A soldadura por refluxo é un proceso no que se usa unha pasta de soldadura (unha mestura pegajosa de soldadura en po e fundente) para unir temporalmente un ou varios compoñentes eléctricos ás súas almofadas de contacto, despois do cal todo o conxunto é sometido a calor controlado, que derrete a soldadura. , conectando permanentemente a articulación.O quecemento pódese conseguir pasando o conxunto a través dun forno de refluxo ou baixo unha lámpada infravermella ou soldando xuntas individuais cun lapis de aire quente.
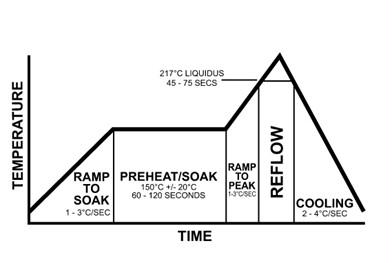
A soldadura por refluxo é o método máis común de unir compoñentes de montaxe en superficie a unha placa de circuíto, aínda que tamén se pode usar para compoñentes de orificios pasantes enchendo os buratos con pasta de soldadura e introducindo os cables de compoñentes a través da pasta.Debido a que a soldadura por onda pode ser máis sinxela e barata, o refluxo xeralmente non se usa en placas de orificios pasantes puros.Cando se usa en placas que conteñen unha mestura de compoñentes SMT e THT, o refluxo de orificios pasantes permite que o paso de soldadura por onda se elimine do proceso de montaxe, reducindo potencialmente os custos de montaxe.
O obxectivo do proceso de refluxo é derreter a soldadura e quentar as superficies adxacentes, sen quentar e danar os compoñentes eléctricos.No proceso de soldadura por refluxo convencional, normalmente hai catro etapas, chamadas "zonas", cada unha con un perfil térmico distinto: prequecemento, remollo térmico (moitas veces acurtado a só remollo), refluxo e arrefriamento.
Zona de prequentar
A pendente máxima é unha relación temperatura/tempo que mide a rapidez con que cambia a temperatura na placa de circuíto impreso.A zona de prequentamento adoita ser a máis longa das zonas e moitas veces establece a taxa de rampla.A velocidade de aceleración adoita estar nalgún lugar entre 1,0 °C e 3,0 °C por segundo, a miúdo cae entre 2,0 °C e 3,0 °C (4 °F a 5 °F) por segundo.Se a taxa supera a pendente máxima, pódense producir danos nos compoñentes por choque térmico ou rachaduras.
A pasta de soldar tamén pode ter un efecto de salpicadura.A sección de precalentamento é onde o disolvente da pasta comeza a evaporarse e, se a taxa de aumento (ou nivel de temperatura) é demasiado baixa, a evaporación dos volátiles do fluxo é incompleta.
Zona de inmersión térmica
A segunda sección, a inmersión térmica, é normalmente unha exposición de 60 a 120 segundos para a eliminación de volátiles da pasta de soldadura e a activación dos fluxos (ver fluxo), onde os compoñentes do fluxo comezan a oxidar os cables e as almofadas dos compoñentes.Unha temperatura demasiado alta pode provocar salpicaduras ou bolas de soldadura, así como a oxidación da pasta, as almofadas de unión e as terminacións dos compoñentes.
Do mesmo xeito, os fluxos poden non activarse completamente se a temperatura é demasiado baixa.Ao final da zona de remollo desérase un equilibrio térmico de todo o conxunto xusto antes da zona de refluxo.Suxírese un perfil de inmersión para diminuír calquera delta T entre compoñentes de diferentes tamaños ou se o conxunto de PCB é moi grande.Tamén se recomenda un perfil de inmersión para diminuír o baleiro nos paquetes de tipo matriz de área.
Zona de refluxo
A terceira sección, a zona de refluxo, tamén se denomina "tempo por riba do refluxo" ou "tempo por riba do liquidus" (TAL), e é a parte do proceso onde se alcanza a temperatura máxima.Unha consideración importante é a temperatura máxima, que é a temperatura máxima permitida de todo o proceso.Un pico de temperatura común é de 20–40 °C por riba de liquidus. Este límite está determinado polo compoñente do conxunto coa menor tolerancia ás altas temperaturas (O compoñente máis susceptible a danos térmicos).Unha pauta estándar é restar 5 °C da temperatura máxima que pode soportar o compoñente máis vulnerable para chegar á temperatura máxima para o proceso.É importante controlar a temperatura do proceso para evitar que supere este límite.
Ademais, as altas temperaturas (máis de 260 °C) poden causar danos nas matrices internas dos compoñentes SMT e favorecer o crecemento intermetálico.Pola contra, unha temperatura que non é o suficientemente quente pode impedir que a pasta refluxa adecuadamente.
O tempo por encima de liquidus (TAL), ou tempo por riba do refluxo, mide o tempo que a soldadura é líquida.O fluxo reduce a tensión superficial na unión dos metais para lograr a unión metalúrxica, permitindo que as esferas individuais de po de soldadura se combinen.Se o tempo do perfil supera a especificación do fabricante, o resultado pode ser unha activación ou un consumo prematuros do fluxo, que "seca" efectivamente a pasta antes da formación da unión de soldadura.Unha relación tempo/temperatura insuficiente provoca unha diminución da acción de limpeza do fluxo, o que provoca unha humectación deficiente, unha eliminación inadecuada do disolvente e do fluxo e, posiblemente, xuntas de soldadura defectuosas.
Os expertos adoitan recomendar o TAL máis curto posible, con todo, a maioría das pastas especifican un TAL mínimo de 30 segundos, aínda que non parece haber unha razón clara para ese tempo específico.Unha posibilidade é que haxa lugares no PCB que non se midan durante o perfilado e, polo tanto, establecer o tempo mínimo permitido en 30 segundos reduce as posibilidades de que unha área non medida non refluxa.Un tempo mínimo de refluxo alto tamén proporciona unha marxe de seguridade contra os cambios de temperatura do forno.O tempo de humectación idealmente permanece por debaixo dos 60 segundos por encima de liquidus.O tempo adicional por encima de liquidus pode provocar un crecemento intermetálico excesivo, o que pode provocar fraxilidade das articulacións.O taboleiro e os compoñentes tamén se poden danar durante períodos prolongados con liquidus, e a maioría dos compoñentes teñen un límite de tempo ben definido para canto tempo poden estar expostos a temperaturas superiores a un máximo determinado.
Demasiado pouco tempo por encima de liquidus pode atrapar disolventes e fluxos e crear o potencial de xuntas frías ou apagadas, así como baleiros de soldadura.
Zona de refrixeración
A última zona é unha zona de arrefriamento para arrefriar gradualmente a placa procesada e solidificar as unións de soldadura.O arrefriamento axeitado inhibe a formación intermetálica excesiva ou o choque térmico dos compoñentes.As temperaturas típicas na zona de refrixeración oscilan entre 30 e 100 °C (86–212 °F).Escóllese unha velocidade de arrefriamento rápida para crear unha estrutura de gran fino que sexa mecánicamente máis sólida.
[1] A diferenza da taxa de aceleración máxima, a taxa de baixada adoita ignorarse.Pode ser que a velocidade de rampla sexa menos crítica por encima de certas temperaturas, non obstante, a pendente máxima permitida para calquera compoñente debería aplicarse tanto se estea quentando como se arrefría.Normalmente suxírese unha velocidade de arrefriamento de 4 °C/s.É un parámetro a ter en conta á hora de analizar os resultados do proceso.
O termo "reflow" úsase para referirse á temperatura por encima da cal unha masa sólida de aliaxe de soldadura seguramente se fundirá (en oposición a simplemente suavizar).Se se arrefría por debaixo desta temperatura, a soldadura non fluirá.Quentada por riba dela unha vez máis, a soldadura volverá fluír, polo que "refluxa".
As técnicas modernas de montaxe de circuítos que usan a soldadura por refluxo non permiten necesariamente que a soldadura flúe máis dunha vez.Eles garanten que a soldadura granulada contida na pasta de soldadura supera a temperatura de refluxo da soldadura implicada.
Perfil térmico
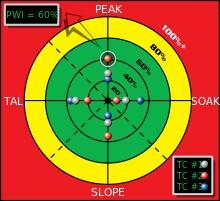
Unha representación gráfica do índice da ventá de proceso para un perfil térmico.
Na industria de fabricación de produtos electrónicos utilízase unha medida estatística, coñecida como Process Window Index (PWI) para cuantificar a robustez dun proceso térmico.PWI axuda a medir o ben que "encaixa" un proceso nun límite de proceso definido polo usuario coñecido como Límite de especificación. Cada perfil térmico clasifícase segundo como "encaixa" nunha xanela de proceso (o límite de especificación ou tolerancia).
O centro da xanela do proceso defínese como cero e o bordo extremo da xanela do proceso como 99%. Un PWI maior ou igual ao 100% indica que o perfil non procesa o produto dentro das especificacións.Un PWI do 99 % indica que o perfil procesa o produto dentro das especificacións, pero execútase no borde da xanela do proceso.Un PWI do 60 % indica que un perfil utiliza o 60 % da especificación do proceso.Ao usar valores PWI, os fabricantes poden determinar canto da ventá de proceso usa un perfil térmico particular.Un valor PWI máis baixo indica un perfil máis robusto.
Para a máxima eficiencia, calcúlanse valores de PWI separados para procesos de pico, pendente, refluxo e remollo dun perfil térmico.Para evitar a posibilidade de choque térmico que afecte á saída, débese determinar e nivelar a pendente máis pronunciada do perfil térmico.Os fabricantes usan software personalizado para determinar e diminuír con precisión a inclinación da pendente.Ademais, o software tamén recalibra automaticamente os valores PWI para os procesos de pico, pendente, refluxo e inmersión.Ao establecer os valores PWI, os enxeñeiros poden asegurarse de que o traballo de soldadura por refluxo non se sobrequente nin se arrefríe demasiado rápido.
Hora de publicación: 01-mar-2022