Penyolderan reflow adalah proses di mana pasta solder (campuran lengket dari bubuk solder dan fluks) digunakan untuk menempelkan sementara satu atau beberapa komponen listrik ke bantalan kontaknya, setelah itu seluruh rakitan dikenai panas terkontrol, yang melelehkan solder. , menghubungkan sambungan secara permanen.Pemanasan dapat dilakukan dengan melewatkan rakitan melalui oven reflow atau di bawah lampu inframerah atau dengan menyolder masing-masing sambungan dengan pensil udara panas.
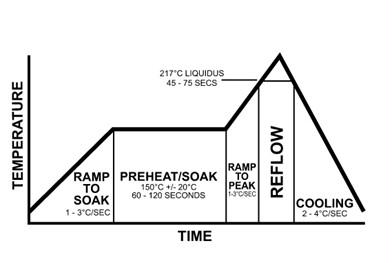
Penyolderan reflow adalah metode paling umum untuk memasang komponen pemasangan permukaan ke papan sirkuit, meskipun metode ini juga dapat digunakan untuk komponen lubang tembus dengan mengisi lubang dengan pasta solder dan memasukkan kabel komponen melalui pasta.Karena penyolderan gelombang bisa lebih sederhana dan lebih murah, reflow umumnya tidak digunakan pada papan lubang murni.Ketika digunakan pada papan yang berisi campuran komponen SMT dan THT, reflow melalui lubang memungkinkan langkah penyolderan gelombang dihilangkan dari proses perakitan, sehingga berpotensi mengurangi biaya perakitan.
Tujuan dari proses reflow adalah untuk melelehkan solder dan memanaskan permukaan yang bersebelahan, tanpa menyebabkan panas berlebih dan merusak komponen kelistrikan.Dalam proses penyolderan reflow konvensional, biasanya terdapat empat tahap, yang disebut "zona", masing-masing memiliki profil termal yang berbeda: pemanasan awal, rendaman termal (sering disingkat menjadi hanya rendam), reflow, dan pendinginan.
Zona pemanasan awal
Kemiringan maksimum adalah hubungan suhu/waktu yang mengukur seberapa cepat suhu pada papan sirkuit cetak berubah.Zona pemanasan awal sering kali merupakan zona yang paling panjang dan sering kali menentukan kecepatan ramp.Laju peningkatan biasanya berkisar antara 1,0 °C dan 3,0 °C per detik, sering kali turun antara 2,0 °C dan 3,0 °C (4 °F hingga 5 °F) per detik.Jika laju melebihi kemiringan maksimum, kerusakan pada komponen akibat sengatan panas atau keretakan dapat terjadi.
Pasta solder juga dapat menimbulkan efek percikan.Bagian pemanasan awal adalah saat pelarut dalam pasta mulai menguap, dan jika laju kenaikan (atau tingkat suhu) terlalu rendah, penguapan fluks volatil tidak sempurna.
Zona rendam termal
Bagian kedua, rendam termal, biasanya merupakan paparan 60 hingga 120 detik untuk menghilangkan zat volatil pasta solder dan mengaktifkan fluks (lihat fluks), di mana komponen fluks mulai melakukan reduksi oksida pada kabel dan bantalan komponen.Suhu yang terlalu tinggi dapat menyebabkan percikan atau penggumpalan solder serta oksidasi pasta, bantalan pemasangan, dan penghentian komponen.
Demikian pula, fluks mungkin tidak aktif sepenuhnya jika suhu terlalu rendah.Pada akhir zona perendaman, kesetimbangan termal seluruh rakitan diinginkan tepat sebelum zona reflow.Profil rendam disarankan untuk mengurangi delta T antar komponen dengan berbagai ukuran atau jika rakitan PCB sangat besar.Profil rendam juga disarankan untuk mengurangi kekosongan pada paket tipe susunan area.
Zona aliran balik
Bagian ketiga, zona reflow, juga disebut sebagai “waktu di atas reflow” atau “waktu di atas likuidus” (TAL), dan merupakan bagian dari proses dimana suhu maksimum tercapai.Pertimbangan penting adalah suhu puncak, yang merupakan suhu maksimum yang diijinkan dari keseluruhan proses.Suhu puncak yang umum adalah 20–40 °C di atas cairan. Batas ini ditentukan oleh komponen pada rakitan yang memiliki toleransi terendah terhadap suhu tinggi (Komponen paling rentan terhadap kerusakan termal).Pedoman standarnya adalah mengurangi 5 °C dari suhu maksimum yang dapat dipertahankan oleh komponen yang paling rentan untuk mencapai suhu maksimum untuk proses.Penting untuk memantau suhu proses agar tidak melebihi batas ini.
Selain itu, suhu tinggi (di atas 260 °C) dapat menyebabkan kerusakan pada cetakan internal komponen SMT serta mendorong pertumbuhan intermetalik.Sebaliknya, suhu yang tidak cukup panas dapat menyebabkan pasta tidak dapat mengalir kembali dengan baik.
Waktu di atas likuidus (TAL), atau waktu di atas reflow, mengukur berapa lama solder berbentuk cair.Fluks tersebut mengurangi tegangan permukaan pada titik persimpangan logam untuk menghasilkan ikatan metalurgi, sehingga memungkinkan masing-masing bola bubuk solder untuk bergabung.Jika waktu profil melebihi spesifikasi pabrikan, akibatnya mungkin aktivasi atau konsumsi fluks prematur, yang secara efektif “mengeringkan” pasta sebelum pembentukan sambungan solder.Hubungan waktu/suhu yang tidak memadai menyebabkan penurunan aksi pembersihan fluks, mengakibatkan pembasahan yang buruk, penghilangan pelarut dan fluks yang tidak memadai, dan kemungkinan sambungan solder yang rusak.
Para ahli biasanya merekomendasikan TAL sesingkat mungkin, namun sebagian besar pasta menentukan TAL minimum 30 detik, meskipun tampaknya tidak ada alasan yang jelas untuk waktu spesifik tersebut.Salah satu kemungkinannya adalah ada tempat pada PCB yang tidak diukur selama pembuatan profil, dan oleh karena itu, menyetel waktu minimum yang diperbolehkan menjadi 30 detik akan mengurangi kemungkinan area yang tidak diukur tidak mengalir kembali.Waktu reflow minimum yang tinggi juga memberikan margin keamanan terhadap perubahan suhu oven.Waktu pembasahan idealnya berada di bawah 60 detik di atas likuidus.Tambahan waktu di atas likuidus dapat menyebabkan pertumbuhan intermetalik yang berlebihan, yang dapat menyebabkan kerapuhan sendi.Papan dan komponen juga dapat rusak dalam waktu lama karena likuid, dan sebagian besar komponen memiliki batas waktu yang jelas mengenai berapa lama komponen tersebut dapat terkena suhu pada suhu maksimum tertentu.
Terlalu sedikit waktu di atas likuidus dapat memerangkap pelarut dan fluks serta menimbulkan potensi sambungan dingin atau kusam serta rongga solder.
Zona pendinginan
Zona terakhir adalah zona pendinginan untuk mendinginkan papan yang diproses secara bertahap dan memperkuat sambungan solder.Pendinginan yang tepat menghambat pembentukan intermetalik berlebih atau kejutan termal pada komponen.Suhu umum di zona pendinginan berkisar antara 30–100 °C (86–212 °F).Laju pendinginan yang cepat dipilih untuk menciptakan struktur butiran halus yang paling sehat secara mekanis.
[1] Berbeda dengan laju peningkatan maksimum, laju penurunan sering kali diabaikan.Mungkin saja laju ramp kurang kritis di atas suhu tertentu, namun kemiringan maksimum yang diijinkan untuk setiap komponen harus berlaku baik komponen sedang memanas atau mendingin.Laju pendinginan 4°C/s biasanya disarankan.Ini adalah parameter yang perlu dipertimbangkan ketika menganalisis hasil proses.
Istilah "reflow" digunakan untuk merujuk pada suhu di atas mana massa padat paduan solder pasti akan meleleh (bukan hanya melunak).Jika didinginkan di bawah suhu ini, solder tidak akan mengalir.Dipanaskan di atasnya sekali lagi, solder akan mengalir lagi—karenanya "mengalir kembali".
Teknik perakitan sirkuit modern yang menggunakan penyolderan reflow tidak selalu memungkinkan solder mengalir lebih dari satu kali.Mereka menjamin bahwa butiran solder yang terkandung dalam pasta solder melebihi suhu reflow solder yang terlibat.
Profil termal
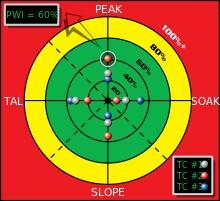
Representasi grafis dari Indeks Jendela Proses untuk profil termal.
Dalam industri manufaktur elektronik, ukuran statistik, yang dikenal sebagai Process Window Index (PWI) digunakan untuk mengukur ketahanan suatu proses termal.PWI membantu mengukur seberapa baik suatu proses "cocok" ke dalam batas proses yang ditentukan pengguna yang dikenal sebagai Batas Spesifikasi. Setiap profil termal diberi peringkat berdasarkan seberapa "sesuai" dalam jendela proses (batas spesifikasi atau toleransi).
Bagian tengah jendela proses didefinisikan sebagai nol, dan tepi ekstrem jendela proses ditetapkan sebagai 99%. PWI yang lebih besar atau sama dengan 100% menunjukkan bahwa profil tidak memproses produk sesuai spesifikasi.PWI sebesar 99% menunjukkan bahwa profil memproses produk sesuai spesifikasi, namun berjalan di tepi jendela proses.PWI sebesar 60% menunjukkan suatu profil menggunakan 60% spesifikasi proses.Dengan menggunakan nilai PWI, produsen dapat menentukan berapa banyak jendela proses yang digunakan profil termal tertentu.Nilai PWI yang lebih rendah menunjukkan profil yang lebih kuat.
Untuk efisiensi maksimum, nilai PWI terpisah dihitung untuk proses puncak, kemiringan, reflow, dan rendam profil termal.Untuk menghindari kemungkinan kejutan termal mempengaruhi keluaran, kemiringan paling curam pada profil termal harus ditentukan dan diratakan.Pabrikan menggunakan perangkat lunak yang dibuat khusus untuk menentukan dan mengurangi kecuraman lereng secara akurat.Selain itu, perangkat lunak juga secara otomatis mengkalibrasi ulang nilai PWI untuk proses puncak, kemiringan, reflow, dan rendam.Dengan menetapkan nilai PWI, para insinyur dapat memastikan bahwa pekerjaan penyolderan reflow tidak terlalu panas atau dingin terlalu cepat.
Waktu posting: 01-03-2022