Reflow-solderen is een proces waarbij een soldeerpasta (een kleverig mengsel van poedervormig soldeer en vloeimiddel) wordt gebruikt om een of meerdere elektrische componenten tijdelijk aan hun contactvlakken te bevestigen, waarna het geheel wordt onderworpen aan gecontroleerde hitte, waardoor het soldeer smelt. , die de verbinding permanent verbindt.Het verwarmen kan worden bewerkstelligd door het geheel door een reflow-oven of onder een infraroodlamp te leiden, of door afzonderlijke verbindingen met een heteluchtpotlood te solderen.
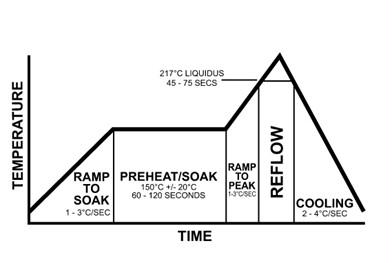
Reflow-solderen is de meest gebruikelijke methode om componenten voor opbouwmontage op een printplaat te bevestigen, hoewel het ook kan worden gebruikt voor componenten met doorlopende gaten door de gaten te vullen met soldeerpasta en de componentdraden door de pasta te steken.Omdat golfsolderen eenvoudiger en goedkoper kan zijn, wordt reflow over het algemeen niet gebruikt op pure through-hole-platen.Bij gebruik op borden met een mix van SMT- en THT-componenten zorgt de through-hole reflow ervoor dat de golfsoldeerstap uit het assemblageproces wordt geëlimineerd, waardoor de montagekosten mogelijk worden verlaagd.
Het doel van het reflow-proces is om het soldeer te smelten en de aangrenzende oppervlakken te verwarmen, zonder de elektrische componenten oververhit te raken en te beschadigen.Bij het conventionele reflow-soldeerproces zijn er gewoonlijk vier fasen, "zones" genoemd, die elk een duidelijk thermisch profiel hebben: voorverwarmen, thermisch weken (vaak afgekort tot gewoon weken), reflow en afkoelen.
Verwarm zone voor
Maximale helling is een temperatuur/tijd-relatie die meet hoe snel de temperatuur op de printplaat verandert.De voorverwarmingszone is vaak de langste van de zones en bepaalt vaak de stijgingssnelheid.De oploopsnelheid ligt gewoonlijk ergens tussen 1,0 °C en 3,0 °C per seconde, vaak tussen 2,0 °C en 3,0 °C (4 °F tot 5 °F) per seconde.Als de snelheid de maximale helling overschrijdt, kan schade aan componenten door thermische schokken of barsten optreden.
Soldeerpasta kan ook een spateffect hebben.In het voorverwarmgedeelte begint het oplosmiddel in de pasta te verdampen, en als de stijgsnelheid (of het temperatuurniveau) te laag is, is de verdamping van de vluchtige stoffen onvolledig.
Thermische doorweekzone
Het tweede gedeelte, thermische weken, is doorgaans een blootstelling van 60 tot 120 seconden voor het verwijderen van vluchtige soldeerpasta's en activering van de fluxen (zie flux), waar de fluxcomponenten beginnen met oxidereductie op componentleidingen en -pads.Een te hoge temperatuur kan leiden tot soldeerspatten of kogelvorming, evenals tot oxidatie van de pasta, de bevestigingspads en de aansluitingen van de componenten.
Op dezelfde manier kunnen fluxen niet volledig worden geactiveerd als de temperatuur te laag is.Aan het einde van de doorweekzone is een thermisch evenwicht van het gehele samenstel gewenst net vóór de reflowzone.Er wordt een doorweekprofiel aanbevolen om eventuele delta T tussen componenten van verschillende groottes te verkleinen of als de PCB-assemblage erg groot is.Een doorweekprofiel wordt ook aanbevolen om de leegte in pakketten van het type area array te verminderen.
Reflow-zone
Het derde deel, de reflowzone, wordt ook wel de “time Above Reflow” of “Time Above Liquidus” (TAL) genoemd en is het deel van het proces waar de maximale temperatuur wordt bereikt.Een belangrijke overweging is de piektemperatuur, de maximaal toegestane temperatuur van het hele proces.Een gebruikelijke piektemperatuur is 20–40 °C boven liquidus. Deze limiet wordt bepaald door het onderdeel op het samenstel met de laagste tolerantie voor hoge temperaturen (het onderdeel dat het meest gevoelig is voor thermische schade).Een standaardrichtlijn is om 5 °C af te trekken van de maximale temperatuur die het meest kwetsbare onderdeel kan verdragen om zo tot de maximale procestemperatuur te komen.Het is belangrijk om de procestemperatuur te bewaken om te voorkomen dat deze deze limiet overschrijdt.
Bovendien kunnen hoge temperaturen (boven 260 °C) schade aan de interne matrijzen van SMT-componenten veroorzaken en intermetallische groei bevorderen.Omgekeerd kan een temperatuur die niet hoog genoeg is ervoor zorgen dat de pasta niet voldoende terugstroomt.
Tijd boven liquidus (TAL), of tijd boven reflow, meet hoe lang het soldeer vloeibaar is.De flux vermindert de oppervlaktespanning op de verbindingspunten van de metalen om metallurgische binding te bewerkstelligen, waardoor de individuele soldeerpoederbollen kunnen worden gecombineerd.Als de profieltijd de specificaties van de fabrikant overschrijdt, kan het resultaat voortijdige fluxactivering of -verbruik zijn, waardoor de pasta effectief wordt "gedroogd" voordat de soldeerverbinding wordt gevormd.Een onvoldoende tijd/temperatuur-relatie veroorzaakt een afname van de reinigende werking van het vloeimiddel, wat resulteert in een slechte bevochtiging, onvoldoende verwijdering van het oplosmiddel en het vloeimiddel, en mogelijk defecte soldeerverbindingen.
Deskundigen raden doorgaans de kortst mogelijke TAL aan, maar de meeste pasta's specificeren een minimale TAL van 30 seconden, hoewel er geen duidelijke reden lijkt te zijn voor die specifieke tijd.Eén mogelijkheid is dat er plaatsen op de printplaat zijn die niet worden gemeten tijdens het profileren, en daarom verkleint het instellen van de minimaal toegestane tijd op 30 seconden de kans dat een niet-gemeten gebied niet opnieuw stroomt.Een hoge minimale terugvloeitijd biedt ook een veiligheidsmarge tegen veranderingen in de oventemperatuur.De bevochtigingstijd blijft idealiter onder de 60 seconden boven de liquidus.Extra tijd boven de liquidus kan overmatige intermetallische groei veroorzaken, wat kan leiden tot broosheid van de gewrichten.Het bord en de componenten kunnen ook langdurig beschadigd raken door liquidus, en de meeste componenten hebben een goed gedefinieerde tijdslimiet voor hoe lang ze mogen worden blootgesteld aan temperaturen boven een bepaald maximum.
Te weinig tijd boven liquidus kan oplosmiddelen en vloeimiddel vasthouden en de kans op koude of doffe verbindingen en soldeerholtes creëren.
Koelzone
De laatste zone is een koelzone om de bewerkte plaat geleidelijk af te koelen en de soldeerverbindingen te laten stollen.Een goede koeling voorkomt overmatige intermetallische vorming of thermische schokken van de componenten.Typische temperaturen in de koelzone variëren van 30–100 ° C (86–212 ° F).Er is gekozen voor een snelle afkoeling om een fijne korrelstructuur te creëren die mechanisch het meest verantwoord is.
[1] In tegenstelling tot de maximale oploopsnelheid wordt de uitloopsnelheid vaak genegeerd.Het kan zijn dat de stijgingssnelheid boven bepaalde temperaturen minder kritisch is, maar de maximaal toegestane helling voor elk onderdeel moet gelden, ongeacht of het onderdeel opwarmt of afkoelt.Normaal gesproken wordt een koelsnelheid van 4°C/s aanbevolen.Het is een parameter waarmee rekening moet worden gehouden bij het analyseren van procesresultaten.
De term "reflow" wordt gebruikt om te verwijzen naar de temperatuur waarboven een vaste massa soldeerlegering zeker zal smelten (in plaats van alleen maar zachter te worden).Als het onder deze temperatuur wordt afgekoeld, zal het soldeer niet vloeien.Als het soldeer er nogmaals boven wordt opgewarmd, zal het weer gaan vloeien - vandaar "re-flow".
Moderne circuitassemblagetechnieken waarbij reflow-solderen wordt gebruikt, zorgen er niet noodzakelijkerwijs voor dat het soldeer meer dan één keer kan vloeien.Ze garanderen dat het gegranuleerde soldeer in de soldeerpasta de reflow-temperatuur van het betreffende soldeer overtreft.
Thermische profilering
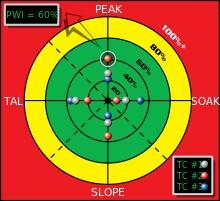
Een grafische weergave van de Process Window Index voor een thermisch profiel.
In de elektronica-industrie wordt een statistische maatstaf, bekend als de Process Window Index (PWI), gebruikt om de robuustheid van een thermisch proces te kwantificeren.PWI helpt meten hoe goed een proces "past" binnen een door de gebruiker gedefinieerde proceslimiet die bekend staat als de Specificatielimiet. Elk thermisch profiel wordt gerangschikt op basis van hoe het "past" in een procesvenster (de specificatie- of tolerantielimiet).
Het midden van het procesvenster wordt gedefinieerd als nul en de uiterste rand van het procesvenster als 99%. Een PWI groter dan of gelijk aan 100% geeft aan dat het profiel het product niet binnen de specificatie verwerkt.Een PWI van 99% geeft aan dat het profiel het product binnen de specificatie verwerkt, maar aan de rand van het procesvenster loopt.Een PWI van 60% geeft aan dat een profiel 60% van de processpecificatie gebruikt.Door PWI-waarden te gebruiken, kunnen fabrikanten bepalen hoeveel van het procesvenster een bepaald thermisch profiel gebruikt.Een lagere PWI-waarde duidt op een robuuster profiel.
Voor maximale efficiëntie worden afzonderlijke PWI-waarden berekend voor piek-, helling-, reflow- en soak-processen van een thermisch profiel.Om de mogelijkheid van een thermische schok die de output beïnvloedt te voorkomen, moet de steilste helling in het thermische profiel worden bepaald en genivelleerd.Fabrikanten gebruiken op maat gemaakte software om de steilheid van de helling nauwkeurig te bepalen en te verminderen.Bovendien herkalibreert de software automatisch de PWI-waarden voor de piek-, helling-, reflow- en soak-processen.Door PWI-waarden in te stellen, kunnen ingenieurs ervoor zorgen dat het reflow-soldeerwerk niet oververhit raakt of te snel afkoelt.
Posttijd: 01 maart 2022