La soldadura per reflux és un procés en què s'utilitza una pasta de soldadura (una barreja enganxosa de soldadura en pols i flux) per connectar temporalment un o diversos components elèctrics als seus coixinets de contacte, després del qual tot el conjunt es sotmet a una calor controlada, que fon la soldadura. , connectant permanentment l'articulació.L'escalfament es pot aconseguir passant el conjunt a través d'un forn de reflux o sota una làmpada d'infrarojos o soldant juntes individuals amb un llapis d'aire calent.
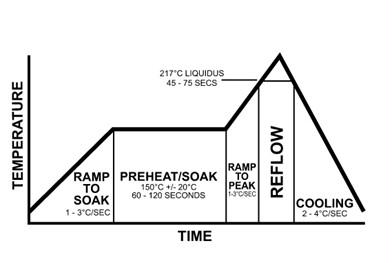
La soldadura per reflujo és el mètode més comú per connectar components de muntatge superficial a una placa de circuit, encara que també es pot utilitzar per a components de forat passant omplint els forats amb pasta de soldadura i inserint els cables dels components a través de la pasta.Com que la soldadura per ones pot ser més senzilla i econòmica, el reflux no s'utilitza generalment en taulers purs de forat.Quan s'utilitza en plaques que contenen una barreja de components SMT i THT, el reflujo de forats permet eliminar el pas de soldadura per ona del procés de muntatge, reduint potencialment els costos de muntatge.
L'objectiu del procés de reflux és fondre la soldadura i escalfar les superfícies adjacents, sense sobreescalfar i danyar els components elèctrics.En el procés de soldadura per reflux convencional, normalment hi ha quatre etapes, anomenades "zones", cadascuna amb un perfil tèrmic diferent: preescalfament, remull tèrmic (sovint escurçat a només remull), reflux i refredament.
Zona de preescalfament
El pendent màxim és una relació temperatura/temps que mesura la rapidesa amb què canvia la temperatura a la placa de circuit imprès.La zona de preescalfament és sovint la més llarga de les zones i sovint estableix la velocitat de rampa.La velocitat d'augment sol estar entre 1,0 °C i 3,0 °C per segon, sovint entre 2,0 °C i 3,0 °C (4 °F a 5 °F) per segon.Si la velocitat supera el pendent màxim, es poden produir danys als components per xoc tèrmic o esquerdes.
La pasta de soldadura també pot tenir un efecte esquitxat.La secció de preescalfament és on el dissolvent de la pasta comença a evaporar-se, i si la velocitat d'augment (o nivell de temperatura) és massa baixa, l'evaporació dels volàtils de flux és incompleta.
Zona de remull tèrmic
La segona secció, remull tèrmic, sol ser una exposició de 60 a 120 segons per a l'eliminació dels volàtils de la pasta de soldadura i l'activació dels fluxos (vegeu el flux), on els components del flux comencen a oxidar els cables i els coixinets dels components.Una temperatura massa alta pot provocar esquitxades o boles de soldadura, així com l'oxidació de la pasta, els coixinets de fixació i les terminacions dels components.
De la mateixa manera, és possible que els fluxos no s'activin completament si la temperatura és massa baixa.Al final de la zona de remull es desitja un equilibri tèrmic de tot el conjunt just abans de la zona de reflux.Es recomana un perfil de remull per reduir qualsevol delta T entre components de diferents mides o si el conjunt de PCB és molt gran.També es recomana un perfil de remull per disminuir el buit en paquets de tipus matriu d'àrea.
Zona de refluig
La tercera secció, la zona de reflux, també s'anomena "temps per sobre del reflux" o "temps per sobre del liquidus" (TAL), i és la part del procés on s'arriba a la temperatura màxima.Una consideració important és la temperatura màxima, que és la temperatura màxima permesa de tot el procés.Una temperatura màxima comuna és de 20 a 40 °C per sobre de liquidus. Aquest límit està determinat pel component del conjunt amb la tolerància més baixa per a altes temperatures (el component més susceptible a danys tèrmics).Una pauta estàndard és restar 5 °C de la temperatura màxima que pot suportar el component més vulnerable per arribar a la temperatura màxima per al procés.És important controlar la temperatura del procés per evitar que superi aquest límit.
A més, les altes temperatures (més enllà dels 260 °C) poden causar danys a les matrius internes dels components SMT i fomentar el creixement intermetàl·lic.Per contra, una temperatura que no sigui prou calenta pot impedir que la pasta refluixi adequadament.
El temps per sobre del liquidus (TAL), o el temps per sobre del reflux, mesura quant de temps la soldadura és líquida.El flux redueix la tensió superficial a la unió dels metalls per aconseguir la unió metal·lúrgica, permetent que les esferes de pols de soldadura individuals es combinen.Si el temps del perfil supera l'especificació del fabricant, el resultat pot ser l'activació o el consum prematur del flux, "assecant" efectivament la pasta abans de la formació de la junta de soldadura.Una relació de temps/temperatura insuficient provoca una disminució de l'acció de neteja del flux, donant lloc a una humectació deficient, una eliminació inadequada del dissolvent i del flux, i possiblement juntes de soldadura defectuoses.
Els experts solen recomanar el TAL més curt possible, però, la majoria de pastes especifiquen un TAL mínim de 30 segons, tot i que sembla que no hi ha una raó clara per a aquest temps específic.Una possibilitat és que hi hagi llocs a la PCB que no es mesuren durant el perfilat i, per tant, establir el temps mínim permès a 30 segons redueix les possibilitats que una àrea no mesurada no es torni a fluir.Un temps de refluig mínim elevat també proporciona un marge de seguretat contra els canvis de temperatura del forn.El temps d'humectació idealment es manté per sota dels 60 segons per sobre de liquidus.El temps addicional per sobre de liquidus pot provocar un creixement intermetàl·lic excessiu, que pot provocar fragilitat de les articulacions.El tauler i els components també es poden danyar en temps prolongats amb liquidus, i la majoria dels components tenen un límit de temps ben definit per quant de temps poden estar exposats a temperatures superiors a un màxim determinat.
Massa poc temps per sobre de liquidus pot atrapar dissolvents i flux i crear el potencial de juntes fredes o avorrides, així com buits de soldadura.
Zona de refrigeració
L'última zona és una zona de refrigeració per refredar gradualment el tauler processat i solidificar les juntes de soldadura.El refredament adequat inhibeix la formació intermetàl·lica excessiva o el xoc tèrmic als components.Les temperatures típiques a la zona de refrigeració oscil·len entre 30 i 100 °C (86 i 212 °F).S'escull una velocitat de refredament ràpida per crear una estructura de gra fi que sigui més sòlida mecànicament.
[1] A diferència de la velocitat de pujada màxima, sovint s'ignora la velocitat de baixada.Pot ser que la velocitat de rampa sigui menys crítica per sobre de determinades temperatures, però, s'hauria d'aplicar el pendent màxim permès per a qualsevol component tant si el component s'està escalfant com si es refreda.Normalment es recomana una velocitat de refredament de 4 °C/s.És un paràmetre a tenir en compte a l'hora d'analitzar els resultats del procés.
El terme "reflow" s'utilitza per referir-se a la temperatura per sobre de la qual una massa sòlida d'aliatge de soldadura segurament es fon (en lloc de simplement suavitzar).Si es refreda per sota d'aquesta temperatura, la soldadura no fluirà.Escalfada per sobre una vegada més, la soldadura tornarà a fluir, per tant, "refluirà".
Les tècniques modernes de muntatge de circuits que utilitzen la soldadura per reflux no permeten necessàriament que la soldadura flueixi més d'una vegada.Garantixen que la soldadura granulada continguda a la pasta de soldadura supera la temperatura de refluig de la soldadura implicada.
Perfil tèrmic
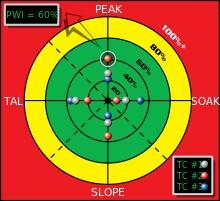
Una representació gràfica de l'índex de la finestra de procés per a un perfil tèrmic.
A la indústria de fabricació d'electrònica, s'utilitza una mesura estadística, coneguda com a Process Window Index (PWI) per quantificar la robustesa d'un procés tèrmic.PWI ajuda a mesurar fins a quin punt un procés "encaixa" en un límit de procés definit per l'usuari conegut com a límit d'especificació. Cada perfil tèrmic es classifica segons com "encaix" a una finestra de procés (l'especificació o el límit de tolerància).
El centre de la finestra del procés es defineix com a zero i la vora extrema de la finestra del procés com el 99%. Un PWI superior o igual al 100% indica que el perfil no processa el producte dins de les especificacions.Un PWI del 99% indica que el perfil processa el producte dins de les especificacions, però s'executa a la vora de la finestra del procés.Un PWI del 60% indica que un perfil utilitza el 60% de l'especificació del procés.Mitjançant l'ús de valors PWI, els fabricants poden determinar quina part de la finestra de procés utilitza un perfil tèrmic concret.Un valor PWI més baix indica un perfil més robust.
Per obtenir la màxima eficiència, es calculen valors PWI separats per als processos de pic, pendent, reflux i remull d'un perfil tèrmic.Per evitar la possibilitat de xoc tèrmic que afecti la sortida, s'ha de determinar i anivellar el pendent més pronunciat del perfil tèrmic.Els fabricants utilitzen un programari personalitzat per determinar i reduir amb precisió la inclinació del pendent.A més, el programari també recalibra automàticament els valors PWI per als processos de pic, pendent, reflux i remull.En establir els valors de PWI, els enginyers poden assegurar-se que el treball de soldadura per reflux no es sobreescalfi ni es refredi massa ràpidament.
Hora de publicació: 01-mar-2022