Lutowanie rozpływowe to proces, w którym pasta lutownicza (lepka mieszanina sproszkowanego lutowia i topnika) służy do tymczasowego mocowania jednego lub kilku elementów elektrycznych do ich pól stykowych, po czym cały zespół poddawany jest kontrolowanemu działaniu ciepła, które topi lut , trwale łącząc złącze.Ogrzewanie można przeprowadzić przepuszczając zespół przez piec rozpływowy lub pod lampą podczerwieni lub lutując poszczególne złącza za pomocą ołówka na gorące powietrze.
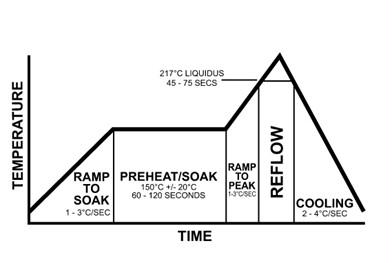
Lutowanie rozpływowe to najpopularniejsza metoda mocowania elementów do montażu powierzchniowego na płytce drukowanej, chociaż można go również stosować w przypadku elementów z otworami przelotowymi, wypełniając otwory pastą lutowniczą i wkładając przewody komponentów przez pastę.Ponieważ lutowanie na fali może być prostsze i tańsze, rozpływ nie jest zwykle stosowany w przypadku płyt z otworami przelotowymi.W przypadku stosowania na płytkach zawierających mieszankę komponentów SMT i THT, przepływ przez otwór umożliwia wyeliminowanie etapu lutowania na fali z procesu montażu, potencjalnie zmniejszając koszty montażu.
Celem procesu rozpływu jest stopienie lutu i podgrzanie przylegających powierzchni, bez przegrzania i uszkodzenia elementów elektrycznych.W konwencjonalnym procesie lutowania rozpływowego istnieją zwykle cztery etapy, zwane „strefami”, z których każdy ma odrębny profil termiczny: podgrzewanie wstępne, wygrzewanie termiczne (często w skrócie nazywane po prostu namacaniem), rozpływ i chłodzenie.
Strefa rozgrzania
Maksymalne nachylenie to zależność temperatura/czas, która mierzy, jak szybko zmienia się temperatura na płytce drukowanej.Strefa podgrzewania wstępnego jest często najdłuższą ze stref i często określa szybkość narastania.Szybkość narastania wynosi zwykle od 1,0°C do 3,0°C na sekundę, często spada od 2,0°C do 3,0°C (4°F do 5°F) na sekundę.Jeśli prędkość przekracza maksymalne nachylenie, może wystąpić uszkodzenie komponentów w wyniku szoku termicznego lub pęknięć.
Pasta lutownicza może również powodować rozpryskiwanie.Sekcja podgrzewania wstępnego to miejsce, w którym rozpuszczalnik z pasty zaczyna odparowywać i jeśli szybkość wzrostu (lub poziom temperatury) jest zbyt niska, odparowanie substancji lotnych topnika jest niecałkowite.
Strefa wygrzewania termicznego
Druga sekcja, wygrzewanie termiczne, to zazwyczaj ekspozycja trwająca od 60 do 120 sekund w celu usunięcia substancji lotnych pasty lutowniczej i aktywacji topników (patrz topnik), podczas której składniki topnika rozpoczynają redukcję tlenków na przewodach i podkładkach komponentów.Zbyt wysoka temperatura może prowadzić do odprysków lub kulek lutowia, a także utlenienia pasty, pól mocujących i zakończeń elementów.
Podobnie topniki mogą nie zostać w pełni aktywowane, jeśli temperatura jest zbyt niska.Na końcu strefy wygrzewania pożądana jest równowaga termiczna całego zestawu tuż przed strefą rozpływu.Sugeruje się profil namaczania, aby zmniejszyć różnicę T pomiędzy komponentami o różnych rozmiarach lub jeśli zespół PCB jest bardzo duży.Zaleca się również profil namaczania, aby zmniejszyć puste przestrzenie w opakowaniach typu Area Array.
Strefa rozpływu
Trzecia sekcja, strefa rozpływu, nazywana jest także „czasem powyżej rozpływu” lub „czasem powyżej likwidusu” (TAL) i stanowi część procesu, w której osiągana jest maksymalna temperatura.Ważnym czynnikiem jest temperatura szczytowa, która jest maksymalną dopuszczalną temperaturą całego procesu.Typowa temperatura szczytowa wynosi 20–40 °C powyżej likwidusu. Limit ten jest wyznaczany przez element zespołu o najniższej tolerancji na wysokie temperatury (element najbardziej podatny na uszkodzenia termiczne).Standardową wytyczną jest odejmowanie 5°C od maksymalnej temperatury, jaką może wytrzymać najbardziej wrażliwy element, aby osiągnąć maksymalną temperaturę procesu.Ważne jest monitorowanie temperatury procesu, aby nie przekroczyła ona tego limitu.
Dodatkowo wysokie temperatury (powyżej 260°C) mogą powodować uszkodzenia wewnętrznych matryc elementów SMT, a także sprzyjać wzrostowi międzymetalicznemu.I odwrotnie, zbyt niska temperatura może uniemożliwić odpowiednie rozpływanie się pasty.
Czas powyżej likwidusu (TAL) lub czas powyżej rozpływu mierzy, jak długo lut jest cieczą.Topnik zmniejsza napięcie powierzchniowe na stykach metali, aby uzyskać wiązanie metalurgiczne, umożliwiając połączenie poszczególnych kulek proszku lutowniczego.Jeśli czas trwania profilu przekracza specyfikację producenta, skutkiem może być przedwczesna aktywacja lub zużycie topnika, skutecznie „wysuszając” pastę przed utworzeniem złącza lutowniczego.Niewystarczający stosunek czasu do temperatury powoduje zmniejszenie działania czyszczącego topnika, co skutkuje słabym zwilżaniem, niewystarczającym usuwaniem rozpuszczalnika i topnika i prawdopodobnie wadliwymi połączeniami lutowniczymi.
Eksperci zwykle zalecają najkrótszy możliwy TAL, jednak w większości past określa się minimalny TAL na 30 sekund, chociaż wydaje się, że nie ma jasnego powodu dla takiego konkretnego czasu.Jedną z możliwości jest to, że na płytce PCB znajdują się miejsca, które nie są mierzone podczas profilowania, dlatego ustawienie minimalnego dopuszczalnego czasu na 30 sekund zmniejsza ryzyko, że niezmierzony obszar nie rozpłynie się ponownie.Wysoki minimalny czas rozpływu zapewnia również margines bezpieczeństwa przed zmianami temperatury piekarnika.Czas zwilżania w idealnym przypadku pozostaje poniżej 60 sekund powyżej likwidusu.Dodatkowy czas powyżej likwidusu może spowodować nadmierny narost międzymetaliczny, co może prowadzić do łamliwości spoin.Płyta i komponenty mogą również ulec uszkodzeniu w dłuższym czasie w wyniku likwidusu, a większość komponentów ma dobrze określony limit czasu, w jakim mogą być wystawione na działanie temperatur przekraczających dane maksimum.
Zbyt krótki czas powyżej likwidusu może spowodować zatrzymanie rozpuszczalników i topnika, co może spowodować powstanie zimnych lub stępionych połączeń, a także pustek lutowniczych.
Strefa chłodzenia
Ostatnia strefa to strefa chłodzenia, w której następuje stopniowe schładzanie obrobionej płyty i utwardzanie połączeń lutowanych.Właściwe chłodzenie zapobiega nadmiernemu tworzeniu się międzymetali lub szokowi termicznemu komponentów.Typowe temperatury w strefie chłodzenia wahają się od 30–100 ° C (86–212 ° F).Wybrano dużą szybkość chłodzenia, aby utworzyć drobnoziarnistą strukturę, która jest najbardziej wytrzymała mechanicznie.
[1] W przeciwieństwie do maksymalnej szybkości narastania, często ignoruje się prędkość zwalniania.Może się zdarzyć, że prędkość narastania będzie mniej krytyczna powyżej pewnych temperatur, jednakże maksymalne dopuszczalne nachylenie dla dowolnego komponentu powinno obowiązywać niezależnie od tego, czy komponent się nagrzewa, czy schładza.Powszechnie sugeruje się szybkość chłodzenia 4°C/s.Jest to parametr, który należy wziąć pod uwagę analizując wyniki procesu.
Termin „rozpływ” jest używany w odniesieniu do temperatury, powyżej której stała masa stopu lutowniczego z pewnością się stopi (a nie tylko zmięknie).Jeśli zostanie schłodzony poniżej tej temperatury, lut nie będzie płynął.Po ponownym ogrzaniu lutowie znów zacznie płynąć - stąd „ponowny przepływ”.
Nowoczesne techniki montażu obwodów wykorzystujące lutowanie rozpływowe niekoniecznie pozwalają na wielokrotny przepływ lutu.Gwarantują, że granulat lutowniczy zawarty w paście lutowniczej przekracza temperaturę rozpływu stosowanego lutowia.
Profilowanie termiczne
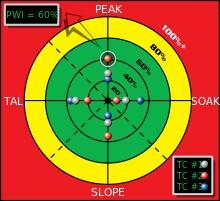
Graficzna reprezentacja indeksu okna procesu dla profilu termicznego.
W przemyśle elektronicznym miara statystyczna, znana jako wskaźnik okna procesu (PWI), służy do ilościowego określenia odporności procesu termicznego.PWI pomaga zmierzyć, jak dobrze proces „wpasowuje się” w zdefiniowany przez użytkownika limit procesu, zwany limitem specyfikacji. Każdy profil termiczny jest klasyfikowany na podstawie tego, jak „wpasowuje się” w okno procesu (specyfikacja lub granica tolerancji).
Środek okna procesu definiuje się jako zero, a skrajną krawędź okna procesu jako 99%. PWI większy lub równy 100% wskazuje, że profil nie przetwarza produktu zgodnie ze specyfikacją.PWI wynoszący 99% wskazuje, że profil przetwarza produkt zgodnie ze specyfikacją, ale działa na krawędzi okna procesu.PWI wynoszący 60% wskazuje, że profil wykorzystuje 60% specyfikacji procesu.Korzystając z wartości PWI, producenci mogą określić, jaką część okna procesowego wykorzystuje dany profil termiczny.Niższa wartość PWI wskazuje na solidniejszy profil.
Aby uzyskać maksymalną wydajność, obliczane są oddzielne wartości PWI dla procesów szczytu, nachylenia, rozpływu i wygrzewania profilu termicznego.Aby uniknąć możliwości wystąpienia szoku termicznego wpływającego na moc wyjściową, należy określić i wyrównać najbardziej strome nachylenie profilu termicznego.Producenci korzystają ze specjalnie opracowanego oprogramowania, aby dokładnie określić i zmniejszyć nachylenie zbocza.Ponadto oprogramowanie automatycznie ponownie kalibruje wartości PWI dla procesów szczytu, nachylenia, rozpływu i wygrzewania.Ustawiając wartości PWI, inżynierowie mogą zapewnić, że lutowanie rozpływowe nie przegrzeje się ani nie ochłodzi zbyt szybko.
Czas publikacji: 01 marca 2022 r