Lipirea prin reflow este un proces în care o pastă de lipire (un amestec lipicios de lipire sub formă de pulbere și flux) este utilizată pentru a atașa temporar una sau mai multe componente electrice pe plăcuțele lor de contact, după care întregul ansamblu este supus la căldură controlată, care topește lipirea. , legând permanent îmbinarea.Încălzirea poate fi realizată prin trecerea ansamblului printr-un cuptor cu reflow sau sub o lampă cu infraroșu sau prin lipirea îmbinărilor individuale cu un creion cu aer cald.
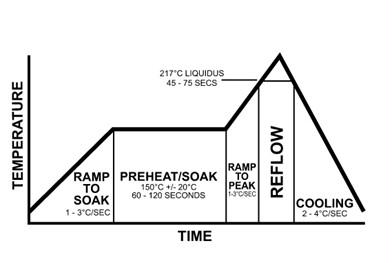
Lipirea prin reflow este cea mai comună metodă de atașare a componentelor de montare pe suprafață la o placă de circuit, deși poate fi folosită și pentru componentele cu orificii prin umplerea găurilor cu pastă de lipit și introducerea cablurilor componente prin pastă.Deoarece lipirea prin valuri poate fi mai simplă și mai ieftină, reflow nu este utilizat în general pe plăci cu orificii pur și simplu.Când este utilizat pe plăci care conțin un amestec de componente SMT și THT, reflow prin orificiu permite eliminarea etapei de lipire prin val din procesul de asamblare, reducând potențial costurile de asamblare.
Scopul procesului de reflow este de a topi lipirea și de a încălzi suprafețele adiacente, fără a supraîncălzi și a deteriora componentele electrice.În procesul convențional de lipire prin reflow, există de obicei patru etape, numite „zone”, fiecare având un profil termic distinct: preîncălzire, înmuiere termică (adesea scurtată la doar înmuiere), reflux și răcire.
Zona de preîncălzire
Panta maximă este o relație temperatură/timp care măsoară cât de repede se schimbă temperatura de pe placa de circuit imprimat.Zona de preîncălzire este adesea cea mai lungă dintre zone și adesea stabilește rata de rampă.Rata de accelerare este de obicei între 1,0 °C și 3,0 °C pe secundă, adesea scăzând între 2,0 °C și 3,0 °C (4 °F până la 5 °F) pe secundă.Dacă rata depășește panta maximă, pot apărea deteriorarea componentelor din cauza șocului termic sau crăparea.
Pasta de lipit poate avea, de asemenea, efect de stropire.Secțiunea de preîncălzire este locul în care solventul din pastă începe să se evapore, iar dacă rata de creștere (sau nivelul temperaturii) este prea scăzută, evaporarea substanțelor volatile de flux este incompletă.
Zona de inmuiere termica
A doua secțiune, înmuierea termică, este în mod obișnuit o expunere de 60 până la 120 de secunde pentru îndepărtarea substanțelor volatile ale pastei de lipit și activarea fluxurilor (vezi flux), unde componentele fluxului încep oxidarea pe cablurile și plăcuțele componente.O temperatură prea ridicată poate duce la stropirea sau formarea lipirii, precum și la oxidarea pastei, a plăcuțelor de atașare și a terminațiilor componentelor.
În mod similar, fluxurile pot să nu se activeze complet dacă temperatura este prea scăzută.La sfârșitul zonei de înmuiere este de dorit un echilibru termic al întregului ansamblu chiar înainte de zona de reflux.Se sugerează un profil de înmuiere pentru a reduce orice delta T între componente de dimensiuni diferite sau dacă ansamblul PCB este foarte mare.Un profil de înmuiere este, de asemenea, recomandat pentru a diminua golirea în pachetele de tip matrice de zonă.
Zona de reflux
Cea de-a treia secțiune, zona de reflux, este denumită și „timpul deasupra refluxului” sau „timpul deasupra lichidului” (TAL) și este partea procesului în care se atinge temperatura maximă.Un aspect important este temperatura de vârf, care este temperatura maximă admisă a întregului proces.O temperatură de vârf comună este de 20–40 °C peste lichidus. Această limită este determinată de componenta de pe ansamblu cu cea mai scăzută toleranță la temperaturi ridicate (componenta cea mai susceptibilă la deteriorarea termică).Un ghid standard este de a scădea 5 °C din temperatura maximă pe care o poate suporta componenta cea mai vulnerabilă pentru a ajunge la temperatura maximă pentru proces.Este important să monitorizați temperatura procesului pentru a nu depăși această limită.
În plus, temperaturile ridicate (peste 260 °C) pot provoca deteriorarea matrițelor interne ale componentelor SMT și pot favoriza creșterea intermetalice.Dimpotrivă, o temperatură care nu este suficient de fierbinte poate împiedica pasta să refunde în mod adecvat.
Timpul deasupra lichidului (TAL), sau timpul peste reflow, măsoară cât timp lipirea este lichidă.Fluxul reduce tensiunea superficială la joncțiunea metalelor pentru a realiza lipirea metalurgică, permițând sferelor individuale de pulbere de lipit să se combine.Dacă timpul profilului depășește specificațiile producătorului, rezultatul poate fi activarea sau consumul prematur al fluxului, „uscând” efectiv pasta înainte de formarea îmbinării de lipit.O relație insuficientă timp/temperatură determină o scădere a acțiunii de curățare a fluxului, având ca rezultat umezirea slabă, îndepărtarea inadecvată a solventului și a fluxului și posibil îmbinări de lipire defecte.
Experții recomandă de obicei cel mai scurt TAL posibil, cu toate acestea, majoritatea pastelor specifică un TAL minim de 30 de secunde, deși pare să nu existe un motiv clar pentru acel timp specific.O posibilitate este că există locuri pe PCB care nu sunt măsurate în timpul profilării și, prin urmare, setarea timpului minim admisibil la 30 de secunde reduce șansele ca o zonă nemăsurată să nu se revarsă.Un timp minim mare de refluere oferă, de asemenea, o marjă de siguranță împotriva schimbărilor de temperatură a cuptorului.În mod ideal, timpul de umectare rămâne sub 60 de secunde peste lichidus.Timpul suplimentar peste lichidus poate provoca o creștere intermetalica excesivă, ceea ce poate duce la fragilitatea articulațiilor.Placa și componentele pot fi, de asemenea, deteriorate în perioade lungi de timp peste lichidus, iar majoritatea componentelor au o limită de timp bine definită pentru cât timp pot fi expuse la temperaturi peste un anumit maxim.
Prea puțin timp deasupra lichidus poate capta solvenții și fluxul și poate crea potențialul pentru îmbinări reci sau plictisitoare, precum și goluri de lipire.
Zona de racire
Ultima zonă este o zonă de răcire pentru a răci treptat placa prelucrată și a solidifica îmbinările de lipit.Răcirea adecvată inhibă formarea intermetalice în exces sau șocul termic asupra componentelor.Temperaturile tipice în zona de răcire variază între 30–100 °C (86–212 °F).Se alege o viteză de răcire rapidă pentru a crea o structură cu granulație fină, care este cea mai bună din punct de vedere mecanic.
[1] Spre deosebire de rata maximă de accelerare, rata de ramp-down este adesea ignorată.Este posibil ca rata rampei să fie mai puțin critică peste anumite temperaturi, totuși, panta maximă admisă pentru orice componentă ar trebui să se aplice indiferent dacă componenta se încălzește sau se răcește.Se sugerează de obicei o viteză de răcire de 4°C/s.Este un parametru de luat în considerare atunci când se analizează rezultatele procesului.
Termenul "reflow" este folosit pentru a se referi la temperatura peste care o masă solidă de aliaj de lipit este sigur că se va topi (spre deosebire de a se înmuia pur și simplu).Dacă este răcit sub această temperatură, lipirea nu va curge.Încălzită deasupra ei încă o dată, lipirea va curge din nou - deci „reflux”.
Tehnicile moderne de asamblare a circuitelor care folosesc lipirea prin reflow nu permit neapărat lipirii să curgă de mai multe ori.Acestea garantează că lipirea granulată conținută în pasta de lipit depășește temperatura de reflux a lipitului implicat.
Profilare termică
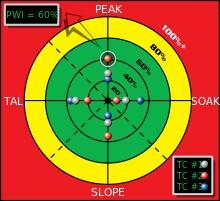
O reprezentare grafică a Indexului ferestrei de proces pentru un profil termic.
În industria de fabricare a electronicelor, o măsură statistică, cunoscută sub numele de Process Window Index (PWI) este utilizată pentru a cuantifica robustețea unui proces termic.PWI ajută la măsurarea cât de bine „se potrivește” un proces într-o limită de proces definită de utilizator, cunoscută sub numele de Limită de specificație. Fiecare profil termic este clasificat în funcție de modul în care „se potrivește” într-o fereastră de proces (limita de specificație sau toleranță).
Centrul ferestrei de proces este definit ca zero, iar marginea extremă a ferestrei de proces ca 99%. Un PWI mai mare sau egal cu 100% indică faptul că profilul nu procesează produsul conform specificațiilor.Un PWI de 99% indică faptul că profilul procesează produsul conform specificațiilor, dar rulează la marginea ferestrei de proces.Un PWI de 60% indică că un profil utilizează 60% din specificația procesului.Utilizând valorile PWI, producătorii pot determina cât de mult din fereastra de proces folosește un anumit profil termic.O valoare PWI mai mică indică un profil mai robust.
Pentru o eficiență maximă, valorile PWI separate sunt calculate pentru procesele de vârf, pantă, reflux și înmuiere ale unui profil termic.Pentru a evita posibilitatea ca șoc termic să afecteze puterea, trebuie determinată și nivelată cea mai abruptă pantă din profilul termic.Producătorii folosesc software personalizat pentru a determina și a reduce cu precizie abruptul pantei.În plus, software-ul recalibrează automat valorile PWI pentru procesele de vârf, pantă, reflux și înmuiere.Prin setarea valorilor PWI, inginerii se pot asigura că lucrările de lipire prin reflow nu se supraîncălzi sau nu se răcesc prea repede.
Ora postării: 01-03-2022