لحیم کاری مجدد فرآیندی است که در آن از خمیر لحیم کاری (مخلوطی چسبنده از لحیم پودری و فلاکس) برای اتصال موقت یک یا چند جزء الکتریکی به لنت های تماس آنها استفاده می شود و پس از آن کل مجموعه تحت حرارت کنترل شده قرار می گیرد که لحیم کاری را ذوب می کند. ، اتصال دائمی مفصل.گرمایش ممکن است با عبور دادن مجموعه از یک کوره جریان یا زیر یک لامپ مادون قرمز یا با لحیم کردن اتصالات جداگانه با یک مداد هوای گرم انجام شود.
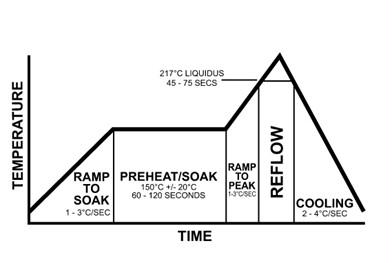
لحیم کاری مجدد رایج ترین روش برای اتصال قطعات نصب سطحی به برد مدار است، اگرچه می توان از آن برای قطعات سوراخ شده نیز با پر کردن سوراخ ها با خمیر لحیم کاری و قرار دادن سرنخ های قطعه از طریق خمیر استفاده کرد.از آنجایی که لحیم کاری موج می تواند ساده تر و ارزان تر باشد، جریان مجدد معمولاً روی تخته های سوراخ دار خالص استفاده نمی شود.هنگامی که بر روی بردهایی که حاوی ترکیبی از اجزای SMT و THT هستند استفاده می شود، جریان مجدد از طریق سوراخ اجازه می دهد تا مرحله لحیم کاری موج از فرآیند مونتاژ حذف شود و به طور بالقوه هزینه های مونتاژ را کاهش دهد.
هدف از فرآیند جریان مجدد ذوب کردن لحیم کاری و گرم کردن سطوح مجاور بدون گرم شدن بیش از حد و آسیب رساندن به اجزای الکتریکی است.در فرآیند لحیم کاری با جریان معمولی، معمولاً چهار مرحله وجود دارد که «منطقهها» نامیده میشوند، که هر کدام مشخصات حرارتی مشخصی دارند: پیشگرم، خیساندن حرارتی (اغلب کوتاهتر میشود)، جریان مجدد و خنکسازی.
منطقه پیش گرم
حداکثر شیب یک رابطه دما/زمان است که سرعت تغییر دما در برد مدار چاپی را اندازه میگیرد.منطقه پیش گرم اغلب طولانی ترین منطقه است و اغلب نرخ شیب دار را تعیین می کند.نرخ شیب بالا معمولاً بین 1.0 تا 3.0 درجه سانتیگراد در ثانیه است که اغلب بین 2.0 تا 3.0 درجه سانتیگراد (4 درجه فارنهایت تا 5 درجه فارنهایت) در ثانیه کاهش می یابد.اگر سرعت از حداکثر شیب تجاوز کند، آسیب به قطعات ناشی از شوک حرارتی یا ترک خوردگی ممکن است رخ دهد.
خمیر لحیم کاری نیز می تواند اثر پاشیدن داشته باشد.بخش پیش گرما جایی است که حلال در خمیر شروع به تبخیر می کند و اگر میزان افزایش (یا سطح دما) خیلی کم باشد، تبخیر مواد فرار شار ناقص است.
منطقه خیساندن حرارتی
بخش دوم، خیساندن حرارتی، معمولا یک نوردهی 60 تا 120 ثانیه ای برای حذف مواد فرار خمیر لحیم کاری و فعال شدن شارها است (به شار مراجعه کنید)، جایی که اجزای شار شروع به کاهش اکسیداسیون روی لیدها و لنت های اجزا می کنند.دمای بیش از حد بالا می تواند منجر به پاشیدگی لحیم کاری یا گلوله شدن و همچنین اکسید شدن خمیر، لنت های اتصال و پایان قطعات شود.
به طور مشابه، اگر دما خیلی پایین باشد، شارها ممکن است به طور کامل فعال نشوند.در انتهای منطقه خیساندن، تعادل حرارتی کل مجموعه درست قبل از منطقه جریان مجدد مورد نظر است.برای کاهش دلتا T بین اجزای با اندازه های مختلف یا اگر مجموعه PCB بسیار بزرگ باشد، یک پروفایل خیس کردن پیشنهاد می شود.همچنین برای کاهش تخلیه در بستههای نوع آرایه منطقهای، یک پروفایل خیسکردن توصیه میشود.
منطقه جریان مجدد
بخش سوم، منطقه جریان مجدد، همچنین به عنوان "زمان بالای جریان مجدد" یا "زمان بالای مایع" (TAL) شناخته می شود و بخشی از فرآیند است که در آن به حداکثر دما می رسد.یک نکته مهم دمای پیک است که حداکثر دمای مجاز کل فرآیند است.حداکثر دمای معمول 20 تا 40 درجه سانتیگراد بالاتر از مایع است. این حد توسط قطعه روی مجموعه با کمترین تحمل برای دماهای بالا (جزئی که مستعد آسیب حرارتی است) تعیین می شود.یک دستورالعمل استاندارد این است که 5 درجه سانتیگراد از حداکثر دمایی که آسیب پذیرترین جزء می تواند برای رسیدن به حداکثر دمای فرآیند حفظ کند، کم شود.نظارت بر دمای فرآیند برای جلوگیری از تجاوز از این حد بسیار مهم است.
علاوه بر این، دمای بالا (بیش از 260 درجه سانتیگراد) ممکن است باعث آسیب به قالبهای داخلی اجزای SMT و همچنین رشد بین فلزی شود.برعکس، دمایی که به اندازه کافی گرم نباشد ممکن است از جریان مجدد خمیر به اندازه کافی جلوگیری کند.
زمان بالای مایع (TAL)، یا زمان بالای جریان مجدد، مدت زمانی که لحیم کاری مایع است را اندازه گیری می کند.شار کشش سطحی را در محل اتصال فلزات کاهش می دهد تا پیوند متالورژیکی را انجام دهد و به کره های پودر لحیم کاری اجازه می دهد تا با هم ترکیب شوند.اگر زمان پروفیل بیشتر از مشخصات سازنده باشد، نتیجه ممکن است فعال یا مصرف زودرس شار باشد که به طور موثر خمیر را قبل از تشکیل اتصال لحیم "خشک می کند".یک رابطه زمان/دمای ناکافی باعث کاهش عملکرد تمیز کردن شار می شود که در نتیجه خیس شدن ضعیف، حذف ناکافی حلال و شار و احتمالاً اتصالات لحیم کاری معیوب می شود.
کارشناسان معمولا کوتاه ترین TAL ممکن را توصیه می کنند، با این حال، اکثر خمیرها حداقل TAL 30 ثانیه را مشخص می کنند، اگرچه به نظر می رسد دلیل روشنی برای آن زمان خاص وجود ندارد.یکی از احتمالات این است که مکان هایی روی PCB وجود دارد که در حین پروفایل اندازه گیری نمی شوند و بنابراین، تنظیم حداقل زمان مجاز روی 30 ثانیه، احتمال عدم جریان مجدد یک ناحیه اندازه گیری نشده را کاهش می دهد.حداقل زمان جریان مجدد بالا نیز حاشیه ایمنی در برابر تغییرات دمای فر را فراهم می کند.زمان خیس شدن در حالت ایده آل زیر 60 ثانیه بالای مایع باقی می ماند.زمان اضافی بالای مایع ممکن است باعث رشد بیش از حد بین فلزی شود که می تواند منجر به شکنندگی مفصل شود.برد و اجزای آن همچنین ممکن است در زمان های طولانی بیش از مایعات آسیب ببینند، و اکثر اجزا دارای محدودیت زمانی مشخصی برای مدت زمانی هستند که ممکن است در معرض دمای بیش از یک حداکثر معین قرار گیرند.
زمان بسیار کم بالای مایع ممکن است حلال ها و شار را به دام بیاندازد و پتانسیل ایجاد اتصالات سرد یا کسل کننده و همچنین حفره های لحیم کاری را ایجاد کند.
منطقه خنک کننده
آخرین منطقه یک منطقه خنک کننده برای خنک کردن تدریجی برد پردازش شده و جامد کردن اتصالات لحیم کاری است.خنک کاری مناسب از تشکیل بیش از حد بین فلزی یا شوک حرارتی به اجزاء جلوگیری می کند.دمای معمولی در منطقه خنک کننده از 30 تا 100 درجه سانتیگراد (86 تا 212 درجه فارنهایت) متغیر است.یک سرعت خنک کننده سریع برای ایجاد ساختار دانه ریز انتخاب شده است که از نظر مکانیکی بسیار سالم است.
[1] برخلاف حداکثر نرخ افزایش، نرخ شیب پایین اغلب نادیده گرفته میشود.ممکن است نرخ رمپ بالاتر از دماهای خاص کمتر بحرانی باشد، با این حال، حداکثر شیب مجاز برای هر جزء باید اعمال شود، چه قطعه در حال گرم شدن یا خنک شدن باشد.معمولاً سرعت سرمایش 4 درجه سانتیگراد در ثانیه پیشنهاد می شود.این پارامتری است که هنگام تجزیه و تحلیل نتایج فرآیند باید در نظر گرفته شود.
اصطلاح "جریان مجدد" برای اشاره به دمایی استفاده می شود که بالاتر از آن یک توده جامد از آلیاژ لحیم کاری ذوب می شود (در مقابل صرفاً نرم شدن).اگر زیر این دما خنک شود، لحیم کاری جریان پیدا نمی کند.لحیم کاری که یک بار دیگر در بالای آن گرم می شود، دوباره جریان می یابد - بنابراین "جریان مجدد".
تکنیک های مونتاژ مدار مدرن که از لحیم کاری مجدد استفاده می کنند لزوماً اجازه نمی دهند که لحیم کاری بیش از یک بار جریان یابد.آنها تضمین می کنند که لحیم گرانول موجود در خمیر لحیم از دمای جریان مجدد لحیم کاری درگیر فراتر می رود.
پروفیل حرارتی
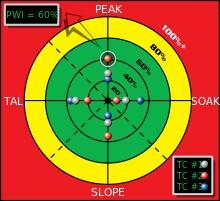
یک نمایش گرافیکی از شاخص پنجره فرآیند برای یک پروفایل حرارتی.
در صنعت تولید الکترونیک، یک معیار آماری، به نام شاخص پنجره فرآیند (PWI) شناخته میشود تا استحکام یک فرآیند حرارتی را تعیین کند.PWI به اندازهگیری میزان «تطابق» یک فرآیند با یک محدودیت فرآیند تعریفشده توسط کاربر، معروف به «محدودیت مشخصات» کمک میکند.
مرکز پنجره فرآیند به عنوان صفر و لبه انتهایی پنجره فرآیند به عنوان 99٪ تعریف می شود. یک PWI بزرگتر یا مساوی 100٪ نشان می دهد که نمایه محصول را مطابق مشخصات پردازش نمی کند.PWI 99% نشان می دهد که نمایه محصول را مطابق مشخصات پردازش می کند، اما در لبه پنجره فرآیند اجرا می شود.PWI 60٪ نشان می دهد که یک پروفایل از 60٪ مشخصات فرآیند استفاده می کند.با استفاده از مقادیر PWI، سازندگان می توانند تعیین کنند که یک پروفیل حرارتی خاص از چه مقدار از پنجره فرآیند استفاده می کند.مقدار PWI پایین تر نشان دهنده پروفایل قوی تر است.
برای حداکثر کارایی، مقادیر PWI جداگانه برای فرآیندهای پیک، شیب، جریان مجدد و خیساندن یک پروفیل حرارتی محاسبه میشود.برای جلوگیری از احتمال تاثیر شوک حرارتی بر خروجی، باید تندترین شیب در پروفیل حرارتی تعیین و تراز شود.سازندگان از نرم افزارهای سفارشی ساخته شده برای تعیین دقیق و کاهش شیب شیب استفاده می کنند.علاوه بر این، نرم افزار همچنین به طور خودکار مقادیر PWI را برای فرآیندهای اوج، شیب، جریان مجدد و خیس کردن مجدد کالیبره می کند.با تنظیم مقادیر PWI، مهندسان می توانند اطمینان حاصل کنند که کار لحیم کاری با جریان مجدد بیش از حد گرم نمی شود یا خیلی سریع سرد نمی شود.
زمان ارسال: مارس-01-2022