Қайта ағынды дәнекерлеу - бұл дәнекерлеу пастасы (ұнтақты дәнекерлеу және флюстің жабысқақ қоспасы) бір немесе бірнеше электрлік компоненттерді олардың контакт алаңдарына уақытша бекіту үшін қолданылатын процесс, содан кейін бүкіл жинақ дәнекерленген еріткіш бақыланатын жылу әсеріне ұшырайды. , буынды тұрақты байланыстыру.Жылыту жинақты қайта ағынды пеш арқылы немесе инфрақызыл шамның астынан өткізу арқылы немесе жеке буындарды ыстық ауа қарындашымен дәнекерлеу арқылы жүзеге асырылуы мүмкін.
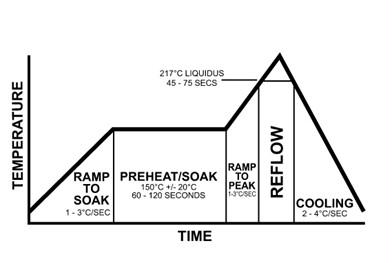
Қайта ағынмен дәнекерлеу - беткі қондырғы компоненттерін схемалық тақтаға бекітудің ең кең таралған әдісі, дегенмен ол тесіктерді дәнекерлеу пастасымен толтыру және құрамдас сымдарды паста арқылы енгізу арқылы тесігі бар компоненттер үшін де пайдаланылуы мүмкін.Толқынды дәнекерлеу оңайырақ және арзанырақ болуы мүмкін болғандықтан, қайта ағу әдетте таза тесік тақталарында қолданылмайды.Құрамында SMT және THT компоненттерінің қоспасы бар тақталарда пайдаланылған кезде саңылау арқылы қайта ағу толқынды дәнекерлеу қадамын құрастыру процесінен алып тастауға мүмкіндік береді, бұл құрастыру шығындарын әлеуетті түрде азайтады.
Қайта ағынды процестің мақсаты - электрлік компоненттерді қызып кетпей және зақымдамай, дәнекерлеуді балқыту және іргелес беттерді жылыту.Кәдімгі қайта ағынды дәнекерлеу процесінде әдетте әрқайсысының нақты жылу профилі бар «аймақтар» деп аталатын төрт кезең бар: алдын ала қыздыру, термиялық жібіту (көбінесе жай ғана сіңіру үшін қысқартылған), қайта ағу және салқындату.
Алдын ала қыздыру аймағы
Максималды көлбеу - басып шығарылған платадағы температураның қаншалықты жылдам өзгеретінін өлшейтін температура/уақыт қатынасы.Алдын ала қыздыру аймағы жиі аймақтардың ең ұзыны болып табылады және жиі рампа жылдамдығын белгілейді.Көтеру жылдамдығы әдетте секундына 1,0 °C және 3,0 °C аралығында болады, жиі секундына 2,0 °C және 3,0 °C (4 °F пен 5 °F) аралығында болады.Егер жылдамдық максималды көлбеуден асып кетсе, термиялық соққыдан немесе крекингтен компоненттердің зақымдалуы мүмкін.
Дәнекерлеу пастасы да шашыратқыш әсерге ие болуы мүмкін.Алдын ала қыздыру бөлімі пастадағы еріткіштің булана бастайтын жері болып табылады және көтерілу жылдамдығы (немесе температура деңгейі) тым төмен болса, ағынның ұшпа заттарының булануы толық емес.
Термиялық сіңіру аймағы
Екінші бөлім, термиялық сіңіру, әдетте дәнекерлеу пастасы ұшпа заттарын кетіруге және ағындарды белсендіруге арналған 60-120 секундтық экспозиция болып табылады (флюсті қараңыз), мұнда ағынның құрамдас бөліктері құрамдас өткізгіштер мен төсемдердегі тотықсыздануды бастайды.Тым жоғары температура дәнекерлеудің шашырауына немесе шарлануына, сондай-ақ пастаның, бекіту төсемдерінің және құрамдас ұштардың тотығуына әкелуі мүмкін.
Сол сияқты, егер температура тым төмен болса, ағындар толығымен белсендірілмеуі мүмкін.Тұндыру аймағының соңында бүкіл жинақтың жылулық тепе-теңдігі қайта ағу аймағының алдында қажет.Әртүрлі өлшемдегі құрамдас бөліктер арасында немесе ПХД жинағы өте үлкен болса, кез келген дельта T азайту үшін сулау профилі ұсынылады.Сондай-ақ, аумақтық массив түріндегі пакеттерде бос орындарды азайту үшін сулау профилі ұсынылады.
Қайта ағу аймағы
Үшінші бөлім, қайта ағу аймағы, сондай-ақ «қайта ағызудан жоғары уақыт» немесе «сұйықтықтан жоғары уақыт» (TAL) деп аталады және максималды температураға жеткен процестің бөлігі болып табылады.Маңызды мәселе - бұл бүкіл процестің максималды рұқсат етілген температурасы болып табылатын ең жоғары температура.Жалпы ең жоғары температура сұйықтықтан 20–40 °C жоғары. Бұл шек жоғары температураға ең төмен төзімділікпен құрамдас бөлікте анықталады (Термиялық зақымға ең сезімтал компонент).Стандартты нұсқау - ең осал құрамдас процесс үшін максималды температураға жету үшін шыдай алатын ең жоғары температурадан 5 °C шегеру.Бұл шектен асып кетпеу үшін процестің температурасын бақылау маңызды.
Сонымен қатар, жоғары температура (260 °C-тан жоғары) SMT құрамдастарының ішкі қалыптарына зақым келтіруі, сондай-ақ металларалық өсуді ынталандыруы мүмкін.Керісінше, жеткілікті ыстық емес температура пастаның жеткілікті түрде қайта ағуына кедергі келтіруі мүмкін.
Сұйықтықтан жоғары уақыт (TAL) немесе қайта ағудан жоғары уақыт дәнекерлеудің қаншалықты сұйықтық екенін өлшейді.Ағын металлургиялық байланысты жүзеге асыру үшін металдардың түйіскен жеріндегі беттік керілуді азайтады, бұл жеке дәнекерлеу ұнтағының сфераларын біріктіруге мүмкіндік береді.Егер профиль уақыты өндірушінің сипаттамасынан асып кетсе, нәтиже ағынның мерзімінен бұрын белсендірілуі немесе тұтынуы болуы мүмкін, дәнекерлеу қосылысы пайда болғанға дейін пастаны тиімді түрде «кептіреді».Уақыт/температура қатынасының жеткіліксіздігі ағынның тазалау әрекетінің төмендеуіне әкеледі, нәтижесінде нашар ылғалдануға, еріткіш пен флюстің жеткіліксіз алынуына және мүмкін ақаулы дәнекерлеу қосылыстарына әкеледі.
Сарапшылар әдетте мүмкін болатын ең қысқа TAL-ды ұсынады, дегенмен, пасталардың көпшілігі ең аз TAL 30 секундты көрсетеді, дегенмен нақты уақыттың нақты себебі жоқ сияқты.Мүмкіндіктердің бірі - ПХД-да профильдеу кезінде өлшенбейтін орындар бар, сондықтан ең аз рұқсат етілген уақытты 30 секундқа орнату өлшенбеген аумақтың қайта ағып кетпеу мүмкіндігін азайтады.Жоғары минималды қайта ағызу уақыты сонымен қатар пеш температурасының өзгеруіне қарсы қауіпсіздік шегін қамтамасыз етеді.Ылғалдау уақыты сұйықтықтан жоғары 60 секундтан төмен болады.Сұйықтықтың үстіндегі қосымша уақыт шамадан тыс металаралық өсуді тудыруы мүмкін, бұл буындардың сынғыштығына әкелуі мүмкін.Сондай-ақ, тақта мен құрамдас бөліктер сұйықтықтың өтуіне байланысты ұзақ уақыт бойы зақымдалуы мүмкін және көптеген құрамдастардың берілген максимумнан жоғары температураға қаншалықты әсер ететіні туралы нақты белгіленген уақыт шегі бар.
Сұйықтықтан жоғары тым аз уақыт еріткіштер мен ағынды ұстап қалуы мүмкін және суық немесе күңгірт буындардың, сондай-ақ дәнекерлеудің бос жерлерін тудыруы мүмкін.
Салқындату аймағы
Соңғы аймақ өңделген тақтаны бірте-бірте салқындату және дәнекерлеу қосылыстарын қатайту үшін салқындату аймағы болып табылады.Тиісті салқындату құрамдас бөліктерге артық металаралық түзілуді немесе термиялық соққыны болдырмайды.Салқындату аймағындағы әдеттегі температуралар 30–100 °C (86–212 °F) аралығында болады.Жылдам салқындату жылдамдығы механикалық тұрғыдан ең берік ұсақ түйіршікті құрылымды жасау үшін таңдалады.
[1] Ең жоғары көтерілу жылдамдығынан айырмашылығы, төмендеу жылдамдығы жиі еленбейді.Белгілі бір температурадан жоғары рампа жылдамдығы азырақ маңызды болуы мүмкін, дегенмен кез келген құрамдас үшін ең жоғары рұқсат етілген еңіс компонент қызып немесе салқындап жатқанына қарамастан қолданылуы керек.Әдетте 4°C/с салқындату жылдамдығы ұсынылады.Бұл процесс нәтижелерін талдау кезінде ескерілетін параметр.
«Қайта ағу» термині дәнекерленген қорытпаның қатты массасы балқитын (жай жұмсартуға қарағанда) жоғары температураға сілтеме жасау үшін қолданылады.Осы температурадан төмен салқындатылған болса, дәнекерлеу ағып кетпейді.Оның үстіне тағы бір рет жылытылған дәнекер қайтадан ағып кетеді, демек «қайта ағып кетеді».
Қайта ағынды дәнекерлеуді қолданатын заманауи тізбекті құрастыру әдістері дәнекерлеудің бірнеше рет ағуына мүмкіндік бермейді.Олар дәнекерлеу пастасының құрамындағы түйіршіктелген дәнекерленген дәнекерленген дәнекерлеудің қайта ағу температурасынан асып түсетініне кепілдік береді.
Термиялық профильдеу
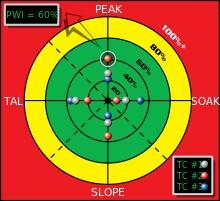
Термиялық профиль үшін Процесс терезесі индексінің графикалық көрінісі.
Электроника өндірісінде термиялық процестің беріктігін сандық бағалау үшін Процесс терезесінің индексі (PWI) деп аталатын статистикалық көрсеткіш қолданылады.PWI процестің Спецификация шегі деп аталатын пайдаланушы анықтаған процесс шегіне қаншалықты "сәйкес келетінін" өлшеуге көмектеседі. Әрбір жылу профилі процесс терезесінде (спецификация немесе төзімділік шегі) "сәйкестігі" бойынша бағаланады.
Процесс терезесінің ортасы нөл ретінде анықталады, ал процесс терезесінің шеткі шеті 99%. 100%-дан үлкен немесе оған тең PWI профиль спецификация аясында өнімді өңдемейтінін көрсетеді.99% PWI профильдің өнімді спецификация аясында өңдейтінін, бірақ процесс терезесінің шетінде жұмыс істейтінін көрсетеді.60% PWI профиль процесс сипаттамасының 60% пайдаланатынын көрсетеді.PWI мәндерін пайдалану арқылы өндірушілер белгілі бір жылу профилі процесс терезесінің қанша бөлігін пайдаланатынын анықтай алады.Төменгі PWI мәні сенімдірек профильді көрсетеді.
Максималды тиімділік үшін термиялық профильдің шыңы, көлбеу, қайта ағу және сіңіру процестері үшін бөлек PWI мәндері есептеледі.Шығаруға әсер ететін термиялық соққының мүмкіндігін болдырмау үшін жылу профиліндегі ең тік еңісті анықтау және тегістеу керек.Өндірушілер еңістің тіктігін дәл анықтау және азайту үшін арнайы құрастырылған бағдарламалық жасақтаманы пайдаланады.Бұған қоса, бағдарламалық құрал шың, көлбеу, қайта ағу және сіңіру процестері үшін PWI мәндерін автоматты түрде қайта калибрлейді.PWI мәндерін орнату арқылы инженерлер қайта ағынды дәнекерлеу жұмысының қызып кетпеуін немесе тым тез салқындамауын қамтамасыз ете алады.
Жіберу уақыты: 01 наурыз 2022 ж