La saldatura a riflusso è un processo in cui una pasta saldante (una miscela appiccicosa di polvere di saldatura e flusso) viene utilizzata per collegare temporaneamente uno o più componenti elettrici ai relativi cuscinetti di contatto, dopodiché l'intero assieme viene sottoposto a calore controllato, che scioglie la saldatura. , collegando permanentemente il giunto.Il riscaldamento può essere ottenuto facendo passare l'insieme attraverso un forno di rifusione o sotto una lampada a infrarossi o saldando i singoli giunti con una matita ad aria calda.
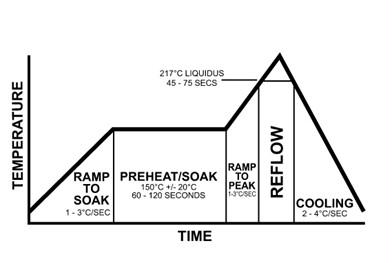
La saldatura a rifusione è il metodo più comune per collegare componenti a montaggio superficiale a un circuito stampato, sebbene possa essere utilizzata anche per componenti a foro passante riempiendo i fori con pasta saldante e inserendo i cavi del componente attraverso la pasta.Poiché la saldatura ad onda può essere più semplice ed economica, il reflow non viene generalmente utilizzato su schede a foro passante puro.Se utilizzato su schede contenenti un mix di componenti SMT e THT, il riflusso a foro passante consente di eliminare la fase di saldatura a onda dal processo di assemblaggio, riducendo potenzialmente i costi di assemblaggio.
L'obiettivo del processo di rifusione è sciogliere la saldatura e riscaldare le superfici adiacenti, senza surriscaldare e danneggiare i componenti elettrici.Nel processo di saldatura a rifusione convenzionale, ci sono solitamente quattro fasi, chiamate "zone", ciascuna con un profilo termico distinto: preriscaldamento, immersione termica (spesso abbreviata semplicemente in immersione), rifusione e raffreddamento.
Zona di preriscaldamento
La pendenza massima è una relazione temperatura/tempo che misura la velocità con cui cambia la temperatura sul circuito stampato.La zona di preriscaldamento è spesso la più lunga delle zone e spesso stabilisce la velocità di rampa.La velocità di aumento è solitamente compresa tra 1,0 °C e 3,0 °C al secondo, spesso scende tra 2,0 °C e 3,0 °C (da 4 °F a 5 °F) al secondo.Se la velocità supera la pendenza massima, possono verificarsi danni ai componenti dovuti a shock termico o fessurazioni.
La pasta saldante può anche avere un effetto a spruzzo.La sezione di preriscaldamento è il punto in cui il solvente nella pasta inizia ad evaporare e, se la velocità di aumento (o il livello di temperatura) è troppo bassa, l'evaporazione dei flussi volatili è incompleta.
Zona di immersione termica
La seconda sezione, immersione termica, è tipicamente un'esposizione da 60 a 120 secondi per la rimozione delle sostanze volatili della pasta saldante e l'attivazione dei flussi (vedi flusso), dove i componenti del flusso iniziano la riduzione dell'ossido sui conduttori e sulle piazzole dei componenti.Una temperatura troppo elevata può causare schizzi o formazione di palline di saldatura, nonché ossidazione della pasta, dei cuscinetti di fissaggio e delle terminazioni dei componenti.
Allo stesso modo, i flussi potrebbero non attivarsi completamente se la temperatura è troppo bassa.Alla fine della zona di immersione si desidera un equilibrio termico dell'intero assieme appena prima della zona di riflusso.Si consiglia un profilo di immersione per ridurre qualsiasi delta T tra componenti di dimensioni variabili o se il gruppo PCB è molto grande.Si consiglia inoltre un profilo di assorbimento per ridurre lo svuotamento nei pacchetti di tipo array di aree.
Zona di riflusso
La terza sezione, la zona di riflusso, è chiamata anche “tempo sopra il riflusso” o “tempo sopra il liquidus” (TAL), ed è la parte del processo in cui viene raggiunta la temperatura massima.Una considerazione importante è la temperatura di picco, che è la temperatura massima consentita dell'intero processo.Una temperatura di picco comune è 20–40 °C superiore al liquido. Questo limite è determinato dal componente dell'assieme con la tolleranza più bassa alle alte temperature (il componente più suscettibile al danno termico).Una linea guida standard consiste nel sottrarre 5 °C dalla temperatura massima che il componente più vulnerabile può sostenere per arrivare alla temperatura massima per il processo.È importante monitorare la temperatura del processo per evitare che superi questo limite.
Inoltre, le alte temperature (oltre 260 °C) possono causare danni agli stampi interni dei componenti SMT e favorire la crescita intermetallica.Al contrario, una temperatura non sufficientemente elevata può impedire alla pasta di rifluire adeguatamente.
Il tempo sopra il liquidus (TAL), o tempo sopra il riflusso, misura per quanto tempo la saldatura rimane liquida.Il flusso riduce la tensione superficiale nella giunzione dei metalli per realizzare il legame metallurgico, consentendo alle singole sfere di polvere saldante di combinarsi.Se il tempo del profilo supera le specifiche del produttore, il risultato potrebbe essere un'attivazione o un consumo prematuro del flusso, “asciugando” di fatto la pasta prima della formazione del giunto di saldatura.Un rapporto tempo/temperatura insufficiente provoca una diminuzione dell'azione pulente del fondente, con conseguente scarsa bagnatura, rimozione inadeguata del solvente e del fondente e possibili giunti di saldatura difettosi.
Gli esperti solitamente raccomandano il TAL più breve possibile, tuttavia, la maggior parte delle paste specifica un TAL minimo di 30 secondi, anche se non sembra esserci una ragione chiara per quel tempo specifico.Una possibilità è che ci siano punti sul PCB che non vengono misurati durante la profilazione e pertanto, impostando il tempo minimo consentito su 30 secondi si riducono le possibilità che un'area non misurata non rifluisca.Un tempo di riflusso minimo elevato fornisce inoltre un margine di sicurezza contro le variazioni di temperatura del forno.Il tempo di bagnatura rimane idealmente inferiore a 60 secondi sopra il liquidus.Un tempo aggiuntivo al di sopra del liquido può causare un'eccessiva crescita intermetallica, che può portare alla fragilità delle articolazioni.La scheda e i componenti possono anche essere danneggiati per periodi prolungati durante il liquidus e la maggior parte dei componenti ha un limite di tempo ben definito per quanto tempo possono essere esposti a temperature superiori a un determinato massimo.
Un tempo troppo breve al di sopra del liquidus può intrappolare solventi e flusso e creare il potenziale per giunti freddi o opachi, nonché vuoti di saldatura.
Zona di raffreddamento
L'ultima zona è una zona di raffreddamento per raffreddare gradualmente la scheda lavorata e solidificare i giunti di saldatura.Un raffreddamento adeguato inibisce la formazione eccessiva di elementi intermetallici o lo shock termico dei componenti.Le temperature tipiche nella zona di raffreddamento vanno da 30 a 100 ° C (86–212 ° F).Viene scelta una velocità di raffreddamento rapida per creare una struttura a grana fine che sia meccanicamente più solida.
[1] A differenza del tasso massimo di accelerazione, il tasso di decelerazione viene spesso ignorato.È possibile che la velocità di rampa sia meno critica al di sopra di determinate temperature, tuttavia, la pendenza massima consentita per qualsiasi componente dovrebbe applicarsi sia che il componente si stia riscaldando o raffreddando.Viene comunemente suggerita una velocità di raffreddamento di 4°C/s.È un parametro da considerare quando si analizzano i risultati del processo.
Il termine "riflusso" è usato per riferirsi alla temperatura al di sopra della quale una massa solida di lega di saldatura si scioglierà sicuramente (invece che semplicemente ammorbidirsi).Se raffreddata al di sotto di questa temperatura, la saldatura non scorrerà.Riscaldata sopra ancora una volta, la saldatura scorrerà di nuovo, quindi "riflusso".
Le moderne tecniche di assemblaggio dei circuiti che utilizzano la saldatura a rifusione non consentono necessariamente alla saldatura di fluire più di una volta.Garantiscono che la lega saldante granulata contenuta nella pasta saldante superi la temperatura di rifusione della lega saldante coinvolta.
Profilazione termica
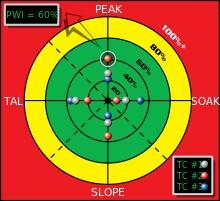
Una rappresentazione grafica dell'indice della finestra del processo per un profilo termico.
Nel settore della produzione elettronica, una misura statistica, nota come Process Window Index (PWI), viene utilizzata per quantificare la robustezza di un processo termico.PWI aiuta a misurare quanto bene un processo "si adatta" a un limite di processo definito dall'utente noto come limite di specifica. Ogni profilo termico viene classificato in base a come "si adatta" a una finestra di processo (la specifica o il limite di tolleranza).
Il centro della finestra del processo è definito come zero e il bordo estremo della finestra del processo come 99%. Un PWI maggiore o uguale al 100% indica che il profilo non elabora il prodotto entro le specifiche.Un PWI del 99% indica che il profilo elabora il prodotto entro le specifiche, ma viene eseguito al limite della finestra del processo.Un PWI del 60% indica che un profilo utilizza il 60% della specifica del processo.Utilizzando i valori PWI, i produttori possono determinare quanta finestra di processo utilizza un particolare profilo termico.Un valore PWI inferiore indica un profilo più robusto.
Per la massima efficienza, vengono calcolati valori PWI separati per i processi di picco, pendenza, riflusso e assorbimento di un profilo termico.Per evitare la possibilità che uno shock termico influenzi la potenza, è necessario determinare e livellare la pendenza più ripida del profilo termico.I produttori utilizzano software personalizzato per determinare e ridurre con precisione la pendenza del pendio.Inoltre, il software ricalibra automaticamente i valori PWI per i processi di picco, pendenza, riflusso e assorbimento.Impostando i valori PWI, gli ingegneri possono garantire che il lavoro di saldatura a riflusso non si surriscaldi o si raffreddi troppo rapidamente.
Orario di pubblicazione: 01-marzo-2022