Повторното лемење е процес во кој се користи паста за лемење (леплива мешавина од лемење во прав и флукс) за привремено прицврстување на една или неколку електрични компоненти на нивните контактни влошки, по што целиот склоп е подложен на контролирана топлина, која го топи лемењето. , трајно поврзување на зглобот.Загревањето може да се постигне со поминување на склопот низ рерната за преточување или под инфрацрвена ламба или со лемење на поединечни споеви со молив за топол воздух.
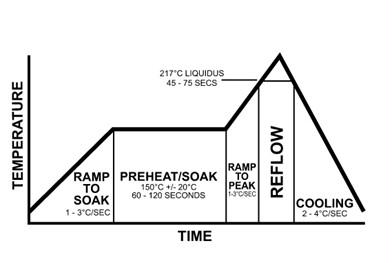
Повторното лемење е најчестиот метод за прицврстување на компонентите за површинска монтажа на таблата со коло, иако може да се користи и за компонентите низ дупки со полнење на дупките со паста за лемење и вметнување на каблите на компонентата низ пастата.Бидејќи лемењето со бранови може да биде поедноставно и поевтино, повторното лемење генерално не се користи на чисти плочи со отвори.Кога се користи на табли кои содржат мешавина од компоненти SMT и THT, повторното протекување низ дупка овозможува да се елиминира чекорот на лемење со бранови од процесот на склопување, што потенцијално ги намалува трошоците за склопување.
Целта на процесот на преточување е да се стопи лемењето и да се загреат соседните површини, без прегревање и оштетување на електричните компоненти.Во конвенционалниот процес на повторно лемење, обично има четири фази, наречени „зони“, секоја има посебен термички профил: претходно загревање, термичко натопување (често се скратува на само впивање), преточување и ладење.
Загрева зона
Максималниот наклон е врска температура/време што мери колку брзо се менува температурата на печатеното коло.Зоната за предзагревање е често најдолгата од зоните и често ја утврдува стапката на рампа.Стапката на рампа обично е некаде помеѓу 1,0 °C и 3,0 °C во секунда, честопати паѓа помеѓу 2,0 °C и 3,0 °C (4 °F до 5 °F) во секунда.Ако стапката го надминува максималниот наклон, може да дојде до оштетување на компонентите од термички шок или пукање.
Пастата за лемење може да има и ефект на прскање.Одделот за предзагревање е местото каде што растворувачот во пастата почнува да испарува, и ако стапката на пораст (или нивото на температурата) е премногу ниска, испарувањето на флуксните испарливи материи е нецелосно.
Термичка зона на натопување
Вториот дел, термичко натопување, е типично изложување од 60 до 120 секунди за отстранување на испарливите паста за лемење и активирање на флуксовите (види флукс), каде што компонентите на флуксот започнуваат со намалување на оксидацијата на каблите и перничињата на компонентите.Премногу висока температура може да доведе до прскање или топење на лемењето, како и оксидација на пастата, влошките за прицврстување и завршетоците на компонентите.
Слично на тоа, флуксот може да не се активира целосно ако температурата е премногу ниска.На крајот од зоната на натопување се посакува термичка рамнотежа на целото склопување непосредно пред зоната на преточување.Се предлага профил на натопување за намалување на делта Т помеѓу компоненти со различна големина или ако склопот на ПХБ е многу голем.Се препорачува и профил за натопување за да се намали празнењето во пакувањата од типот на низа од областа.
Зона на преточување
Третиот дел, зоната на преточување, се нарекува и „време над повторното проток“ или „време над течноста“ (TAL), и е дел од процесот каде што се постигнува максималната температура.Важна сметка е максималната температура, која е максималната дозволена температура на целиот процес.Вообичаената максимална температура е 20–40 °C над течноста. Оваа граница е одредена од компонентата на склопот со најниска толеранција за високи температури (компонента која е најподложна на термичко оштетување).Стандардно упатство е да се одземе 5 °C од максималната температура што најранливата компонента може да ја одржи за да стигне до максималната температура за процесот.Важно е да се следи температурата на процесот за да не ја надмине оваа граница.
Дополнително, високите температури (над 260 °C) може да предизвикаат оштетување на внатрешните матрици на SMT компонентите, како и да го поттикнат меѓуметалниот раст.Спротивно на тоа, температурата што не е доволно топла може да го спречи соодветното течење на пастата.
Времето над ликвидус (TAL), или времето над преточувањето, мери колку долго лемењето е течност.Флуксот го намалува површинскиот напон на спојот на металите за да се постигне металуршко поврзување, дозволувајќи им на поединечните сфери на прашокот за лемење да се комбинираат.Ако времето на профилот ја надминува спецификацијата на производителот, резултатот може да биде предвремено активирање или потрошувачка на флукс, ефективно „сушење“ на пастата пред формирањето на спојката за лемење.Недоволната врска време/температура предизвикува намалување на дејството на чистењето на флуксот, што резултира со лошо навлажнување, несоодветно отстранување на растворувачот и флуксот, а можеби и неисправни споеви за лемење.
Експертите обично препорачуваат најкраток можен TAL, сепак, повеќето пасти специфицираат минимум TAL од 30 секунди, иако се чини дека нема јасна причина за тоа конкретно време.Една од можностите е дека има места на ПХБ кои не се мерат за време на профилирањето, и затоа, поставувањето на минималното дозволено време на 30 секунди ги намалува шансите неизмерената површина да не тече повторно.Високото минимално време на преточување, исто така, обезбедува маргина на безбедност против промените на температурата во рерната.Времето на мокрење идеално останува под 60 секунди над течноста.Дополнително време над течноста може да предизвика прекумерен меѓуметален раст, што може да доведе до кршливост на зглобовите.Плочката и компонентите, исто така, може да се оштетат долго време во текот на течноста, а повеќето компоненти имаат добро дефинирано временско ограничување за тоа колку долго можат да бидат изложени на температури над даден максимум.
Премалку време над течноста може да ги зароби растворувачите и флуксот и да создаде потенцијал за ладни или досадни споеви, како и празнини за лемење.
Зона за ладење
Последната зона е зона за ладење за постепено ладење на обработената плоча и зацврстување на споеви за лемење.Правилното ладење го инхибира прекумерното меѓуметално формирање или термички шок на компонентите.Типичните температури во зоната за ладење се движат од 30–100 °C (86–212 °F).Избрана е брза стапка на ладење за да се создаде фино зрнеста структура која е механички најиздржлива.
[1] За разлика од максималната стапка на зголемување, стапката на рампа-надолу често се игнорира.Можеби стапката на рампата е помалку критична над одредени температури, сепак, максимално дозволениот наклон за која било компонента треба да важи без разлика дали компонентата се загрева или лади.Најчесто се предлага стапка на ладење од 4°C/s.Тоа е параметар што треба да се земе предвид кога се анализираат резултатите од процесот.
Терминот „повторно проток“ се користи за да се однесува на температурата над која сигурно ќе се стопи цврста маса на легура за лемење (наспроти само омекнување).Ако се излади под оваа температура, лемењето нема да тече.Загреан над него уште еднаш, лемењето повторно ќе тече - оттука „повторно тече“.
Современите техники за склопување на колото што користат лемење со повторно проток не мора да дозволуваат лемењето да тече повеќе од еднаш.Тие гарантираат дека гранулираниот лемење содржан во пастата за лемење ја надминува температурата на преточување на вклученото лемење.
Термичко профилирање
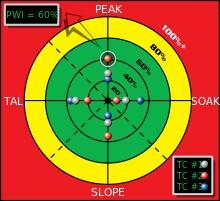
Графички приказ на Индексот на Прозорецот на Процесот за термички профил.
Во индустријата за производство на електроника, статистичка мерка, позната како Индекс на прозорски прозорец (PWI) се користи за квантифицирање на робусноста на термичкиот процес.PWI помага да се измери колку добро еден процес „се вклопува“ во ограничување на процесот дефинирано од корисникот познато како Ограничување на спецификацијата. Секој термички профил е рангиран според тоа како „се вклопува“ во прозорец на процес (спецификација или ограничување на толеранција).
Центарот на процесниот прозорец е дефиниран како нула, а крајниот раб на прозорецот на процесот како 99%. PWI поголем или еднаков на 100% покажува дека профилот не го обработува производот во рамките на спецификацијата.PWI од 99% покажува дека профилот го обработува производот во рамките на спецификацијата, но работи на работ на прозорецот на процесот.PWI од 60% покажува дека профилот користи 60% од спецификацијата на процесот.Со користење на вредностите на PWI, производителите можат да одредат колку од процесниот прозорец користи одреден термички профил.Пониска вредност на PWI укажува на поцврст профил.
За максимална ефикасност, се пресметуваат посебни вредности на PWI за процесите на врв, наклон, преточување и натопување на термички профил.За да се избегне можноста термички шок да влијае на излезот, мора да се одреди и израмни најстрмниот наклон во термичкиот профил.Производителите користат сопствен софтвер за прецизно одредување и намалување на стрмнината на наклонот.Покрај тоа, софтверот исто така автоматски ги рекалибрира вредностите на PWI за процесите на врв, наклон, преточување и натопување.Со поставување на вредностите на PWI, инженерите можат да се погрижат работата за лемење со повторно проток да не се прегрее или лади премногу брзо.
Време на објавување: Мар-01-2022 година