การบัดกรีแบบรีโฟลว์เป็นกระบวนการที่ใช้การบัดกรี (ส่วนผสมเหนียวของผงบัดกรีและฟลักซ์) เพื่อติดส่วนประกอบไฟฟ้าหนึ่งหรือหลายชิ้นเข้ากับแผ่นสัมผัสชั่วคราว หลังจากนั้นส่วนประกอบทั้งหมดจะถูกควบคุมด้วยความร้อน ซึ่งจะทำให้โลหะบัดกรีละลาย เชื่อมข้อต่ออย่างถาวรการทำความร้อนอาจทำได้โดยการส่งชุดประกอบผ่านเตาอบแบบรีโฟลว์หรือใต้หลอดไฟอินฟราเรด หรือโดยการบัดกรีข้อต่อแต่ละจุดด้วยดินสอลมร้อน
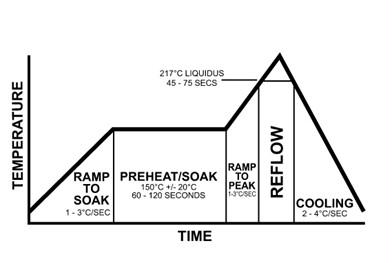
การบัดกรีแบบ Reflow เป็นวิธีการทั่วไปในการติดส่วนประกอบที่ยึดบนพื้นผิวเข้ากับแผงวงจร แม้ว่าจะสามารถใช้กับส่วนประกอบที่มีรูทะลุได้โดยการเติมรูด้วยสารบัดกรีและสอดส่วนประกอบที่นำไปสู่ผ่านส่วนผสมเนื่องจากการบัดกรีแบบคลื่นทำได้ง่ายกว่าและราคาถูกกว่า โดยทั่วไปจึงไม่มีการใช้การรีโฟลว์กับบอร์ดทะลุรูล้วนๆเมื่อใช้กับบอร์ดที่มีส่วนประกอบ SMT และ THT ผสมกัน การรีโฟลว์ผ่านรูช่วยให้ขั้นตอนการบัดกรีแบบคลื่นถูกกำจัดออกจากกระบวนการประกอบ ซึ่งอาจช่วยลดต้นทุนการประกอบได้
เป้าหมายของกระบวนการรีโฟลว์คือการหลอมโลหะบัดกรีและให้ความร้อนแก่พื้นผิวที่อยู่ติดกัน โดยไม่ทำให้อุปกรณ์ไฟฟ้าเสียหายจนเกินไปในกระบวนการบัดกรีแบบรีโฟลว์แบบทั่วไป โดยปกติแล้วจะมีสี่ขั้นตอนที่เรียกว่า "โซน" ซึ่งแต่ละขั้นตอนจะมีโปรไฟล์ความร้อนที่แตกต่างกัน: อุ่น การแช่ด้วยความร้อน (มักเรียกสั้น ๆ ว่าแค่แช่) การรีโฟลว์ และการทำให้เย็นลง
อุ่นโซน
ความชันสูงสุดคือความสัมพันธ์ของอุณหภูมิ/เวลาที่วัดว่าอุณหภูมิบนแผงวงจรพิมพ์เปลี่ยนแปลงเร็วเพียงใดโซนอุ่นเครื่องมักจะเป็นโซนที่ยาวที่สุดของโซน และมักจะกำหนดอัตราการเปลี่ยนความเร็วอัตราการเพิ่มปกติจะอยู่ระหว่าง 1.0 °C ถึง 3.0 °C ต่อวินาที ซึ่งมักจะลดลงระหว่าง 2.0 °C ถึง 3.0 °C (4 °F ถึง 5 °F) ต่อวินาทีหากอัตราเกินความชันสูงสุด อาจเกิดความเสียหายต่อส่วนประกอบจากการเปลี่ยนแปลงอุณหภูมิหรือรอยแตกร้าวได้
สารบัดกรียังสามารถทำให้เกิดประกายไฟได้ส่วนอุ่นเครื่องคือจุดที่ตัวทำละลายในส่วนผสมเริ่มระเหย และหากอัตราการเพิ่มขึ้น (หรือระดับอุณหภูมิ) ต่ำเกินไป การระเหยของสารระเหยฟลักซ์จะไม่สมบูรณ์
โซนแช่ความร้อน
ส่วนที่สอง การแช่ด้วยความร้อน โดยทั่วไปจะใช้เวลา 60 ถึง 120 วินาทีในการกำจัดสารระเหยของสารบัดกรีและการกระตุ้นฟลักซ์ (ดูฟลักซ์) ซึ่งส่วนประกอบของฟลักซ์เริ่มลดการเกิดออกไซด์บนตัวนำและแผ่นส่วนประกอบอุณหภูมิที่สูงเกินไปอาจทำให้บัดกรีกระเด็นหรือเป็นก้อน รวมถึงการเกิดออกซิเดชันของเพสต์ แผ่นยึดติด และปลายส่วนประกอบ
ในทำนองเดียวกัน ฟลักซ์อาจไม่ทำงานเต็มที่หากอุณหภูมิต่ำเกินไปในตอนท้ายของโซนแช่ ต้องการสมดุลทางความร้อนของส่วนประกอบทั้งหมดก่อนถึงโซนการไหลซ้ำแนะนำให้ใช้โปรไฟล์การแช่เพื่อลดเดลต้า T ระหว่างส่วนประกอบที่มีขนาดแตกต่างกัน หรือหากชุดประกอบ PCB มีขนาดใหญ่มากแนะนำให้ใช้โปรไฟล์การแช่เพื่อลดช่องว่างในแพ็คเกจประเภทอาเรย์พื้นที่
โซนรีโฟลว์
ส่วนที่สาม โซนการไหลซ้ำ ยังเรียกอีกอย่างว่า "เวลาที่อยู่เหนือการไหลซ้ำ" หรือ "เวลาที่อยู่เหนือของเหลว" (TAL) และเป็นส่วนหนึ่งของกระบวนการเมื่อถึงอุณหภูมิสูงสุดข้อควรพิจารณาที่สำคัญคืออุณหภูมิสูงสุด ซึ่งเป็นอุณหภูมิสูงสุดที่อนุญาตของกระบวนการทั้งหมดอุณหภูมิสูงสุดโดยทั่วไปคือ 20–40 °C เหนือของเหลว ขีดจำกัดนี้กำหนดโดยส่วนประกอบบนชิ้นส่วนประกอบที่มีความทนต่ออุณหภูมิสูงต่ำที่สุด (ส่วนประกอบที่เสี่ยงต่อความเสียหายจากความร้อนมากที่สุด)แนวทางมาตรฐานคือการลบ 5 °C ออกจากอุณหภูมิสูงสุดที่ส่วนประกอบที่เปราะบางที่สุดสามารถคงอยู่ได้เพื่อให้ได้อุณหภูมิสูงสุดสำหรับกระบวนการสิ่งสำคัญคือต้องตรวจสอบอุณหภูมิของกระบวนการเพื่อไม่ให้เกินขีดจำกัดนี้
นอกจากนี้ อุณหภูมิที่สูง (เกิน 260 °C) อาจทำให้เกิดความเสียหายต่อแม่พิมพ์ภายในของส่วนประกอบ SMT รวมทั้งส่งเสริมการเติบโตของโลหะระหว่างกันในทางกลับกัน อุณหภูมิที่ไม่ร้อนพออาจทำให้ส่วนผสมไม่ไหลออกมาได้เพียงพอ
เวลาเหนือของเหลว (TAL) หรือเวลาเหนือการไหลกลับจะวัดระยะเวลาที่โลหะบัดกรีเป็นของเหลวฟลักซ์จะช่วยลดแรงตึงผิวที่จุดเชื่อมต่อของโลหะเพื่อให้เกิดการยึดเหนี่ยวทางโลหะวิทยา ซึ่งช่วยให้ผงทรงกลมของโลหะบัดกรีแต่ละตัวรวมกันได้หากเวลาโปรไฟล์เกินกว่าข้อกำหนดของผู้ผลิต ผลลัพธ์อาจเป็นการเปิดใช้งานหรือการใช้ฟลักซ์ก่อนเวลาอันควร ซึ่งจะทำให้ "แห้ง" ส่วนผสมได้อย่างมีประสิทธิภาพก่อนที่จะเกิดข้อต่อประสานความสัมพันธ์ระหว่างเวลา/อุณหภูมิที่ไม่เพียงพอทำให้การทำความสะอาดฟลักซ์ลดลง ส่งผลให้เปียกได้ไม่ดี การกำจัดตัวทำละลายและฟลักซ์ไม่เพียงพอ และข้อต่อบัดกรีอาจมีข้อบกพร่อง
ผู้เชี่ยวชาญมักแนะนำให้ใช้ TAL ที่สั้นที่สุดเท่าที่จะเป็นไปได้ อย่างไรก็ตาม Paste ส่วนใหญ่จะระบุ TAL ขั้นต่ำไว้ที่ 30 วินาที แม้ว่าดูเหมือนจะไม่มีเหตุผลที่ชัดเจนสำหรับช่วงเวลานั้นก็ตามความเป็นไปได้ประการหนึ่งก็คือ มีตำแหน่งบน PCB ที่ไม่ได้ถูกวัดระหว่างการทำโปรไฟล์ ดังนั้น การตั้งเวลาขั้นต่ำที่อนุญาตไว้ที่ 30 วินาทีจะช่วยลดโอกาสที่พื้นที่ที่ไม่ได้วัดจะไม่ไหลซ้ำเวลาการไหลซ้ำขั้นต่ำที่สูงยังช่วยเพิ่มความปลอดภัยต่อการเปลี่ยนแปลงอุณหภูมิของเตาอบอีกด้วยเวลาในการทำให้เปียกควรอยู่ต่ำกว่า 60 วินาทีเหนือของเหลวเวลาเพิ่มเติมเหนือ liquidus อาจทำให้เกิดการเจริญเติบโตระหว่างโลหะมากเกินไป ซึ่งอาจนำไปสู่ความเปราะบางของข้อต่อได้บอร์ดและส่วนประกอบอาจเสียหายเป็นเวลานานกว่าลิควิดัส และส่วนประกอบส่วนใหญ่มีกำหนดเวลาที่ชัดเจนสำหรับระยะเวลาที่ชิ้นส่วนอาจสัมผัสกับอุณหภูมิเกินค่าสูงสุดที่กำหนด
เวลาเหนือของเหลวน้อยเกินไปอาจดักจับตัวทำละลายและฟลักซ์ และสร้างโอกาสให้เกิดข้อต่อเย็นหรือหมองคล้ำตลอดจนช่องว่างของการบัดกรี
โซนทำความเย็น
โซนสุดท้ายเป็นโซนทำความเย็นเพื่อค่อยๆ ระบายความร้อนให้กับบอร์ดที่ประมวลผลและทำให้ข้อต่อบัดกรีแข็งตัวการระบายความร้อนที่เหมาะสมจะยับยั้งการก่อตัวของโลหะระหว่างโลหะมากเกินไปหรือการเปลี่ยนแปลงอุณหภูมิอย่างฉับพลันไปยังส่วนประกอบต่างๆอุณหภูมิโดยทั่วไปในเขตทำความเย็นอยู่ในช่วง 30–100 °C (86–212 °F)เลือกอัตราการทำความเย็นที่รวดเร็วเพื่อสร้างโครงสร้างเกรนที่ละเอียดซึ่งมีกลไกการทำงานดีที่สุด
[1] ต่างจากอัตราการเพิ่มความเร็วสูงสุด อัตราการลาดลงมักจะถูกละเลยอาจเป็นไปได้ว่าอัตราความชันมีความสำคัญน้อยกว่าเหนืออุณหภูมิที่กำหนด อย่างไรก็ตาม ควรใช้ความชันสูงสุดที่อนุญาตสำหรับส่วนประกอบใดๆ ไม่ว่าส่วนประกอบจะร้อนขึ้นหรือเย็นลงก็ตามโดยทั่วไปแนะนำให้ใช้อัตราการทำความเย็นที่ 4°C/sเป็นพารามิเตอร์ที่ต้องพิจารณาเมื่อวิเคราะห์ผลลัพธ์ของกระบวนการ
คำว่า "การรีโฟลว์" ใช้เพื่ออ้างถึงอุณหภูมิที่สูงกว่าซึ่งมวลของแข็งของโลหะผสมบัดกรีจะต้องละลายอย่างแน่นอนหากเย็นลงต่ำกว่าอุณหภูมินี้ โลหะบัดกรีจะไม่ไหลเมื่ออุ่นขึ้นเหนืออีกครั้ง ลวดบัดกรีจะไหลอีกครั้ง ดังนั้นจึง "ไหลใหม่"
เทคนิคการประกอบวงจรสมัยใหม่ที่ใช้การบัดกรีแบบรีโฟลว์ไม่จำเป็นต้องให้บัดกรีไหลมากกว่าหนึ่งครั้งพวกเขารับประกันว่าโลหะบัดกรีที่เป็นเม็ดที่มีอยู่ในสารประสานจะเกินกว่าอุณหภูมิการรีโฟลว์ของโลหะบัดกรีที่เกี่ยวข้อง
การทำโปรไฟล์ความร้อน
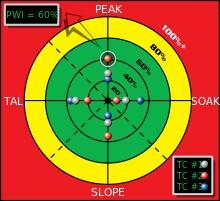
การแสดงดัชนีหน้าต่างกระบวนการแบบกราฟิกสำหรับโปรไฟล์การระบายความร้อน
ในอุตสาหกรรมการผลิตอุปกรณ์อิเล็กทรอนิกส์ การวัดทางสถิติที่เรียกว่าดัชนีหน้าต่างกระบวนการ (PWI) ถูกนำมาใช้เพื่อวัดปริมาณความทนทานของกระบวนการทางความร้อนPWI ช่วยวัดว่ากระบวนการ "พอดี" กับขีดจำกัดกระบวนการที่ผู้ใช้กำหนดได้ดีเพียงใด ซึ่งเรียกว่าขีดจำกัดข้อกำหนด โปรไฟล์การระบายความร้อนแต่ละโปรไฟล์จะถูกจัดอันดับตามวิธีที่ "พอดี" ในหน้าต่างกระบวนการ (ข้อกำหนดหรือขีดจำกัดความคลาดเคลื่อน)
ศูนย์กลางของหน้าต่างกระบวนการถูกกำหนดให้เป็นศูนย์ และขอบสุดของหน้าต่างกระบวนการคือ 99% PWI ที่มากกว่าหรือเท่ากับ 100% บ่งชี้ว่าโปรไฟล์ไม่ได้ประมวลผลผลิตภัณฑ์ตามข้อกำหนดPWI 99% บ่งชี้ว่าโปรไฟล์ประมวลผลผลิตภัณฑ์ตามข้อกำหนด แต่ทำงานที่ขอบของหน้าต่างกระบวนการPWI 60% บ่งชี้ว่าโปรไฟล์ใช้ 60% ของข้อกำหนดกระบวนการด้วยการใช้ค่า PWI ผู้ผลิตสามารถกำหนดได้ว่าโปรไฟล์การระบายความร้อนเฉพาะจะใช้กรอบเวลากระบวนการมากเพียงใดค่า PWI ที่ต่ำกว่าบ่งบอกถึงโปรไฟล์ที่แข็งแกร่งยิ่งขึ้น
เพื่อประสิทธิภาพสูงสุด จะมีการคำนวณค่า PWI ที่แยกจากกันสำหรับกระบวนการพีค ความชัน การรีโฟลว์ และการแช่ของโปรไฟล์การระบายความร้อนเพื่อหลีกเลี่ยงความเป็นไปได้ที่การเปลี่ยนแปลงของความร้อนจะส่งผลกระทบต่อเอาท์พุต จะต้องกำหนดและปรับระดับความชันที่ชันที่สุดในโปรไฟล์ความร้อนผู้ผลิตใช้ซอฟต์แวร์ที่สร้างขึ้นเองเพื่อระบุและลดความชันของทางลาดได้อย่างแม่นยำนอกจากนี้ ซอฟต์แวร์ยังปรับเทียบค่า PWI ใหม่สำหรับกระบวนการพีค ความชัน การจัดเรียงและการแช่อีกครั้งโดยอัตโนมัติด้วยการตั้งค่า PWI วิศวกรสามารถมั่นใจได้ว่างานบัดกรีแบบรีโฟลว์ไม่ร้อนเกินไปหรือเย็นลงเร็วเกินไป
เวลาโพสต์: 01-01-2022