Az újrafolyós forrasztás egy olyan eljárás, amelynek során forrasztópasztát (forrasztópor és folyasztószer ragadós keverékét) használnak egy vagy több elektromos alkatrész ideiglenes rögzítésére az érintkezőfelületeikhez, majd az egész szerelvényt szabályozott hőhatásnak vetik alá, amely megolvasztja a forrasztóanyagot. , tartósan összeköti az ízületet.A felfűtést úgy lehet végrehajtani, hogy a szerelvényt visszafolyató kemencén vagy infralámpa alatt vezetjük át, vagy az egyes csatlakozásokat forró levegős ceruzával forrasztjuk.
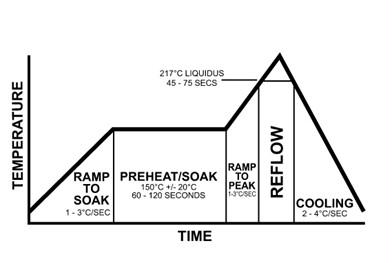
Az újrafolyós forrasztás a legelterjedtebb módszer a felületre szerelhető alkatrészek áramköri lapra történő rögzítésére, bár átmenőlyukakhoz is használható, ha a lyukakat megtöltjük forrasztópasztával, és a komponens vezetékeit a pasztán keresztül vezetjük be.Mivel a hullámforrasztás egyszerűbb és olcsóbb lehet, az újrafolyatás általában nem használható tiszta átmenőlyukú lapokon.Ha SMT- és THT-komponenseket tartalmazó táblákon használják, az átmenő furat-visszaáramlás lehetővé teszi a hullámforrasztási lépés kiiktatását az összeszerelési folyamatból, ami potenciálisan csökkenti az összeszerelési költségeket.
Az újrafolytatási eljárás célja a forrasztás megolvasztása és a szomszédos felületek felmelegítése anélkül, hogy az elektromos alkatrészek túlmelegednének és károsodnának.A hagyományos újrafolyós forrasztási eljárásban általában négy szakasz van, amelyeket "zónáknak" neveznek, és mindegyiknek külön termikus profilja van: előmelegítés, hőkezelés (gyakran csak áztatásra rövidítve), visszafolyatás és hűtés.
Előmelegítési zóna
A maximális meredekség egy hőmérséklet/idő összefüggés, amely azt méri, hogy milyen gyorsan változik a hőmérséklet a nyomtatott áramköri lapon.Az előmelegítési zóna gyakran a leghosszabb a zónák közül, és gyakran meghatározza a rámpa sebességét.A felfutási sebesség általában valahol 1,0 °C és 3,0 °C között van másodpercenként, gyakran másodpercenként 2,0 °C és 3,0 °C (4 °F és 5 °F) közé esik.Ha a sebesség meghaladja a maximális lejtőt, az alkatrészek hősokk vagy repedés következtében megsérülhetnek.
A forrasztópaszta fröcskölő hatású is lehet.Az előmelegítő rész az a hely, ahol a pasztában lévő oldószer elkezd elpárologni, és ha az emelkedési sebesség (vagy hőmérsékleti szint) túl alacsony, a fluxus illékony anyagainak elpárologtatása nem teljes.
Termikus áztatási zóna
A második szakasz, a termikus áztatás, jellemzően 60-120 másodperces expozíció a forrasztópaszta illékony komponenseinek eltávolítására és a folyasztószerek aktiválására (lásd a folyasztószert), ahol a folyasztószer komponensei megkezdik az oxidációs redukciót az alkatrészek vezetékein és párnáin.A túl magas hőmérséklet a forrasztás fröccsenéséhez vagy golyósodáshoz, valamint a paszta, a rögzítőbetétek és az alkatrészek végződéseinek oxidációjához vezethet.
Hasonlóképpen előfordulhat, hogy a fluxusok nem aktiválódnak teljesen, ha a hőmérséklet túl alacsony.Az áztatási zóna végén a teljes szerelvény termikus egyensúlya kívánatos közvetlenül a visszafolyási zóna előtt.Javasoljuk, hogy az áztatási profilt csökkentse a T delta a különböző méretű alkatrészek között, vagy ha a PCB egység nagyon nagy.Az áztatási profil is javasolt a kiürülés csökkentése érdekében a területtömb típusú csomagokban.
Reflow zóna
A harmadik szakaszt, a visszafolyási zónát „visszafolyás feletti időnek” vagy „likvidusz feletti időnek” (TAL) is nevezik, és ez a folyamat azon része, ahol elérjük a maximális hőmérsékletet.Fontos szempont a csúcshőmérséklet, amely a teljes folyamat maximálisan megengedhető hőmérséklete.Az általános csúcshőmérséklet 20-40 °C-kal a likvidus felett van. Ezt a határértéket az a komponens határozza meg, amely a szerelvényen a legalacsonyabb magas hőmérséklettűréssel rendelkezik (A hőkárosodásra leginkább érzékeny alkatrész).A szabványos irányelv szerint 5 °C-ot le kell vonni abból a maximális hőmérsékletből, amelyet a legsérülékenyebb komponens el tud tartani, hogy elérje a folyamat maximális hőmérsékletét.Fontos figyelni a folyamat hőmérsékletét, hogy ne lépje túl ezt a határértéket.
Ezenkívül a magas hőmérséklet (260 °C felett) károsíthatja az SMT alkatrészek belső szerszámait, és elősegítheti az intermetallikus növekedést.Ezzel szemben a nem elég meleg hőmérséklet megakadályozhatja a paszta megfelelő újrafolyását.
A likvidusz feletti idő (TAL), vagy a visszafolyás feletti idő azt méri, hogy a forrasztás mennyi ideig folyékony.A fluxus csökkenti a felületi feszültséget a fémek találkozásánál, hogy kohászati kötést hozzon létre, lehetővé téve az egyes forrasztópor gömbök egyesülését.Ha a profil idő meghaladja a gyártó által előírtakat, akkor az eredmény idő előtti folyasztószer aktiválódás vagy elhasználódás lehet, ami hatékonyan „szárítja” a pasztát a forrasztási kötés kialakulása előtt.Az elégtelen idő/hőmérséklet kapcsolat a folyasztószer tisztító hatásának csökkenését okozza, ami gyenge nedvesítést, az oldószer és a folyasztószer nem megfelelő eltávolítását, és esetleg hibás forrasztási kötéseket eredményez.
A szakértők általában a lehető legrövidebb TAL-t ajánlják, azonban a legtöbb paszta minimum 30 másodperces TAL-t ad meg, bár úgy tűnik, nincs egyértelmű ok erre a konkrét időre.Az egyik lehetőség az, hogy a NYÁK-on vannak olyan helyek, amelyeket a profilalkotás során nem mérnek, ezért a minimálisan megengedett idő 30 másodpercre állítása csökkenti annak esélyét, hogy a nem mért terület ne folyjon vissza.A magas minimális visszafolyási idő biztonsági résszel is rendelkezik a sütő hőmérséklet-változásaival szemben.A nedvesítési idő ideális esetben 60 másodperc alatt marad a likvidus felett.A likvidus feletti további idő túlzott intermetallikus növekedést okozhat, ami az ízületek törékenységéhez vezethet.A kártya és a komponensek a likviditáson túl hosszú ideig is megsérülhetnek, és a legtöbb alkatrésznek jól meghatározott időkorlátja van arra vonatkozóan, hogy mennyi ideig lehetnek kitéve egy adott maximum feletti hőmérsékletnek.
Ha túl kevés idő van a folyadék felett, az oldószereket és folyasztószert csapdába ejthet, és hideg vagy tompa illesztéseket, valamint forrasztási üregeket okozhat.
Hűtőzóna
Az utolsó zóna egy hűtőzóna a feldolgozott tábla fokozatos hűtésére és a forrasztási kötések megszilárdítására.A megfelelő hűtés megakadályozza a felesleges intermetallikus képződést vagy az alkatrészeket érő hősokkot.A hűtési zóna jellemző hőmérséklete 30–100 °C (86–212 °F).A gyors hűtési sebességet úgy választják meg, hogy finom szemcsés szerkezetet hozzanak létre, amely mechanikailag a legmegbízhatóbb.
[1] A maximális felfutási sebességgel ellentétben a felfutási-lefutási sebességet gyakran figyelmen kívül hagyják.Előfordulhat, hogy bizonyos hőmérsékletek felett a rámpasebesség kevésbé kritikus, azonban minden alkatrészre a megengedett legnagyobb lejtést kell alkalmazni, függetlenül attól, hogy az alkatrész felmelegszik vagy lehűl.Általában a 4°C/s hűtési sebesség javasolt.Ez egy olyan paraméter, amelyet figyelembe kell venni a folyamat eredményeinek elemzésekor.
Az „újrafolyás” kifejezés azt a hőmérsékletet jelenti, amely felett a szilárd forrasztóötvözet biztosan megolvad (a pusztán meglágyulással szemben).Ha ez alá a hőmérséklet alá hűtjük, a forraszanyag nem fog folyni.Még egyszer felmelegítve a forraszanyag újra folyni fog – tehát „újrafolyik”.
A reflow forrasztást alkalmazó modern áramkör-összeállítási technikák nem feltétlenül teszik lehetővé a forrasztóanyag többszöri áramlását.Garantálják, hogy a forrasztópasztában lévő granulált forrasztóanyag meghaladja az érintett forraszanyag visszafolyási hőmérsékletét.
Termikus profilozás
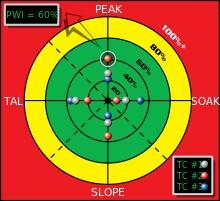
A Termikus profil Process Window Index grafikus ábrázolása.
Az elektronikai gyártóiparban egy statisztikai mérőszámot, az úgynevezett Process Window Indexet (PWI) használnak a termikus folyamat robusztusságának számszerűsítésére.A PWI segít mérni, hogy egy folyamat mennyire „illeszkedik” a felhasználó által definiált folyamathatárhoz, amelyet specifikációs határként ismerünk. Minden egyes termikus profilt aszerint rangsorolnak, hogy hogyan „illeszkedik” a folyamatablakhoz (a specifikáció vagy a tűréshatár).
A folyamatablak középpontja nulla, a folyamatablak szélső széle pedig 99%. A 100%-nál nagyobb vagy egyenlő PWI azt jelzi, hogy a profil nem a specifikáción belül dolgozza fel a terméket.A 99%-os PWI azt jelzi, hogy a profil a specifikáción belül dolgozza fel a terméket, de a folyamatablak szélén fut.A 60%-os PWI azt jelzi, hogy egy profil a folyamatspecifikáció 60%-át használja.A PWI-értékek használatával a gyártók meghatározhatják, hogy egy adott termikus profil mekkora részét használja fel a folyamatablakból.Az alacsonyabb PWI-érték robusztusabb profilt jelez.
A maximális hatékonyság érdekében külön PWI-értékeket számítanak ki a hőprofil csúcs-, lejtő-, visszafolyási és beázási folyamataira.A teljesítményt befolyásoló hősokk lehetőségének elkerülése érdekében a hőprofil legmeredekebb lejtőjét kell meghatározni és kiegyenlíteni.A gyártók egyedi szoftvert használnak a lejtő meredekségének pontos meghatározására és csökkentésére.Ezenkívül a szoftver automatikusan újrakalibrálja a PWI-értékeket a csúcs-, lejtő-, visszafolyás- és beázási folyamatokhoz.A PWI értékek beállításával a mérnökök biztosíthatják, hogy az újrafolyós forrasztási munka ne melegedjen túl vagy hűljön le túl gyorsan.
Feladás időpontja: 2022-01-01