ഒന്നോ അതിലധികമോ ഇലക്ട്രിക്കൽ ഘടകങ്ങൾ അവയുടെ കോൺടാക്റ്റ് പാഡുകളിലേക്ക് താൽക്കാലികമായി ഘടിപ്പിക്കാൻ സോൾഡർ പേസ്റ്റ് (പൊടി സോൾഡറിൻ്റെയും ഫ്ലക്സിൻ്റെയും സ്റ്റിക്കി മിശ്രിതം) ഉപയോഗിക്കുന്ന ഒരു പ്രക്രിയയാണ് റിഫ്ലോ സോൾഡറിംഗ്, അതിനുശേഷം മുഴുവൻ അസംബ്ലിയും നിയന്ത്രിത ചൂടിന് വിധേയമാകുന്നു, ഇത് സോൾഡറിനെ ഉരുകുന്നു. , ജോയിൻ്റ് ശാശ്വതമായി ബന്ധിപ്പിക്കുന്നു.ഒരു റിഫ്ലോ ഓവനിലൂടെയോ ഇൻഫ്രാറെഡ് വിളക്കിന് കീഴിലൂടെയോ അല്ലെങ്കിൽ ഹോട്ട് എയർ പെൻസിൽ ഉപയോഗിച്ച് വ്യക്തിഗത സന്ധികൾ സോൾഡറിംഗ് വഴിയോ അസംബ്ലി കടന്നുപോകുന്നതിലൂടെ ചൂടാക്കൽ പൂർത്തിയാക്കാം.
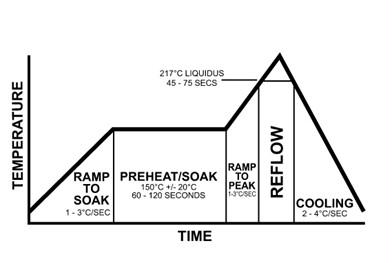
സർക്യൂട്ട് ബോർഡിൽ ഉപരിതല മൌണ്ട് ഘടകങ്ങൾ ഘടിപ്പിക്കുന്നതിനുള്ള ഏറ്റവും സാധാരണമായ രീതിയാണ് റിഫ്ലോ സോൾഡറിംഗ്, എന്നിരുന്നാലും സോൾഡർ പേസ്റ്റ് ഉപയോഗിച്ച് ദ്വാരങ്ങൾ നിറയ്ക്കുകയും പേസ്റ്റിലൂടെ ഘടക ലീഡുകൾ തിരുകുകയും ചെയ്തുകൊണ്ട് ത്രൂ-ഹോൾ ഘടകങ്ങൾക്ക് ഇത് ഉപയോഗിക്കാം.വേവ് സോൾഡറിംഗ് ലളിതവും വിലകുറഞ്ഞതും ആയതിനാൽ, ശുദ്ധമായ ത്രൂ-ഹോൾ ബോർഡുകളിൽ റിഫ്ലോ സാധാരണയായി ഉപയോഗിക്കാറില്ല.SMT, THT ഘടകങ്ങൾ അടങ്ങിയ ബോർഡുകളിൽ ഉപയോഗിക്കുമ്പോൾ, ത്രൂ-ഹോൾ റിഫ്ലോ അസംബ്ലി പ്രക്രിയയിൽ നിന്ന് വേവ് സോൾഡറിംഗ് സ്റ്റെപ്പ് ഇല്ലാതാക്കാൻ അനുവദിക്കുന്നു, ഇത് അസംബ്ലി ചെലവ് കുറയ്ക്കാൻ സാധ്യതയുണ്ട്.
വൈദ്യുത ഘടകങ്ങളെ അമിതമായി ചൂടാക്കാതെയും കേടുപാടുകൾ വരുത്താതെയും സോൾഡർ ഉരുകുകയും അടുത്തുള്ള പ്രതലങ്ങളെ ചൂടാക്കുകയും ചെയ്യുക എന്നതാണ് റിഫ്ലോ പ്രക്രിയയുടെ ലക്ഷ്യം.പരമ്പരാഗത റിഫ്ലോ സോൾഡറിംഗ് പ്രക്രിയയിൽ, സാധാരണയായി "സോണുകൾ" എന്ന് വിളിക്കപ്പെടുന്ന നാല് ഘട്ടങ്ങളുണ്ട്, ഓരോന്നിനും ഒരു പ്രത്യേക തെർമൽ പ്രൊഫൈൽ ഉണ്ട്: പ്രീഹീറ്റ്, തെർമൽ സോക്ക് (പലപ്പോഴും കുതിർക്കാൻ വേണ്ടി ചുരുക്കി), റീഫ്ലോ, കൂളിംഗ്.
പ്രീഹീറ്റ് സോൺ
പ്രിൻ്റഡ് സർക്യൂട്ട് ബോർഡിലെ താപനില എത്ര വേഗത്തിൽ മാറുന്നുവെന്ന് അളക്കുന്ന താപനില/സമയ ബന്ധമാണ് പരമാവധി ചരിവ്.പ്രീഹീറ്റ് സോൺ പലപ്പോഴും സോണുകളിൽ ഏറ്റവും ദൈർഘ്യമേറിയതും പലപ്പോഴും റാംപ് നിരക്ക് സ്ഥാപിക്കുന്നതുമാണ്.റാമ്പ്-അപ്പ് നിരക്ക് സാധാരണയായി സെക്കൻഡിൽ 1.0 °C നും 3.0 °C നും ഇടയിലാണ്, പലപ്പോഴും സെക്കൻഡിൽ 2.0 °C നും 3.0 °C (4 °F മുതൽ 5 °F വരെ) വരെ കുറയുന്നു.നിരക്ക് പരമാവധി ചരിവ് കവിഞ്ഞാൽ, തെർമൽ ഷോക്ക് അല്ലെങ്കിൽ ക്രാക്കിംഗിൽ നിന്നുള്ള ഘടകങ്ങൾക്ക് കേടുപാടുകൾ സംഭവിക്കാം.
സോൾഡർ പേസ്റ്റിന് സ്പാറ്ററിംഗ് ഇഫക്റ്റും ഉണ്ടാകും.പേസ്റ്റിലെ ലായകം ബാഷ്പീകരിക്കപ്പെടാൻ തുടങ്ങുന്ന സ്ഥലമാണ് പ്രീഹീറ്റ് വിഭാഗം, വർധന നിരക്ക് (അല്ലെങ്കിൽ താപനില നില) വളരെ കുറവാണെങ്കിൽ, ഫ്ലക്സ് അസ്ഥിരങ്ങളുടെ ബാഷ്പീകരണം അപൂർണ്ണമാണ്.
താപ സോക്ക് സോൺ
രണ്ടാമത്തെ വിഭാഗമായ തെർമൽ സോക്ക്, സോൾഡർ പേസ്റ്റ് അസ്ഥിരതകൾ നീക്കം ചെയ്യുന്നതിനും ഫ്ലക്സുകൾ സജീവമാക്കുന്നതിനുമുള്ള 60 മുതൽ 120 സെക്കൻഡ് വരെ എക്സ്പോഷർ ആണ് (ഫ്ലക്സ് കാണുക), അവിടെ ഫ്ലക്സ് ഘടകങ്ങൾ ഘടക ലീഡുകളിലും പാഡുകളിലും ഓക്സിഡെഡക്ഷൻ ആരംഭിക്കുന്നു.വളരെ ഉയർന്ന താപനില സോൾഡർ സ്പാറ്ററിംഗിലേക്കോ ബോളിംഗിലേക്കോ പേസ്റ്റിൻ്റെ ഓക്സിഡേഷനിലേക്കും അറ്റാച്ച്മെൻ്റ് പാഡുകളിലേക്കും ഘടകഭാഗങ്ങൾ അവസാനിപ്പിക്കുന്നതിലേക്കും നയിച്ചേക്കാം.
അതുപോലെ, താപനില വളരെ കുറവാണെങ്കിൽ ഫ്ലക്സുകൾ പൂർണ്ണമായും സജീവമാകണമെന്നില്ല.സോക്ക് സോണിൻ്റെ അവസാനത്തിൽ, റിഫ്ലോ സോണിന് തൊട്ടുമുമ്പ് മുഴുവൻ അസംബ്ലിയുടെയും താപ സന്തുലിതാവസ്ഥ ആവശ്യമാണ്.വ്യത്യസ്ത വലുപ്പത്തിലുള്ള ഘടകങ്ങൾക്കിടയിൽ ഏതെങ്കിലും ഡെൽറ്റ ടി കുറയ്ക്കാൻ അല്ലെങ്കിൽ പിസിബി അസംബ്ലി വളരെ വലുതാണെങ്കിൽ സോക്ക് പ്രൊഫൈൽ നിർദ്ദേശിക്കപ്പെടുന്നു.ഏരിയ അറേ ടൈപ്പ് പാക്കേജുകളിലെ ശൂന്യത കുറയ്ക്കാൻ സോക്ക് പ്രൊഫൈലും ശുപാർശ ചെയ്യുന്നു.
റിഫ്ലോ സോൺ
മൂന്നാമത്തെ വിഭാഗം, റിഫ്ലോ സോൺ, "റിഫ്ലോയ്ക്ക് മുകളിലുള്ള സമയം" അല്ലെങ്കിൽ "ലിക്വിഡസിന് മുകളിലുള്ള സമയം" (TAL) എന്നും പരാമർശിക്കപ്പെടുന്നു, ഇത് പരമാവധി താപനിലയിൽ എത്തുന്ന പ്രക്രിയയുടെ ഭാഗമാണ്.ഒരു പ്രധാന പരിഗണന പീക്ക് താപനിലയാണ്, ഇത് മുഴുവൻ പ്രക്രിയയുടെയും പരമാവധി അനുവദനീയമായ താപനിലയാണ്.ലിക്വിഡസിന് മുകളിലുള്ള 20-40 ഡിഗ്രി സെൽഷ്യസാണ് ഒരു സാധാരണ പീക്ക് താപനില. ഈ പരിധി നിർണ്ണയിക്കുന്നത് ഉയർന്ന താപനിലയ്ക്ക് ഏറ്റവും കുറഞ്ഞ സഹിഷ്ണുത ഉള്ള അസംബ്ലിയിലെ ഘടകമാണ് (താപ നാശത്തിന് ഏറ്റവും സാധ്യതയുള്ള ഘടകം).പ്രക്രിയയ്ക്കായി പരമാവധി താപനിലയിൽ എത്താൻ ഏറ്റവും ദുർബലമായ ഘടകം നിലനിർത്താൻ കഴിയുന്ന പരമാവധി താപനിലയിൽ നിന്ന് 5 °C കുറയ്ക്കുക എന്നതാണ് ഒരു സ്റ്റാൻഡേർഡ് മാർഗ്ഗനിർദ്ദേശം.ഈ പരിധി കവിയാതിരിക്കാൻ പ്രക്രിയയുടെ താപനില നിരീക്ഷിക്കേണ്ടത് പ്രധാനമാണ്.
കൂടാതെ, ഉയർന്ന ഊഷ്മാവ് (260 ഡിഗ്രി സെൽഷ്യസിനു മുകളിൽ) SMT ഘടകങ്ങളുടെ ആന്തരിക ഡൈസിന് കേടുപാടുകൾ വരുത്തുകയും ഇൻ്റർമെറ്റാലിക് വളർച്ചയെ പ്രോത്സാഹിപ്പിക്കുകയും ചെയ്യും.നേരെമറിച്ച്, വേണ്ടത്ര ചൂടില്ലാത്ത ഒരു താപനില പേസ്റ്റ് വേണ്ടത്ര വീണ്ടും ഒഴുകുന്നതിൽ നിന്ന് തടഞ്ഞേക്കാം.
ലിക്വിഡസിന് മുകളിലുള്ള സമയം (TAL), അല്ലെങ്കിൽ റിഫ്ലോയ്ക്ക് മുകളിലുള്ള സമയം, സോൾഡർ എത്രത്തോളം ദ്രാവകമാണെന്ന് അളക്കുന്നു.മെറ്റലർജിക്കൽ ബോണ്ടിംഗ് പൂർത്തീകരിക്കുന്നതിന് ഫ്ളക്സ് ലോഹങ്ങളുടെ സന്ധിയിൽ ഉപരിതല പിരിമുറുക്കം കുറയ്ക്കുന്നു, ഇത് വ്യക്തിഗത സോൾഡർ പൗഡർ ഗോളങ്ങളെ സംയോജിപ്പിക്കാൻ അനുവദിക്കുന്നു.പ്രൊഫൈൽ സമയം നിർമ്മാതാവിൻ്റെ സ്പെസിഫിക്കേഷനേക്കാൾ കൂടുതലാണെങ്കിൽ, ഫലം അകാല ഫ്ലക്സ് ആക്റ്റിവേഷൻ അല്ലെങ്കിൽ ഉപഭോഗം ആയിരിക്കാം, സോൾഡർ ജോയിൻ്റ് രൂപപ്പെടുന്നതിന് മുമ്പ് പേസ്റ്റ് ഫലപ്രദമായി "ഉണക്കുക".അപര്യാപ്തമായ സമയ/താപനില ബന്ധം ഫ്ളക്സിൻ്റെ ക്ലീനിംഗ് പ്രവർത്തനത്തിൽ കുറവുണ്ടാക്കുന്നു, ഇത് മോശം നനവ്, ലായകത്തിൻ്റെയും ഫ്ളക്സിൻ്റെയും അപര്യാപ്തമായ നീക്കം, ഒരുപക്ഷേ വികലമായ സോൾഡർ സന്ധികൾ എന്നിവയ്ക്ക് കാരണമാകുന്നു.
വിദഗ്ദ്ധർ സാധാരണയായി സാധ്യമായ ഏറ്റവും കുറഞ്ഞ TAL ശുപാർശ ചെയ്യുന്നു, എന്നിരുന്നാലും, മിക്ക പേസ്റ്റുകളും ഏറ്റവും കുറഞ്ഞ TAL 30 സെക്കൻഡ് വ്യക്തമാക്കുന്നു, എന്നിരുന്നാലും ആ നിർദ്ദിഷ്ട സമയത്തിന് വ്യക്തമായ കാരണമൊന്നുമില്ല.പ്രൊഫൈലിംഗ് സമയത്ത് അളക്കാത്ത സ്ഥലങ്ങൾ പിസിബിയിൽ ഉണ്ടെന്നതാണ് ഒരു സാധ്യത, അതിനാൽ, അനുവദനീയമായ ഏറ്റവും കുറഞ്ഞ സമയം 30 സെക്കൻഡായി സജ്ജീകരിക്കുന്നത് അളക്കാത്ത പ്രദേശം വീണ്ടും ഒഴുകാതിരിക്കാനുള്ള സാധ്യത കുറയ്ക്കുന്നു.ഉയർന്ന കുറഞ്ഞ റിഫ്ലോ സമയം അടുപ്പിലെ താപനില വ്യതിയാനങ്ങൾക്കെതിരെ സുരക്ഷിതത്വത്തിൻ്റെ മാർജിൻ നൽകുന്നു.നനവ് സമയം ലിക്വിഡസിന് മുകളിൽ 60 സെക്കൻഡിൽ താഴെയായിരിക്കും.ലിക്വിഡസിന് മുകളിലുള്ള അധിക സമയം അമിതമായ ഇൻ്റർമെറ്റാലിക് വളർച്ചയ്ക്ക് കാരണമായേക്കാം, ഇത് സംയുക്ത പൊട്ടലിലേക്ക് നയിച്ചേക്കാം.ലിക്വിഡസിനേക്കാൾ കൂടുതൽ സമയങ്ങളിൽ ബോർഡിനും ഘടകങ്ങൾക്കും കേടുപാടുകൾ സംഭവിച്ചേക്കാം, കൂടാതെ മിക്ക ഘടകങ്ങൾക്കും ഒരു നിശ്ചിത പരമാവധി താപനിലയിൽ എത്ര സമയം തുറന്നുകാട്ടപ്പെടാം എന്നതിന് കൃത്യമായി നിർവചിക്കപ്പെട്ട സമയ പരിധിയുണ്ട്.
ലിക്വിഡസിന് മുകളിലുള്ള വളരെ കുറച്ച് സമയം ലായകങ്ങളെയും ഫ്ളക്സിനെയും കുടുക്കി, തണുത്തതോ മങ്ങിയതോ ആയ സന്ധികൾക്കും സോൾഡർ ശൂന്യതയ്ക്കും സാധ്യത സൃഷ്ടിക്കും.
തണുപ്പിക്കൽ മേഖല
പ്രോസസ്സ് ചെയ്ത ബോർഡ് ക്രമേണ തണുപ്പിക്കാനും സോൾഡർ സന്ധികൾ ദൃഢമാക്കാനും അവസാന മേഖല ഒരു തണുപ്പിക്കൽ മേഖലയാണ്.ശരിയായ തണുപ്പിക്കൽ അധിക ഇൻ്റർമെറ്റാലിക് രൂപീകരണത്തെ തടയുന്നു അല്ലെങ്കിൽ ഘടകങ്ങൾക്ക് താപ ഷോക്ക് നൽകുന്നു.കൂളിംഗ് സോണിലെ സാധാരണ താപനില 30-100 °C (86-212 °F) വരെയാണ്.മെക്കാനിക്കലായി മികച്ച ഒരു ധാന്യ ഘടന സൃഷ്ടിക്കാൻ ഫാസ്റ്റ് കൂളിംഗ് നിരക്ക് തിരഞ്ഞെടുത്തു.
[1] പരമാവധി റാമ്പ്-അപ്പ് നിരക്കിൽ നിന്ന് വ്യത്യസ്തമായി, റാംപ്-ഡൗൺ നിരക്ക് പലപ്പോഴും അവഗണിക്കപ്പെടുന്നു.റാംപ് നിരക്ക് ചില പ്രത്യേക ഊഷ്മാവുകൾക്ക് മുകളിൽ നിർണായകമല്ലായിരിക്കാം, എന്നിരുന്നാലും, ഘടകം ചൂടാകുകയോ തണുപ്പിക്കുകയോ ചെയ്യുകയാണെങ്കിൽ ഏത് ഘടകത്തിനും അനുവദനീയമായ പരമാവധി ചരിവ് ബാധകമാണ്.4°C/s തണുപ്പിക്കൽ നിരക്ക് സാധാരണയായി നിർദ്ദേശിക്കപ്പെടുന്നു.പ്രക്രിയയുടെ ഫലങ്ങൾ വിശകലനം ചെയ്യുമ്പോൾ പരിഗണിക്കേണ്ട ഒരു പരാമീറ്ററാണിത്.
സോൾഡർ അലോയ്യുടെ ഖര പിണ്ഡം ഉരുകുമെന്ന് ഉറപ്പായ താപനിലയെ സൂചിപ്പിക്കാൻ "റിഫ്ലോ" എന്ന പദം ഉപയോഗിക്കുന്നു (വെറും മൃദുവാക്കുന്നതിന് വിപരീതമായി).ഈ താപനിലയിൽ താഴെ തണുപ്പിച്ചാൽ, സോൾഡർ ഒഴുകുകയില്ല.അതിനു മുകളിൽ ഒരിക്കൽ കൂടി ചൂടാക്കിയാൽ, സോൾഡർ വീണ്ടും ഒഴുകും - അതിനാൽ "വീണ്ടും ഒഴുകുക".
റിഫ്ലോ സോൾഡറിംഗ് ഉപയോഗിക്കുന്ന ആധുനിക സർക്യൂട്ട് അസംബ്ലി ടെക്നിക്കുകൾ സോൾഡറിനെ ഒന്നിലധികം തവണ ഒഴുകാൻ അനുവദിക്കണമെന്നില്ല.സോൾഡർ പേസ്റ്റിൽ അടങ്ങിയിരിക്കുന്ന ഗ്രാനേറ്റഡ് സോൾഡർ ഉൾപ്പെട്ട സോൾഡറിൻ്റെ റിഫ്ലോ താപനിലയെ മറികടക്കുമെന്ന് അവർ ഉറപ്പ് നൽകുന്നു.
തെർമൽ പ്രൊഫൈലിംഗ്
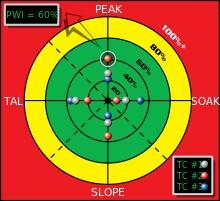
ഒരു തെർമൽ പ്രൊഫൈലിനുള്ള പ്രോസസ് വിൻഡോ സൂചികയുടെ ഗ്രാഫിക്കൽ പ്രാതിനിധ്യം.
ഇലക്ട്രോണിക്സ് നിർമ്മാണ വ്യവസായത്തിൽ, ഒരു താപ പ്രക്രിയയുടെ ദൃഢത അളക്കാൻ പ്രോസസ് വിൻഡോ ഇൻഡക്സ് (PWI) എന്നറിയപ്പെടുന്ന ഒരു സ്റ്റാറ്റിസ്റ്റിക്കൽ അളവ് ഉപയോഗിക്കുന്നു.സ്പെസിഫിക്കേഷൻ ലിമിറ്റ് എന്നറിയപ്പെടുന്ന ഉപയോക്തൃ-നിർവചിച്ച പ്രോസസ്സ് പരിധിയിലേക്ക് ഒരു പ്രോസസ്സ് എത്രത്തോളം "യോജിക്കുന്നുവെന്ന്" അളക്കാൻ PWI സഹായിക്കുന്നു. ഓരോ തെർമൽ പ്രൊഫൈലും ഒരു പ്രോസസ്സ് വിൻഡോയിൽ (സ്പെസിഫിക്കേഷൻ അല്ലെങ്കിൽ ടോളറൻസ് പരിധി) അത് എങ്ങനെ യോജിക്കുന്നു എന്നതിനെ അടിസ്ഥാനമാക്കിയാണ് റാങ്ക് ചെയ്യുന്നത്.
പ്രോസസ്സ് വിൻഡോയുടെ മധ്യഭാഗം പൂജ്യമായും, പ്രോസസ്സ് വിൻഡോയുടെ അങ്ങേയറ്റത്തെ അഗ്രം 99% ആയും നിർവചിച്ചിരിക്കുന്നു. 100%-നേക്കാൾ വലുതോ തുല്യമോ ആയ PWI, പ്രൊഫൈൽ സ്പെസിഫിക്കേഷനിൽ ഉൽപ്പന്നം പ്രോസസ്സ് ചെയ്യുന്നില്ലെന്ന് സൂചിപ്പിക്കുന്നു.99% PWI സൂചിപ്പിക്കുന്നത് പ്രൊഫൈൽ സ്പെസിഫിക്കേഷനിൽ ഉൽപ്പന്നം പ്രോസസ്സ് ചെയ്യുന്നു, എന്നാൽ പ്രോസസ്സ് വിൻഡോയുടെ അരികിൽ പ്രവർത്തിക്കുന്നു.60% PWI എന്നത് ഒരു പ്രൊഫൈൽ പ്രോസസ്സ് സ്പെസിഫിക്കേഷൻ്റെ 60% ഉപയോഗിക്കുന്നതായി സൂചിപ്പിക്കുന്നു.PWI മൂല്യങ്ങൾ ഉപയോഗിക്കുന്നതിലൂടെ, നിർമ്മാതാക്കൾക്ക് ഒരു പ്രത്യേക തെർമൽ പ്രൊഫൈൽ എത്ര പ്രോസസ്സ് വിൻഡോ ഉപയോഗിക്കുന്നു എന്ന് നിർണ്ണയിക്കാനാകും.കുറഞ്ഞ PWI മൂല്യം കൂടുതൽ ശക്തമായ പ്രൊഫൈലിനെ സൂചിപ്പിക്കുന്നു.
പരമാവധി കാര്യക്ഷമതയ്ക്കായി, ഒരു തെർമൽ പ്രൊഫൈലിൻ്റെ പീക്ക്, ചരിവ്, റിഫ്ലോ, സോക്ക് പ്രോസസ്സുകൾ എന്നിവയ്ക്കായി പ്രത്യേക PWI മൂല്യങ്ങൾ കണക്കാക്കുന്നു.ഔട്ട്പുട്ടിനെ ബാധിക്കുന്ന തെർമൽ ഷോക്ക് സാധ്യത ഒഴിവാക്കാൻ, തെർമൽ പ്രൊഫൈലിലെ കുത്തനെയുള്ള ചരിവ് നിർണ്ണയിക്കുകയും നിരപ്പാക്കുകയും വേണം.ചരിവിൻ്റെ കുത്തനെ കൃത്യമായി നിർണ്ണയിക്കാനും കുറയ്ക്കാനും നിർമ്മാതാക്കൾ ഇഷ്ടാനുസൃതമായി നിർമ്മിച്ച സോഫ്റ്റ്വെയർ ഉപയോഗിക്കുന്നു.കൂടാതെ, പീക്ക്, ചരിവ്, റിഫ്ലോ, സോക്ക് പ്രോസസുകൾ എന്നിവയ്ക്കായുള്ള PWI മൂല്യങ്ങൾ സോഫ്റ്റ്വെയർ സ്വയമേവ പുനഃക്രമീകരിക്കുന്നു.പിഡബ്ല്യുഐ മൂല്യങ്ങൾ സജ്ജീകരിക്കുന്നതിലൂടെ, റിഫ്ലോ സോൾഡറിംഗ് ജോലി വളരെ വേഗത്തിൽ ചൂടാകുകയോ തണുപ്പിക്കുകയോ ചെയ്യുന്നില്ലെന്ന് എഞ്ചിനീയർമാർക്ക് ഉറപ്പാക്കാൻ കഴിയും.
പോസ്റ്റ് സമയം: മാർച്ച്-01-2022