростта на нарастване.Скоростта на нарастване обикновено е някъде между 1,0 °C и 3,0 °C за секунда, като често пада между 2,0 °C и 3,0 °C (4 °F до 5 °F) за секунда.Ако скоростта надвиши максималния наклон, може да възникне повреда на компонентите от термичен удар или напукване.
Пастата за запояване също може да има ефект на пръскане.Секцията за предварително нагряване е мястото, където разтворителят в пастата започва да се изпарява и ако скоростта на нарастване (или нивото на температурата) е твърде ниска, изпаряването на летливите вещества на потока е непълно.
Зона за термично накисване
Втората секция, термично накисване, обикновено е експозиция от 60 до 120 секунди за отстраняване на летливите вещества на пастата за запояване и активиране на флюсовете (вижте флюса), където компонентите на флюса започват окисление върху проводниците и подложките на компонентите.Твърде високата температура може да доведе до разпръскване или натрупване на спойка, както и до окисляване на пастата, подложките за закрепване и накрайниците на компонентите.
По същия начин, потоците може да не се активират напълно, ако температурата е твърде ниска.В края на зоната за накисване е желано термично равновесие на целия комплект точно преди зоната за претопяване.Препоръчва се профил на накисване, за да се намали всяка делта Т между компоненти с различни размери или ако монтажът на печатни платки е много голям.Препоръчва се също и профил на накисване, за да се намалят празнотите в пакети тип масив.
Reflow зона
Третият участък, зоната на пренареждане, се нарича още „време над пренареждане“ или „време над ликвидус“ (TAL) и е частта от процеса, където се достига максималната температура.Важно съображение е пиковата температура, която е максимално допустимата температура за целия процес.Общата пикова температура е 20–40 °C над ликвидус. Тази граница се определя от компонента на модула с най-нисък толеранс за високи температури (компонентът, който е най-податлив на термично увреждане).Стандартна насока е да се извадят 5 °C от максималната температура, която може да поддържа най-уязвимият компонент, за да се достигне максималната температура за процеса.Важно е да наблюдавате температурата на процеса, за да не надвишите тази граница.
Освен това високите температури (над 260 °C) могат да причинят повреда на вътрешните матрици на SMT компонентите, както и да насърчат растежа на интерметали.Обратно, температура, която не е достатъчно висока, може да попречи на пастата да се разтопи адекватно.
Време над ликвидус (TAL) или време над претопяване измерва колко дълго спойката е течност.Флюсът намалява повърхностното напрежение на кръстовището на металите, за да се постигне металургично свързване, което позволява на отделните сфери на прах за спойка да се комбинират.Ако времето на профила надвишава спецификацията на производителя, резултатът може да бъде преждевременно активиране или изразходване на потока, ефективно „изсушаване“ на пастата преди образуването на спойката.Недостатъчното съотношение време/температура води до намаляване на почистващото действие на флюса, което води до лошо намокряне, неадекватно отстраняване на разтворителя и флюса и евентуално дефектни споени съединения.
Експертите обикновено препоръчват възможно най-краткия TAL, но повечето пасти определят минимален TAL от 30 секунди, въпреки че изглежда няма ясна причина за това конкретно време.Една от възможностите е, че има места върху печатната платка, които не са измерени по време на профилиране, и следователно, определянето на минималното допустимо време на 30 секунди намалява шансовете неизмерената област да не се преформулира.Високото минимално време за претопяване също осигурява граница на безопасност срещу промени в температурата на пещта.Времето за намокряне в идеалния случай остава под 60 секунди над ликвидус.Допълнително време над ликвидус може да причини прекомерен интерметален растеж, което може да доведе до чупливост на ставите.Платката и компонентите също могат да се повредят при продължителни периоди от време над ликвидус и повечето компоненти имат точно дефинирано времево ограничение за това колко дълго могат да бъдат изложени на температури над даден максимум.
Твърде малкото време над ликвидус може да улови разтворители и флюс и да създаде потенциал за студени или тъпи съединения, както и кухини при запояване.
Охлаждаща зона
Последната зона е зона за охлаждане за постепенно охлаждане на обработената платка и втвърдяване на спойките.Правилното охлаждане предотвратява излишното образуване на интерметали или термичния шок на компонентите.Типичните температури в зоната на охлаждане варират от 30–100 °C (86–212 °F).Избира се бърза скорост на охлаждане, за да се създаде фина зърнеста структура, която е механично най-здрава.
[1] За разлика от максималната скорост на нарастване, скоростта на намаляване често се игнорира.Може да се окаже, че скоростта на нарастване е по-малко критична над определени температури, но максималният допустим наклон за всеки компонент трябва да се прилага независимо дали компонентът се нагрява или охлажда.Обикновено се препоръчва скорост на охлаждане от 4°C/s.Това е параметър, който трябва да се има предвид, когато се анализират резултатите от процеса.
Терминът "reflow" се използва за обозначаване на температурата, над която твърдата маса от спояваща сплав със сигурност ще се стопи (за разлика от простото размекване).Ако се охлади под тази температура, спойката няма да тече.Затоплен над него още веднъж, спойката ще тече отново - следователно "повторно тече".
Съвременните техники за сглобяване на вериги, които използват повторно запояване, не позволяват непременно спойката да тече повече от веднъж.Те гарантират, че гранулираната спойка, съдържаща се в спояващата паста, надвишава температурата на претопяване на използваната спойка.
Термично профилиране
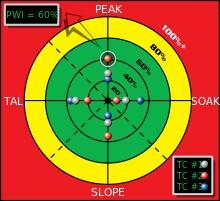
Графично представяне на индекса на прозореца на процеса за термичен профил.
В индустрията за производство на електроника статистическа мярка, известна като индекс на прозореца на процеса (PWI), се използва за количествено определяне на устойчивостта на термичен процес.PWI помага да се измери колко добре даден процес се „вписва“ в дефинирана от потребителя граница на процеса, известна като граница на спецификацията. Всеки термичен профил се класира според това как се „вписва“ в прозорец на процеса (спецификация или граница на толеранс).
Центърът на прозореца на процеса се определя като нула, а крайният ръб на прозореца на процеса е 99%. PWI, по-голям или равен на 100%, показва, че профилът не обработва продукта в рамките на спецификацията.PWI от 99% показва, че профилът обработва продукта в рамките на спецификацията, но работи в края на прозореца на процеса.PWI от 60% показва, че даден профил използва 60% от спецификацията на процеса.Чрез използване на PWI стойности, производителите могат да определят каква част от прозореца на процеса използва даден топлинен профил.По-ниска стойност на PWI показва по-стабилен профил.
За максимална ефективност се изчисляват отделни стойности на PWI за пик, наклон, процеси на преливане и накисване на термичен профил.За да се избегне възможността от термичен шок да повлияе на изхода, най-стръмният наклон в термичния профил трябва да бъде определен и изравнен.Производителите използват специално създаден софтуер за точно определяне и намаляване на стръмността на наклона.В допълнение, софтуерът също така автоматично калибрира отново стойностите на PWI за процесите на пик, наклон, препълване и накисване.Чрез задаване на стойности на PWI, инженерите могат да гарантират, че запояването с преплавяне няма да прегрее или охлади твърде бързо.
Време на публикуване: 01 март 2022 г