Reflow soldering - бул процесс, мында бир же бир нече электрдик компоненттерди алардын контакттык аянтчаларына убактылуу тиркөө үчүн ширетүү пастасы (порошок жана флюстун жабышчаак аралашмасы) колдонулат, андан кийин бүт жамаат контролдонуучу жылуулукка дуушар болот, ал ширетүүчүнү эритет. , биротоло бириктирүүчү.Жылытуу монтажды кайра агызуучу мештен же инфракызыл лампанын астынан өткөрүү же айрым муундарды ысык аба карандаш менен ширетүү аркылуу ишке ашырылышы мүмкүн.
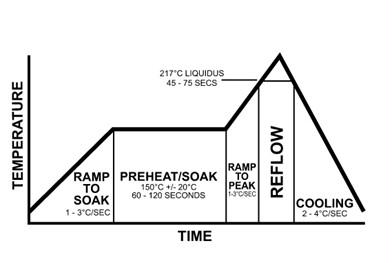
Reflow менен ширетүү - бул жер үстүндөгү монтаждоочу компоненттерди схемалык тактага туташтыруунун эң кеңири таралган ыкмасы, бирок аны тешикчелерди solder пастасы менен толтуруу жана паста аркылуу компонент өткөргүчтөрүн киргизүү аркылуу тешиктен өтүүчү компоненттер үчүн да колдонсо болот.Толкун менен ширетүү жөнөкөй жана арзаныраак болушу мүмкүн болгондуктан, рефлексия көбүнчө таза тешик такталарда колдонулбайт.SMT жана THT компоненттеринин аралашмасын камтыган такталарда колдонулганда, тешик аркылуу кайра агып чыгуу толкун менен ширетүү кадамын монтаждоо процессинен алып салууга мүмкүндүк берет, бул монтаждоо чыгымдарын азайтат.
Reflow процессинин максаты - электрдик компоненттерди ашыкча ысып жана зыян келтирбестен, ширетүүчүнү эритип, чектеш беттерди жылытуу.Кадимки кайра ширетүү процессинде, адатта, "зоналар" деп аталган төрт этап бар, алардын ар бири өзүнчө жылуулук профилине ээ: алдын ала ысытуу, термикалык чылоо (көбүнчө жөн эле чылап коюу үчүн кыскартылат), кайра агып чыгуу жана муздатуу.
Алдын ала ысытуу зонасы
Максималдуу эңкейиш - бул басылып чыккан схемадагы температуранын канчалык тез өзгөрүшүн өлчөй турган температура/убакыт мамилеси.Алдын ала ысытуу зонасы көбүнчө зоналардын эң узуну жана көбүнчө рампа ылдамдыгын белгилейт.Катуу ылдамдыгы секундасына 1,0 °C жана 3,0 °C арасында болот, көбүнчө секундасына 2,0 °C жана 3,0 °C (4 °Fтен 5 °F) чейин төмөндөйт.Эгерде ылдамдык максималдуу эңкейиштен ашса, термикалык шок же крекингден компоненттердин бузулушу мүмкүн.
Solder пастасы да чачыратуу таасирин тийгизиши мүмкүн.Алдын ала ысытуу бөлүмү пастадагы эриткичтин буулана баштаган жери, ал эми көтөрүлүү ылдамдыгы (же температура деңгээли) өтө төмөн болсо, агымдын учуучу заттардын бууланышы толук эмес.
Термикалык зонасы
Экинчи бөлүм, термикалык нымдоо, адатта, 60-120 секундалык экспозиция, ширетүүчү пастанын учуучу заттарын жок кылуу жана флюсторду активдештирүү (флюсту караңыз), мында флюстун компоненттери компоненттин өткөргүчтөрүндө жана төшөктөрүндө кычкылданууну баштайт.Өтө жогорку температура ширетүүчүнүн чачырашына же тополоңдоп кетишине, ошондой эле пастанын, тиркеме төшөлмөлөрүнүн жана тетиктердин бүтүмдөрүнүн кычкылданышына алып келиши мүмкүн.
Ошо сыяктуу эле, температура өтө төмөн болсо, флюстер толук иштетилбей калышы мүмкүн.Чылуу зонасынын аягында, кайра агып чыгуу зонасына чейин бүтүндөй жыйындын жылуулук тең салмактуулугу керек.Ар кандай өлчөмдөгү компоненттердин ортосундагы ар кандай дельтаны T азайтуу үчүн же ПХБ монтажы өтө чоң болсо, суу профили сунушталат.Аймактык массив тибиндеги пакеттерде боштукту азайтуу үчүн суу профили да сунушталат.
Reflow зонасы
Үчүнчү бөлүм, кайра агып чыгуу зонасы, ошондой эле "кайтадан агылган убакыт" же "ликвидациядан жогору убакыт" (TAL) деп аталат жана процесстин максималдуу температурага жеткен бөлүгү болуп саналат.Маанилүү жагдай - бул эң жогорку температура, бул процесстин максималдуу уруксат берилген температурасы.Кадимки эң жогорку температура ликвидустан 20–40 °C жогору. Бул чек жогорку температурага эң төмөнкү толеранттуулук менен курамдагы компонент тарабынан аныкталат (Термикалык бузулууга эң сезгич компонент).Стандарттык көрсөтмө эң аялуу компонент процесстин максималдуу температурасына жетиши үчүн туруштук бере ала турган максималдуу температурадан 5 °Cти алып салуу болуп саналат.Бул чектен ашып кетпеши үчүн процесстин температурасын көзөмөлдөө маанилүү.
Мындан тышкары, жогорку температуралар (260 °Cден жогору) SMT компоненттеринин ички калыптарына зыян келтириши мүмкүн, ошондой эле интерметаллдык өсүшкө өбөлгө түзөт.Тескерисинче, жетиштүү ысык эмес температура паста адекваттуу кайра агып кетишине жол бербейт.
Суюктуктан жогору убакыт (TAL) же кайра агып чыгуудан жогору убакыт, ширетүүчү суюктуктун канчалык узактыгын өлчөйт.Флюс металлургиялык байланышты ишке ашыруу үчүн металлдардын кесилишинде беттик чыңалууну азайтып, жеке ширетүү порошок чөйрөлөрүн бириктирүүгө мүмкүндүк берет.Эгерде профилдик убакыт өндүрүүчүнүн спецификациясынан ашып кетсе, натыйжа агымдын мөөнөтүнөн мурда активдешүүсү же керектөө болушу мүмкүн, паста ширетүүчү муун пайда болгонго чейин эффективдүү "кургатуу".Убакыт/температуранын жетишсиз байланышы агымдын тазалоо аракетинин төмөндөшүнө алып келет, натыйжада нымдуулук начар болот, эриткичтин жана флюстун жетишсиз алынышына жана мүмкүн болгон бузук ширетүүчү муундарга алып келет.
Адатта эксперттер мүмкүн болгон эң кыска TALды сунушташат, бирок көпчүлүк пасталарда эң аз 30 секунд TAL көрсөтүлөт, бирок ал белгилүү бир убакыттын так себеби жоктой сезилет.Мүмкүнчүлүктөрдүн бири - ПХБда профилдөө учурунда өлчөнгөн жерлер бар, ошондуктан минималдуу жол берилген убакытты 30 секундга коюу өлчөнгөн аймактын кайра агып кетпешинин мүмкүнчүлүгүн азайтат.Жогорку минималдуу кайра агып чыгуу убактысы да мештин температурасынын өзгөрүшүнө каршы коопсуздуктун чегин камсыз кылат.Нымдоо убактысы суюктуктан жогору 60 секунддан төмөн бойдон калууда.Суюктуктан жогору болгон кошумча убакыт ашыкча интерметаллдык өсүүгө алып келиши мүмкүн, бул биргелешкен морттукка алып келиши мүмкүн.Такта жана тетиктер суюктуктун үстүнөн узак убакыттарда бузулушу мүмкүн жана көпчүлүк компоненттерде берилген максимумдан ашык температурага канча убакытка чейин таасир эте тургандыгы так аныкталган мөөнөткө ээ.
Суюктуктан жогору өтө аз убакыт эриткичтерди жана агымдарды кармап калышы мүмкүн жана муздак же бүдөмүк муундарды, ошондой эле ширетүүчү боштуктарды пайда кылышы мүмкүн.
Муздатуу зонасы
Акыркы зонасы - кайра иштетилген тактаны акырындык менен муздатуу жана ширетүүчү муундарды бекемдөө үчүн муздатуу зонасы.Туура муздатуу компоненттеринин ашыкча intermetallic пайда же жылуулук шок тоскоол болот.Муздатуу зонасында типтүү температуралар 30–100 °C (86–212 °F) чейин.Тез муздатуу ылдамдыгы механикалык жактан эң жакшы болгон майда бүртүкчөлүү структураны түзүү үчүн тандалат.
[1] Максималдуу өсүү ылдамдыгынан айырмаланып, төмөндөө ылдамдыгы көп учурда этибарга алынбайт.Белгилүү бир температурадан жогору рампа ылдамдыгы анча критикалык эмес болушу мүмкүн, бирок кайсы бир компонент үчүн максималдуу жол берилген эңкейиш компонент ысып же муздап жатканына карабастан колдонулушу керек.Адатта, муздатуу ылдамдыгы 4°C/с сунушталат.Бул процесстин натыйжаларын талдоодо эске алынуучу параметр.
"Reflow" термини ширетүүчү эритмесинин катуу массасы эрип кете турган температурага карата колдонулат (жөн гана жумшартуудан айырмаланып).Бул температурадан төмөн муздаса, ширетүүчү агып кетпейт.Анын үстүнө дагы бир жолу жылытылгандан кийин, ширетүүчү кайра агып чыгат, демек, "кайра агып" кетет.
Reflow soldering колдонгон заманбап схемаларды чогултуу ыкмалары сөзсүз эле бир жолудан ашык агып жол бербейт.Алар ширетүүчү пастадагы гранулдаштырылган ширеткичтин кайра агып чыгуу температурасынан ашып кетээрине кепилдик беришет.
Термикалык профилдөө
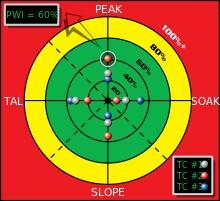
Жылуулук профили үчүн процесстик терезе индексинин графикалык көрүнүшү.
Электроника өндүрүшүндө процесстик терезе индекси (PWI) деп аталган статистикалык өлчөм жылуулук процессинин бекемдигин аныктоо үчүн колдонулат.PWI процесстин колдонуучу аныктаган процесстин Спецификация чеги деп аталган чегине канчалык "туураарын" өлчөөгө жардам берет. Ар бир жылуулук профили процесс терезесинде анын "канчалык туура келгени" боюнча рейтингге ээ (спецификация же толеранттуулук чеги).
Процесс терезесинин борбору нөл катары аныкталат, ал эми процесс терезесинин эң чети 99%. PWI 100%дан жогору же ага барабар профиль спецификациянын чегинде продуктуну иштетпей турганын көрсөтөт.PWI 99% профиль продуктту спецификациянын чегинде иштетээрин, бирок процесстин терезесинин четинде иштей турганын көрсөтөт.PWI 60% профиль процесстин спецификациясынын 60% колдоноорун көрсөтөт.PWI баалуулуктарын колдонуу менен өндүрүүчүлөр белгилүү бир жылуулук профили канчалык процесс терезесин колдоноорун аныктай алышат.Төмөнкү PWI мааниси кыйла бекем профилди көрсөтөт.
Максималдуу эффективдүүлүк үчүн жылуулук профилинин чокусу, эңкейиши, кайра агымы жана сууга түшүү процесстери үчүн өзүнчө PWI маанилери эсептелет.Чыгууга таасир этүүчү термикалык соккунун мүмкүнчүлүгүн болтурбоо үчүн, жылуулук профилиндеги эң тик эңкейишти аныктоо жана тегиздөө керек.Өндүрүүчүлөр эңкейиштин тиктигин так аныктоо жана азайтуу үчүн атайын программалык камсыздоону колдонушат.Кошумчалай кетсек, программалык камсыздоо ошондой эле эң жогорку, эңкейиш, кайра агып чыгуу жана нымдоо процесстери үчүн PWI маанилерин автоматтык түрдө кайра калибрлейт.PWI баалуулуктарын коюу менен, инженерлер кайра агып ширетүү иши өтө ысып же өтө тез муздап кетпешин камсыздай алышат.
Посттун убактысы: Март-01-2022