La soldadura por reflujo es un proceso en el que se utiliza una pasta de soldadura (una mezcla pegajosa de soldadura en polvo y fundente) para unir temporalmente uno o varios componentes eléctricos a sus almohadillas de contacto, después de lo cual todo el conjunto se somete a calor controlado, que derrite la soldadura. , conectando permanentemente la junta.El calentamiento se puede lograr pasando el conjunto a través de un horno de reflujo o bajo una lámpara de infrarrojos o soldando juntas individuales con un lápiz de aire caliente.
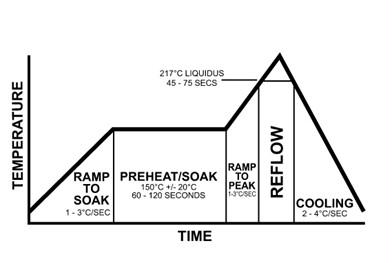
La soldadura por reflujo es el método más común para unir componentes de montaje superficial a una placa de circuito, aunque también se puede usar para componentes con orificios pasantes llenando los orificios con pasta de soldadura e insertando los cables del componente a través de la pasta.Debido a que la soldadura por ola puede ser más simple y económica, el reflujo generalmente no se usa en placas con orificios pasantes puros.Cuando se utiliza en placas que contienen una mezcla de componentes SMT y THT, el reflujo de orificio pasante permite eliminar el paso de soldadura por ola del proceso de ensamblaje, lo que potencialmente reduce los costos de ensamblaje.
El objetivo del proceso de reflujo es derretir la soldadura y calentar las superficies adyacentes, sin sobrecalentar ni dañar los componentes eléctricos.En el proceso de soldadura por reflujo convencional, generalmente hay cuatro etapas, llamadas "zonas", cada una con un perfil térmico distinto: precalentamiento, remojo térmico (a menudo abreviado como solo remojo), reflujo y enfriamiento.
Zona de precalentamiento
La pendiente máxima es una relación temperatura/tiempo que mide qué tan rápido cambia la temperatura en la placa de circuito impreso.La zona de precalentamiento suele ser la más larga de las zonas y suele establecer la velocidad de rampa.La tasa de aumento suele estar entre 1,0 °C y 3,0 °C por segundo, y a menudo cae entre 2,0 °C y 3,0 °C (4 °F a 5 °F) por segundo.Si la tasa excede la pendiente máxima, se pueden producir daños a los componentes por choque térmico o grietas.
La pasta de soldar también puede tener un efecto de salpicaduras.La sección de precalentamiento es donde el disolvente de la pasta comienza a evaporarse y, si la tasa de aumento (o nivel de temperatura) es demasiado baja, la evaporación de los volátiles del fundente es incompleta.
Zona de inmersión térmica
La segunda sección, inmersión térmica, suele ser una exposición de 60 a 120 segundos para eliminar los volátiles de la pasta de soldadura y activar los fundentes (ver fundente), donde los componentes del fundente comienzan la reducción de óxido en los terminales y almohadillas de los componentes.Una temperatura demasiado alta puede provocar salpicaduras o bolas de soldadura, así como oxidación de la pasta, las almohadillas de fijación y las terminaciones de los componentes.
De manera similar, es posible que los fundentes no se activen completamente si la temperatura es demasiado baja.Al final de la zona de inmersión se desea un equilibrio térmico de todo el conjunto justo antes de la zona de reflujo.Se sugiere un perfil de inmersión para disminuir cualquier delta T entre componentes de diferentes tamaños o si el conjunto de PCB es muy grande.También se recomienda un perfil de inmersión para disminuir la formación de huecos en paquetes tipo matriz de área.
Zona de reflujo
La tercera sección, la zona de reflujo, también se conoce como “tiempo por encima del reflujo” o “tiempo por encima del liquidus” (TAL), y es la parte del proceso donde se alcanza la temperatura máxima.Una consideración importante es la temperatura máxima, que es la temperatura máxima permitida de todo el proceso.Una temperatura máxima común es de 20 a 40 °C por encima del líquido. Este límite lo determina el componente del conjunto con la tolerancia más baja a las altas temperaturas (el componente más susceptible al daño térmico).Una pauta estándar es restar 5 °C de la temperatura máxima que el componente más vulnerable puede soportar para llegar a la temperatura máxima para el proceso.Es importante monitorear la temperatura del proceso para evitar que exceda este límite.
Además, las altas temperaturas (más de 260 °C) pueden causar daños a las matrices internas de los componentes SMT y fomentar el crecimiento intermetálico.Por el contrario, una temperatura que no sea lo suficientemente alta puede impedir que la pasta fluya adecuadamente.
El tiempo por encima del liquidus (TAL), o tiempo por encima del reflujo, mide cuánto tiempo la soldadura es líquida.El fundente reduce la tensión superficial en la unión de los metales para lograr la unión metalúrgica, permitiendo que las esferas individuales de polvo de soldadura se combinen.Si el tiempo del perfil excede las especificaciones del fabricante, el resultado puede ser una activación o consumo prematuro del fundente, “secando” efectivamente la pasta antes de la formación de la unión de soldadura.Una relación tiempo/temperatura insuficiente provoca una disminución en la acción limpiadora del fundente, lo que resulta en una mala humectación, una eliminación inadecuada del solvente y el fundente y posiblemente uniones de soldadura defectuosas.
Los expertos suelen recomendar el TAL más corto posible; sin embargo, la mayoría de las pastas especifican un TAL mínimo de 30 segundos, aunque no parece haber una razón clara para ese tiempo específico.Una posibilidad es que haya lugares en la PCB que no se midan durante el perfilado y, por lo tanto, establecer el tiempo mínimo permitido en 30 segundos reduce las posibilidades de que un área no medida no refluya.Un tiempo de reflujo mínimo elevado también proporciona un margen de seguridad contra los cambios de temperatura del horno.Lo ideal es que el tiempo de humectación se mantenga por debajo de 60 segundos por encima del líquido.Un tiempo adicional por encima del líquido puede provocar un crecimiento intermetálico excesivo, lo que puede provocar fragilidad en las articulaciones.La placa y los componentes también pueden dañarse durante períodos prolongados debido al líquido, y la mayoría de los componentes tienen un límite de tiempo bien definido sobre cuánto tiempo pueden estar expuestos a temperaturas superiores a un máximo determinado.
Muy poco tiempo por encima del líquido puede atrapar disolventes y fundentes y crear la posibilidad de que se produzcan uniones frías o opacas, así como huecos de soldadura.
Zona de enfriamiento
La última zona es una zona de enfriamiento para enfriar gradualmente la placa procesada y solidificar las uniones de soldadura.Un enfriamiento adecuado inhibe el exceso de formación intermetálica o el choque térmico en los componentes.Las temperaturas típicas en la zona de enfriamiento oscilan entre 30 y 100 °C (86 y 212 °F).Se elige una velocidad de enfriamiento rápida para crear una estructura de grano fino que sea mecánicamente más sólida.
[1] A diferencia de la tasa máxima de aceleración, la tasa de desaceleración a menudo se ignora.Puede ser que la velocidad de rampa sea menos crítica por encima de ciertas temperaturas; sin embargo, la pendiente máxima permitida para cualquier componente debe aplicarse ya sea que el componente se esté calentando o enfriando.Comúnmente se sugiere una velocidad de enfriamiento de 4°C/s.Es un parámetro a considerar al analizar los resultados del proceso.
El término "reflujo" se utiliza para referirse a la temperatura por encima de la cual una masa sólida de aleación de soldadura seguramente se derretirá (en lugar de simplemente ablandarse).Si se enfría por debajo de esta temperatura, la soldadura no fluirá.Si se calienta por encima una vez más, la soldadura fluirá nuevamente, por lo tanto "refluirá".
Las técnicas modernas de ensamblaje de circuitos que utilizan soldadura por reflujo no necesariamente permiten que la soldadura fluya más de una vez.Garantizan que la soldadura granulada contenida en la soldadura en pasta supera la temperatura de reflujo de la soldadura involucrada.
Perfilado térmico
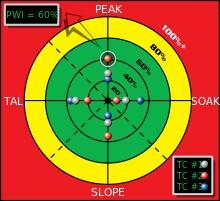
Una representación gráfica del índice de ventana de proceso para un perfil térmico.
En la industria de fabricación de productos electrónicos, se utiliza una medida estadística, conocida como Índice de ventana de proceso (PWI), para cuantificar la robustez de un proceso térmico.PWI ayuda a medir qué tan bien "encaja" un proceso en un límite de proceso definido por el usuario conocido como límite de especificación. Cada perfil térmico se clasifica según cómo "encaja" en una ventana de proceso (la especificación o límite de tolerancia).
El centro de la ventana de proceso se define como cero y el borde extremo de la ventana de proceso como 99%. Un PWI mayor o igual a 100% indica que el perfil no procesa el producto dentro de las especificaciones.Un PWI del 99 % indica que el perfil procesa el producto dentro de las especificaciones, pero se ejecuta en el borde de la ventana de proceso.Un PWI del 60 % indica que un perfil utiliza el 60 % de la especificación del proceso.Al utilizar los valores de PWI, los fabricantes pueden determinar qué parte de la ventana del proceso utiliza un perfil térmico en particular.Un valor de PWI más bajo indica un perfil más sólido.
Para lograr la máxima eficiencia, se calculan valores PWI separados para los procesos de pico, pendiente, reflujo y absorción de un perfil térmico.Para evitar la posibilidad de que un choque térmico afecte la salida, se debe determinar y nivelar la pendiente más pronunciada en el perfil térmico.Los fabricantes utilizan software personalizado para determinar y disminuir con precisión la pendiente de la pendiente.Además, el software también recalibra automáticamente los valores de PWI para los procesos de pico, pendiente, reflujo y remojo.Al establecer los valores de PWI, los ingenieros pueden garantizar que el trabajo de soldadura por reflujo no se sobrecaliente ni se enfríe demasiado rápido.
Hora de publicación: 01-mar-2022