Beim Reflow-Löten handelt es sich um einen Prozess, bei dem eine Lotpaste (eine klebrige Mischung aus pulverförmigem Lot und Flussmittel) verwendet wird, um eine oder mehrere elektrische Komponenten vorübergehend an ihren Kontaktflächen zu befestigen. Anschließend wird die gesamte Baugruppe kontrollierter Hitze ausgesetzt, wodurch das Lot schmilzt , die Verbindung dauerhaft verbinden.Das Erhitzen kann erfolgen, indem die Baugruppe durch einen Reflow-Ofen oder unter einer Infrarotlampe geführt wird oder indem einzelne Verbindungen mit einem Heißluftstift gelötet werden.
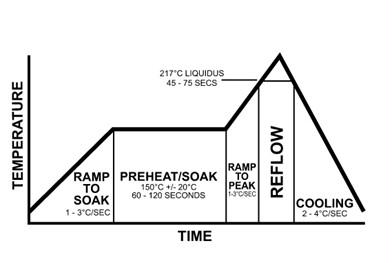
Reflow-Löten ist die gebräuchlichste Methode zum Befestigen von oberflächenmontierten Bauteilen auf einer Leiterplatte, kann jedoch auch für Durchgangslochbauteile verwendet werden, indem die Löcher mit Lötpaste gefüllt und die Bauteilleitungen durch die Paste eingeführt werden.Da Wellenlöten einfacher und kostengünstiger sein kann, wird Reflow bei reinen Durchsteckplatinen im Allgemeinen nicht verwendet.Beim Einsatz auf Platinen, die eine Mischung aus SMT- und THT-Komponenten enthalten, ermöglicht das Through-Hole-Reflow-Löten, dass der Schritt des Wellenlötens aus dem Montageprozess entfällt, was möglicherweise die Montagekosten senkt.
Das Ziel des Reflow-Prozesses besteht darin, das Lot zu schmelzen und die angrenzenden Oberflächen zu erhitzen, ohne die elektrischen Komponenten zu überhitzen und zu beschädigen.Beim herkömmlichen Reflow-Lötprozess gibt es normalerweise vier Stufen, sogenannte „Zonen“, die jeweils ein eigenes thermisches Profil haben: Vorheizen, thermisches Einweichen (häufig abgekürzt als „einfaches Einweichen“), Reflow und Abkühlen.
Zone vorheizen
Die maximale Steigung ist eine Temperatur-Zeit-Beziehung, die misst, wie schnell sich die Temperatur auf der Leiterplatte ändert.Die Vorheizzone ist häufig die längste der Zonen und legt häufig die Rampenrate fest.Die Anstiegsrate liegt normalerweise zwischen 1,0 °C und 3,0 °C pro Sekunde und liegt häufig zwischen 2,0 °C und 3,0 °C (4 °F bis 5 °F) pro Sekunde.Wenn die Rate die maximale Steigung überschreitet, kann es zu Schäden an Bauteilen durch Thermoschock oder Rissbildung kommen.
Auch Lotpaste kann eine spritzende Wirkung haben.Im Vorheizbereich beginnt das Lösungsmittel in der Paste zu verdampfen. Wenn die Anstiegsgeschwindigkeit (oder das Temperaturniveau) zu niedrig ist, ist die Verdunstung der flüchtigen Flussmittelbestandteile unvollständig.
Thermal-Soak-Zone
Der zweite Abschnitt, das thermische Einweichen, besteht typischerweise aus einer 60 bis 120 Sekunden dauernden Einwirkung zur Entfernung flüchtiger Bestandteile der Lotpaste und zur Aktivierung der Flussmittel (siehe Flussmittel), wobei die Flussmittelkomponenten mit der Oxidreduktion auf den Anschlüssen und Pads der Komponenten beginnen.Eine zu hohe Temperatur kann zu Lötspritzern oder -klumpen sowie zur Oxidation der Paste, der Anschlusspads und der Bauteilanschlüsse führen.
Ebenso kann es sein, dass Flussmittel nicht vollständig aktiviert werden, wenn die Temperatur zu niedrig ist.Am Ende der Soak-Zone ist ein thermisches Gleichgewicht der gesamten Baugruppe unmittelbar vor der Reflow-Zone erwünscht.Ein Einweichprofil wird empfohlen, um das Delta T zwischen Bauteilen unterschiedlicher Größe oder bei sehr großen Leiterplattenbaugruppen zu verringern.Ein Einweichprofil wird außerdem empfohlen, um die Bildung von Hohlräumen in Flächenpaketen zu verringern.
Reflow-Zone
Der dritte Abschnitt, die Reflow-Zone, wird auch als „Time Above Reflow“ oder „Time Above Liquidus“ (TAL) bezeichnet und ist der Teil des Prozesses, in dem die maximale Temperatur erreicht wird.Ein wichtiger Gesichtspunkt ist die Spitzentemperatur, also die maximal zulässige Temperatur des gesamten Prozesses.Eine häufige Spitzentemperatur liegt bei 20–40 °C über Liquidus. Dieser Grenzwert wird durch die Komponente der Baugruppe mit der geringsten Toleranz gegenüber hohen Temperaturen bestimmt (die Komponente, die am anfälligsten für thermische Schäden ist).Eine Standardrichtlinie besteht darin, 5 °C von der maximalen Temperatur abzuziehen, die die anfälligste Komponente aushalten kann, um die maximale Temperatur für den Prozess zu erreichen.Es ist wichtig, die Prozesstemperatur zu überwachen, um zu verhindern, dass sie diesen Grenzwert überschreitet.
Darüber hinaus können hohe Temperaturen (über 260 °C) Schäden an den internen Chips von SMT-Komponenten verursachen und intermetallisches Wachstum fördern.Umgekehrt kann eine zu niedrige Temperatur dazu führen, dass die Paste nicht ausreichend auffließt.
Die Zeit oberhalb des Liquidus (TAL) oder die Zeit oberhalb des Reflows misst, wie lange das Lot flüssig ist.Das Flussmittel reduziert die Oberflächenspannung an der Verbindungsstelle der Metalle, um eine metallurgische Verbindung zu erreichen und die Verbindung der einzelnen Lotpulverkügelchen zu ermöglichen.Wenn die Profilzeit die Angaben des Herstellers überschreitet, kann es zu einer vorzeitigen Aktivierung oder einem vorzeitigen Verbrauch des Flussmittels kommen, wodurch die Paste effektiv „austrocknet“, bevor sich die Lötverbindung bildet.Ein unzureichendes Zeit-/Temperaturverhältnis führt zu einer verminderten Reinigungswirkung des Flussmittels, was zu einer schlechten Benetzung, einer unzureichenden Entfernung des Lösungsmittels und Flussmittels und möglicherweise zu fehlerhaften Lötstellen führt.
Experten empfehlen normalerweise die kürzestmögliche TAL, die meisten Pasten geben jedoch eine minimale TAL von 30 Sekunden an, obwohl es offenbar keinen klaren Grund für diese bestimmte Zeit gibt.Eine Möglichkeit besteht darin, dass es Stellen auf der Leiterplatte gibt, die während der Profilierung nicht gemessen werden. Daher verringert die Einstellung der minimal zulässigen Zeit auf 30 Sekunden die Wahrscheinlichkeit, dass ein nicht gemessener Bereich nicht zurückfließt.Eine hohe Mindest-Reflow-Zeit bietet auch einen Sicherheitsspielraum gegen Ofentemperaturschwankungen.Die Benetzungszeit bleibt idealerweise unter 60 Sekunden über Liquidus.Eine zusätzliche Zeit oberhalb des Liquidus kann zu übermäßigem intermetallischem Wachstum führen, was zu einer Brüchigkeit der Verbindung führen kann.Die Platine und die Komponenten können auch über einen längeren Zeitraum durch Liquidus beschädigt werden, und die meisten Komponenten haben eine genau definierte Zeitbegrenzung, wie lange sie Temperaturen über einem bestimmten Maximum ausgesetzt werden dürfen.
Zu wenig Zeit über Liquidus kann Lösungsmittel und Flussmittel einschließen und die Gefahr kalter oder stumpfer Verbindungen sowie von Lötlöchern schaffen.
Kühlzone
Die letzte Zone ist eine Kühlzone, um die bearbeitete Platine allmählich abzukühlen und die Lötstellen zu verfestigen.Eine ordnungsgemäße Kühlung verhindert eine übermäßige intermetallische Bildung oder einen Thermoschock an den Komponenten.Typische Temperaturen in der Kühlzone liegen zwischen 30 und 100 °C (86 und 212 °F).Um eine feine Kornstruktur zu erzeugen, die mechanisch am stabilsten ist, wird eine schnelle Abkühlrate gewählt.
[1] Im Gegensatz zur maximalen Hochlaufrate wird die Rücklaufrate häufig ignoriert.Es kann sein, dass die Anstiegsrate oberhalb bestimmter Temperaturen weniger kritisch ist, jedoch sollte die maximal zulässige Steigung für jede Komponente gelten, unabhängig davon, ob die Komponente aufheizt oder abkühlt.Im Allgemeinen wird eine Abkühlrate von 4 °C/s empfohlen.Es handelt sich um einen Parameter, der bei der Analyse von Prozessergebnissen berücksichtigt werden muss.
Der Begriff „Reflow“ bezieht sich auf die Temperatur, oberhalb derer eine feste Masse einer Lotlegierung mit Sicherheit schmilzt (im Gegensatz zum bloßen Erweichen).Bei Abkühlung unter diese Temperatur fließt das Lot nicht.Wenn das Lot noch einmal darüber erwärmt wird, fließt es wieder – daher „Reflow“.
Moderne Schaltkreismontagetechniken, die Reflow-Löten verwenden, ermöglichen nicht unbedingt, dass das Lot mehr als einmal fließt.Sie gewährleisten, dass das in der Lotpaste enthaltene Lotgranulat die Reflow-Temperatur des jeweiligen Lotes überschreitet.
Thermische Profilierung
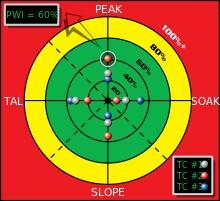
Eine grafische Darstellung des Prozessfensterindex für ein thermisches Profil.
In der Elektronikfertigungsindustrie wird ein statistisches Maß, der Process Window Index (PWI), verwendet, um die Robustheit eines thermischen Prozesses zu quantifizieren.PWI hilft zu messen, wie gut ein Prozess in eine benutzerdefinierte Prozessgrenze, die sogenannte Spezifikationsgrenze, „passt“. Jedes thermische Profil wird danach eingestuft, wie es in ein Prozessfenster „passt“ (die Spezifikation oder Toleranzgrenze).
Die Mitte des Prozessfensters ist als Null und der äußerste Rand des Prozessfensters als 99 % definiert. Ein PWI größer oder gleich 100 % zeigt an, dass das Profil das Produkt nicht innerhalb der Spezifikation verarbeitet.Ein PWI von 99 % bedeutet, dass das Profil das Produkt innerhalb der Spezifikation verarbeitet, aber am Rand des Prozessfensters läuft.Ein PWI von 60 % bedeutet, dass ein Profil 60 % der Prozessspezifikation verwendet.Durch die Verwendung von PWI-Werten können Hersteller bestimmen, wie viel des Prozessfensters ein bestimmtes thermisches Profil nutzt.Ein niedrigerer PWI-Wert weist auf ein robusteres Profil hin.
Für maximale Effizienz werden separate PWI-Werte für Peak-, Slope-, Reflow- und Soak-Prozesse eines thermischen Profils berechnet.Um die Möglichkeit zu vermeiden, dass ein Thermoschock die Leistung beeinträchtigt, muss die steilste Steigung im thermischen Profil bestimmt und eingeebnet werden.Hersteller verwenden speziell entwickelte Software, um die Steilheit des Hangs genau zu bestimmen und zu verringern.Darüber hinaus kalibriert die Software auch automatisch die PWI-Werte für die Peak-, Slope-, Reflow- und Soak-Prozesse neu.Durch die Festlegung von PWI-Werten können Ingenieure sicherstellen, dass die Reflow-Lötarbeit nicht überhitzt oder zu schnell abkühlt.
Zeitpunkt der Veröffentlichung: 01.03.2022