Пайка оплавлением — это процесс, при котором паяльная паста (клейкая смесь порошкообразного припоя и флюса) используется для временного прикрепления одного или нескольких электрических компонентов к их контактным площадкам, после чего вся сборка подвергается контролируемому нагреву, в результате чего припой плавится. , навсегда соединяя сустав.Нагрев может быть осуществлен путем пропускания узла через печь оплавления или под инфракрасной лампой или путем пайки отдельных соединений карандашом с горячим воздухом.
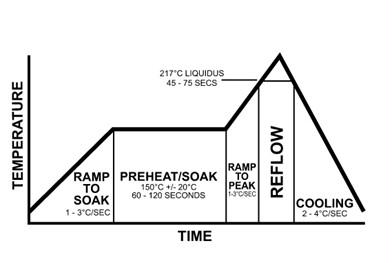
Пайка оплавлением является наиболее распространенным методом крепления компонентов для поверхностного монтажа к печатной плате, хотя ее также можно использовать для компонентов со сквозными отверстиями, заполняя отверстия паяльной пастой и вставляя выводы компонентов через пасту.Поскольку пайка волновой пайкой может быть проще и дешевле, оплавление обычно не используется на платах со сквозными отверстиями.При использовании на платах, содержащих компоненты SMT и THT, оплавление сквозных отверстий позволяет исключить этап пайки волновой пайкой из процесса сборки, что потенциально снижает затраты на сборку.
Цель процесса оплавления — расплавить припой и нагреть прилегающие поверхности, не перегревая и не повреждая электрические компоненты.В обычном процессе пайки оплавлением обычно есть четыре этапа, называемых «зонами», каждый из которых имеет отдельный термический профиль: предварительный нагрев, термическая выдержка (часто сокращается до простого выдержки), оплавление и охлаждение.
Зона предварительного нагрева
Максимальный наклон — это соотношение температуры и времени, которое измеряет, насколько быстро изменяется температура на печатной плате.Зона предварительного нагрева часто является самой длинной из зон и часто определяет скорость изменения температуры.Скорость нарастания обычно составляет от 1,0 °C до 3,0 °C в секунду, часто падая от 2,0 °C до 3,0 °C (от 4 °F до 5 °F) в секунду.Если скорость превышает максимальный наклон, может произойти повреждение компонентов в результате термического удара или растрескивания.
Паяльная паста также может иметь эффект разбрызгивания.В секции предварительного нагрева растворитель в пасте начинает испаряться, и если скорость повышения (или уровень температуры) слишком низкая, испарение летучих веществ флюса будет неполным.
Зона термического замачивания
Второй этап, термическая выдержка, обычно представляет собой выдержку продолжительностью от 60 до 120 секунд для удаления летучих веществ паяльной пасты и активации флюсов (см. флюс), когда компоненты флюса начинают восстановление оксидов на выводах и контактных площадках компонентов.Слишком высокая температура может привести к разбрызгиванию или комкованию припоя, а также к окислению пасты, монтажных площадок и выводов компонентов.
Аналогично, флюсы могут не активироваться полностью, если температура слишком низкая.В конце зоны выдержки желательно достичь теплового равновесия всей сборки непосредственно перед зоной оплавления.Профиль выдержки рекомендуется для уменьшения разницы температур между компонентами разных размеров или в случае, если сборка печатной платы очень велика.Профиль выдержки также рекомендуется для уменьшения образования пустот в упаковках типа массива.
Зона оплавления
Третья секция, зона оплавления, также называется «временем выше оплавления» или «временем выше ликвидуса» (TAL) и представляет собой часть процесса, где достигается максимальная температура.Важным фактором является пиковая температура, которая является максимально допустимой температурой всего процесса.Обычно пиковая температура составляет 20–40 °C выше ликвидуса. Этот предел определяется компонентом сборки с наименьшей устойчивостью к высоким температурам (компонент, наиболее подверженный термическому повреждению).Стандартная рекомендация состоит в том, чтобы вычесть 5 °C из максимальной температуры, которую может выдержать наиболее уязвимый компонент, чтобы получить максимальную температуру для процесса.Важно следить за температурой процесса, чтобы она не превышала этот предел.
Кроме того, высокие температуры (более 260 °C) могут привести к повреждению внутренних штампов SMT-компонентов, а также способствовать росту интерметаллидов.И наоборот, недостаточно высокая температура может помешать пасте адекватно оплавиться.
Время выше ликвидуса (TAL) или время выше оплавления измеряет, как долго припой находится в жидком состоянии.Флюс снижает поверхностное натяжение на стыке металлов, обеспечивая металлургическое соединение, позволяя отдельным сферам припоя соединяться.Если время профиля превышает спецификации производителя, результатом может стать преждевременная активация или расходование флюса, что приводит к эффективному «высыханию» пасты перед формированием паяного соединения.Недостаточное соотношение времени и температуры приводит к снижению очищающего действия флюса, что приводит к плохому смачиванию, недостаточному удалению растворителя и флюса и, возможно, к дефектам паяных соединений.
Эксперты обычно рекомендуют максимально короткий TAL, однако в большинстве паст указывается минимальный TAL, равный 30 секундам, хотя, похоже, нет четкой причины для такого конкретного времени.Одна из возможностей заключается в том, что на печатной плате есть места, которые не измеряются во время профилирования, и поэтому установка минимально допустимого времени в 30 секунд снижает вероятность того, что неизмеренная область не будет перекомпонована.Высокое минимальное время оплавления также обеспечивает запас прочности при изменении температуры в печи.Время смачивания в идеале должно оставаться ниже 60 секунд выше уровня ликвидуса.Дополнительное время выше ликвидуса может вызвать чрезмерный рост интерметаллидов, что может привести к хрупкости соединения.Плата и компоненты также могут быть повреждены в течение длительного времени, превышающего ликвидус, и у большинства компонентов есть четко определенный временной предел, в течение которого они могут подвергаться воздействию температур, превышающих заданный максимум.
Слишком малое время выше уровня ликвидуса может привести к задержке растворителей и флюса и создать вероятность холодных или тусклых соединений, а также пустот при припое.
Зона охлаждения
Последняя зона представляет собой зону охлаждения для постепенного охлаждения обрабатываемой платы и затвердевания паяных соединений.Правильное охлаждение препятствует избыточному интерметаллидному образованию или термическому удару компонентов.Типичные температуры в зоне охлаждения составляют 30–100 ° C (86–212 ° F).Высокая скорость охлаждения выбирается для создания мелкозернистой структуры, наиболее механически прочной.
[1] В отличие от максимальной скорости нарастания, скорость торможения часто игнорируется.Возможно, скорость изменения температуры менее критична выше определенных температур, однако максимально допустимый наклон для любого компонента должен применяться независимо от того, нагревается или остывает компонент.Обычно предлагается скорость охлаждения 4°C/с.Это параметр, который следует учитывать при анализе результатов процесса.
Термин «оплавления» используется для обозначения температуры, выше которой твердая масса припоя наверняка плавится (а не просто размягчается).При охлаждении ниже этой температуры припой не будет течь.Нагревшись над ним еще раз, припой снова потечет - отсюда и «повторное течение».
Современные методы сборки схем, в которых используется пайка оплавлением, не обязательно позволяют припою течь более одного раза.Они гарантируют, что гранулированный припой, содержащийся в паяльной пасте, превосходит температуру оплавления используемого припоя.
Термическое профилирование
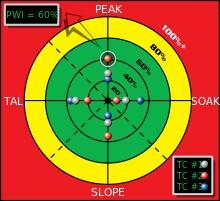
Графическое представление индекса окна процесса для теплового профиля.
В электронной промышленности для количественной оценки устойчивости теплового процесса используется статистический показатель, известный как индекс окна процесса (PWI).PWI помогает измерить, насколько хорошо процесс «вписывается» в заданный пользователем предел процесса, известный как предел спецификации. Каждый тепловой профиль ранжируется по тому, насколько он «вписывается» в окно процесса (спецификация или предел допуска).
Центр окна процесса определяется как ноль, а крайний край окна процесса — как 99%. PWI больше или равно 100 % означает, что профиль не обрабатывает продукт в пределах спецификации.PWI, равный 99 %, указывает на то, что профиль обрабатывает продукт в пределах спецификации, но выполняется на границе окна процесса.PWI, равный 60 %, означает, что профиль использует 60 % спецификации процесса.Используя значения PWI, производители могут определить, какую часть технологического окна использует конкретный тепловой профиль.Более низкое значение PWI указывает на более надежный профиль.
Для максимальной эффективности отдельные значения PWI рассчитываются для процессов пика, наклона, оплавления и выдержки термического профиля.Чтобы избежать возможности термического шока, влияющего на выходную мощность, необходимо определить и выровнять самый крутой наклон температурного профиля.Производители используют специальное программное обеспечение для точного определения и уменьшения крутизны уклона.Кроме того, программное обеспечение также автоматически перекалибровывает значения PWI для процессов пика, наклона, оплавления и выдержки.Установив значения PWI, инженеры могут гарантировать, что пайка оплавлением не перегреется и не остынет слишком быстро.
Время публикации: 01 марта 2022 г.