Паяння оплавленням – це процес, у якому паяльна паста (клейка суміш порошкоподібного припою та флюсу) використовується для тимчасового прикріплення одного чи кількох електричних компонентів до їхніх контактних майданчиків, після чого весь вузол піддається контрольованому нагріванню, що плавить припій. , постійно з’єднуючи з’єднання.Нагрівання можна здійснити, пропустивши вузол через піч оплавлення або під інфрачервоною лампою, або спаявши окремі з’єднання олівцем з гарячим повітрям.
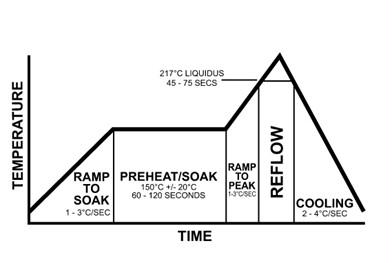
Паяння оплавленням є найпоширенішим способом прикріплення компонентів поверхневого монтажу до друкованої плати, хоча його також можна використовувати для компонентів із наскрізними отворами, заповнюючи отвори паяльною пастою та вставляючи проводи компонентів крізь пасту.Оскільки пайка хвилею може бути простішою та дешевшою, оплавлення зазвичай не використовується на платах із чистими отворами.При використанні на платах, що містять суміш компонентів SMT і THT, оплавлення через отвір дозволяє виключити етап пайки хвилею з процесу складання, що потенційно знижує витрати на складання.
Метою процесу оплавлення є розплавлення припою та нагрівання прилеглих поверхонь без перегріву та пошкодження електричних компонентів.У звичайному процесі паяння оплавленням зазвичай є чотири стадії, які називаються «зонами», кожна з яких має окремий тепловий профіль: попередній нагрів, термічний замочування (часто скорочується до просто замочування), оплавлення та охолодження.
Зона попереднього нагріву
Максимальний нахил — це співвідношення температура/час, яке вимірює швидкість зміни температури на друкованій платі.Зона попереднього нагрівання часто є найдовшою із зон і часто встановлює швидкість підвищення.Швидкість наростання зазвичай становить від 1,0 °C до 3,0 °C за секунду, часто падає від 2,0 °C до 3,0 °C (4 °F до 5 °F) за секунду.Якщо швидкість перевищує максимальний нахил, може виникнути пошкодження компонентів через термічний удар або розтріскування.
Паяльна паста також може мати ефект розбризкування.Секція попереднього нагріву – це місце, де розчинник у пасті починає випаровуватися, і якщо швидкість підйому (або рівень температури) надто низька, випаровування летких речовин флюсу буде неповним.
Термічна зона замочування
Друга секція, термічний замочування, зазвичай становить від 60 до 120 секунд витримки для видалення летких речовин паяльної пасти та активації флюсів (див. флюс), де компоненти флюсу починають окислення на виводах компонентів і майданчиках.Занадто висока температура може призвести до розбризкування або утворення кульок припою, а також до окислення пасти, кріпильних майданчиків і кінців компонентів.
Подібним чином, потоки можуть не повністю активуватися, якщо температура надто низька.Наприкінці зони витримки бажана термічна рівновага всього вузла безпосередньо перед зоною оплавлення.Пропонується профіль витримки для зменшення будь-якої дельта Т між компонентами різного розміру або якщо друкована плата дуже велика.Також рекомендується використовувати профіль замочування, щоб зменшити утворення пустот у пакетах типу масиву.
Зона оплавлення
Третя секція, зона оплавлення, також називається «часом над оплавленням» або «часом над ліквідусом» (TAL), і є частиною процесу, де досягається максимальна температура.Важливим фактором є пікова температура, яка є максимально допустимою температурою всього процесу.Загальна пікова температура на 20–40 °C вище ліквідусу. Ця межа визначається компонентом у зборі з найнижчим допуском до високих температур (компонент, найбільш чутливий до термічного пошкодження).Стандартною вказівкою є віднімання 5 °C від максимальної температури, яку може витримувати найбільш вразливий компонент, щоб отримати максимальну температуру для процесу.Важливо стежити за температурою процесу, щоб вона не перевищувала цю межу.
Крім того, високі температури (понад 260 °C) можуть спричинити пошкодження внутрішніх матриць SMT-компонентів, а також сприяти зростанню інтерметалів.І навпаки, температура, яка є недостатньо високою, може перешкодити належному розтоку пасти.
Час над ліквідусом (TAL), або час над оплавленням, вимірює, як довго припій є рідким.Флюс зменшує поверхневий натяг на стику металів для досягнення металургійного з’єднання, що дозволяє об’єднати окремі сфери порошку припою.Якщо час профілю перевищує специфікацію виробника, результатом може стати передчасна активація або витрата флюсу, що фактично «висихає» пасту перед утворенням паяного з’єднання.Недостатнє співвідношення між часом і температурою спричиняє зниження очисної дії флюсу, що призводить до поганого змочування, недостатнього видалення розчинника та флюсу та, можливо, дефектних паяних з’єднань.
Експерти зазвичай рекомендують найкоротший TAL, однак більшість паст вказують мінімальний TAL у 30 секунд, хоча, здається, немає чіткої причини для цього конкретного часу.Одна з можливостей полягає в тому, що на друкованій платі є місця, які не вимірюються під час профілювання, і тому встановлення мінімально допустимого часу до 30 секунд зменшує ймовірність того, що невиміряна ділянка не оплавиться.Високий мінімальний час оплавлення також забезпечує запас надійності проти змін температури духовки.В ідеалі час змочування залишається нижче 60 секунд вище ліквідусу.Додатковий час вище ліквідусу може спричинити надмірне зростання інтерметалів, що може призвести до крихкості з’єднань.Плата та компоненти також можуть бути пошкоджені протягом тривалого часу протягом ліквідусу, і більшість компонентів мають чітко визначений ліміт часу, протягом якого вони можуть бути піддані впливу температур вище заданого максимуму.
Занадто малий час вище ліквідусу може затримувати розчинники та флюс і створювати потенційну можливість холодних або тьмяних з’єднань, а також порожнеч під пайкою.
Зона охолодження
Остання зона - це зона охолодження для поступового охолодження обробленої плати та затвердіння паяних з'єднань.Правильне охолодження запобігає надлишковому утворенню інтерметалів або термічному удару компонентів.Типова температура в зоні охолодження коливається від 30–100 °C (86–212 °F).Швидка швидкість охолодження вибирається для створення дрібнозернистої структури, яка є найбільш механічно міцною.
[1] На відміну від максимальної швидкості наростання, швидкість зниження часто ігнорується.Може статися, що швидкість зміни температури є менш критичною при перевищенні певних температур, однак максимально допустимий нахил для будь-якого компонента має застосовуватися незалежно від того, нагрівається він чи охолоджується.Зазвичай рекомендована швидкість охолодження 4°C/с.Це параметр, який слід враховувати при аналізі результатів процесу.
Термін «оплавлення» використовується для позначення температури, вище якої тверда маса сплаву припою напевно розплавиться (на відміну від простого розм’якшення).При охолодженні нижче цієї температури припій не буде текти.Знову нагрівшись над ним, припій знову потече — отже, «повторне течення».
Сучасні методи складання схем, які використовують пайку оплавленням, не обов’язково дозволяють припою текти більше одного разу.Вони гарантують, що гранульований припій, що міститься в паяльній пасті, перевищує температуру оплавлення використовуваного припою.
Термічне профілювання
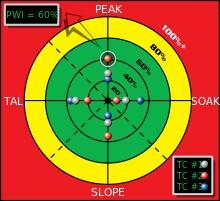
Графічне представлення індексу вікна процесу для теплового профілю.
У промисловості виробництва електроніки для кількісної оцінки стійкості теплового процесу використовується статистичний показник, відомий як індекс вікна процесу (PWI).PWI допомагає виміряти, наскільки добре процес «вписується» у визначене користувачем обмеження процесу, відоме як обмеження специфікації. Кожен тепловий профіль класифікується за тим, як він «вписується» у вікно процесу (специфікація або межа допуску).
Центр вікна процесу визначається як нуль, а крайній край вікна процесу — 99%. PWI, що перевищує або дорівнює 100%, вказує на те, що профіль не обробляє продукт у межах специфікації.PWI 99% вказує на те, що профіль обробляє продукт у межах специфікації, але працює на краю вікна процесу.PWI 60% означає, що профіль використовує 60% специфікації процесу.Використовуючи значення PWI, виробники можуть визначити, яку частину вікна процесу використовує конкретний тепловий профіль.Нижче значення PWI вказує на більш надійний профіль.
Для досягнення максимальної ефективності окремі значення PWI обчислюються для процесів піку, нахилу, оплавлення та витримки теплового профілю.Щоб уникнути впливу теплового удару на вихід, необхідно визначити та вирівняти найкрутіший схил теплового профілю.Виробники використовують спеціально створене програмне забезпечення для точного визначення та зменшення крутизни схилу.Крім того, програмне забезпечення також автоматично повторно калібрує значення PWI для процесів піку, нахилу, оплавлення та замочування.Встановлюючи значення PWI, інженери можуть гарантувати, що пайка оплавленням не перегрівається або не охолоджується занадто швидко.
Час публікації: 01.03.2022